Use Geometric Design Rules
After determining safety goals in a script in Data Setup, you can check the vertical alignment geometry according to these sag and crest
conditions.
The following design values are configured in the script:
- The lane type: one or two ways, speed, design vehicle
- Road profile: design speed, slope angle, the height of object for stopping and passing
sight distance
- Vehicle type (for example: car), design (for example: SUV), speed, the height of the
driver's eyes, headlight height, light beam divergence
- The speed of the vehicle type is taken into account for the length of the crest and
sag vertical curve.
- The curve type: arc or parabola.
Note:
If a speed has been set for the current reference key point, it will compare each
vehicle speed with the key point speed and take the lowest value as reference. If no speed
has been defined for the current key point, it will compare the vehicle speed with the
design speed of alignment and take the lowest value.
-
To check the vertical alignment according to design rules, expand the
Criteria section in the Alignment
assistant dialog box and click one or several options.
The optimization of vertical alignment is based on a combination
of the checks (different types of sight distance). Each check option will be further
detailed below.
-
To check alignment occasionally, click Check or select
Dynamic checks to launch it automatically after each design
change.
The check operation is performed to analyze the length of the crest and sag vertical
curves. For example, you can check if they are long enough to satisfy the stopping
sight distance criteria.
You obtain:
- A visualization result in the 3D area:
Check of the passing sight distance only. The curve section is colored red in the
vertical alignment. If the curves are long enough to satisfy this criteria, the
areas are green.
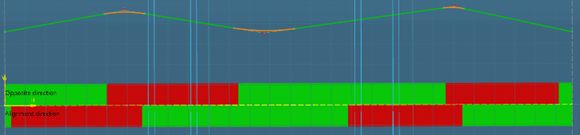
- Messages: A Message Reporting dialog box opens. When the
design rules are not supported, an error of criteria is raised. For example, you
are notified when a crest or sag does not meet the stopping distance criterion, or
when the sight distance is below 50m. The short parabola is however created and
the alignment is still valid.
-
Right-click an error and select the Fix error command.
If there is not enough space to fix the parabola length, a warning appears
giving instructions to solve the problem manually.
-
Remodel the detected areas until they meet the required safety standards.
For example, you can set the minimum value as the new crest/sag
length.
Check the Stopping Sight Distance
The sight distance is the length of the roadway ahead that is visible to the
driver. The stopping sight distance is the sum of two distances: brake reaction distance
(distance traversed by the vehicle from the instant the driver sees an object necessitating
a stop to the instant the brakes are applied) and braking distance (distance needed to stop
the vehicle from the instant the brake application begins). The stopping sight distance is
taken into account in the parabola creation. You can detect existing crests that do not meet
the stopping sight distance criterion, and improve the definition of vertical curves to
enable the driver to see the road ahead and provide the distance needed to stop the
vehicle.
-
To check the vertical alignment according to design rules, expand the
Criteria section in the Alignment
assistant dialog box and click the Stopping sight
distance option.
-
Click Check.
The vehicle properties are initialized from the design rule customization file,
RoadAlignmentDesign.xml, and shared to the project team in Data Setup. You can check if the vehicle specifications (type, height, height of eye,
speed, ...) meet the stopping sight distance criteria.
The following values, defined in the design rule customization
file, are checked:
- The eye height of the driver: should be at a certain distance above the road
surface.
- The sight distance (50m is the minimum value)
- The vehicle speed: Due to high speed, the braking distance needs to be increased
on highways, especially in crests areas.
- If a speed has been set for the current reference key point, the check operation
will compare each vehicle speed with the key point speed and take the lowest value
as reference.
Stopping sight distance and headlight sight distance are linked together. If you
deselect the Stopping sight distance criterion, it will
automatically disable the Headlight sight distance option (the
command name and check box will be grayed out but the check state will remain the
same).
Headlight sight distance is linked to stopping sight distance because it is used only
in crest parabola length calculation in the stopping sight distance case. If an error
linked to headlight sight distance is detected, you will be notified with a stopping
sight distance error in crest.
Error messages are listed in the Message Reporting explaining
that the length of the curve does not meet the stopping distance criterion and longer
sight distances are needed.
-
Right-click an error and select the Fix error command to solve
it.
When stopping sight distance is not sufficient, a warning appears giving
instructions to solve the problem manually.
-
To allow brake reaction, improve the appearance of crest vertical curves by:
- Giving the crest required length to the vertical curves. When there are crests,
longer sight distances and longer vertical curves should be provided.
- Increasing the vertical curve radius.
- Reducing the design speed
Check the Passing Sight Distance
The passing sight distance is the distance ahead of the vehicle to pass safely a
slower vehicle. The passing sight distance is taken into account in the parabola creation.
You can measure the passing sight distance in crests, and adapt the design of vertical
alignment. Passing sight distances are linked to sight distances.
On two-lane roads, faster vehicles which overtake slower vehicles,
cross the centerline and use the opposite traffic lane. Drivers need to see the approaching
vehicles, to have a sufficient sight distance to start and finish their passing manoeuvre
without colliding with the opposing vehicle.
Critical distances must be respected: designers guarantee a given
passing sight distance on at least x% of the alignment length, for example: 25% of 500m.
-
To check the vertical alignment according to design rules, expand the
Criteria section in the Alignment
assistant dialog box and click the Passing sight
distance option.
-
To set a tolerance, select a value in Length of passing
sections and in Ratio of passing sections.
-
Click Check.
The following values, defined in the design rule script, are checked:
- Lane type: design vehicle
- The height of the object for passing sight distance: it can be edited in the
Profile specification.
- The eye height of the driver: should be at a certain distance above the road
surface.
- Length: The sight distance (50m is the minimum value)
In the 3D area, the
curve sections are colored red in the vertical alignment where a crest does not meet
the passing distance criterion. Error messages are also listed in the
Message Reporting explaining that:
- Longer sight distances are needed.
- The rate of the alignment on which sections respect passing sight distance.
- The gradient is out of limit.
- The ratio of the passing sections
-
Right-click an error and select the Fix error command to solve
it.
When passing sight distance is not sufficient, a warning appears giving instructions
to solve the problem manually.
-
To allow the safe passing of a slower vehicle, improve the appearance of crest
vertical curves by:
- Giving the crest required length to the vertical curves. When there are crests,
longer sight distances and longer vertical curves should be provided.
- Increasing the horizontal curve radius.
- Reducing the design speed.
-
Rework the crests and turns to achieve your goal or add passing lanes if
necessary.
Check the Headlight Sight Distance
At night, visibility is less than during the day and the vehicle's headlight illumination
is restricted in sag curves lead to minimum stopping sight distance. With sags, the
headlight beam intersects with the surface of the roadway which reduces the sight distance.
With crests, the headlight beam hits the tangency point of the roadway surface, creating
darkness at a short distance. Therefore, the height of the headlights and the length of
vertical curves must be considered.
-
To check the vertical alignment according to design rules, expand the
Criteria section in the Alignment
assistant dialog box and click the Headlight sight
distance option (not selected by default).
-
Click Check.
The following values, defined in the design rule script, are checked:
- Lane type: one way or two ways, design vehicle
- Vehicle type: The headlight height and the light beam divergence can be set on
each vehicle type.
- The eye height of the driver: should be at a certain distance above the road
surface.
- The sight distance (50m is the minimum value)
- Speed: Given the high velocity on highways (high-speed conditions), the
headlight sight distance must be higher.
- Stopping and passing sight distance: Headlight sight distance depends on these
two values. The length of vertical curves must be long enough to allow safe
stopping and passing distances.
Error messages are listed in the Message Reporting explaining
that longer sight distances are needed.
-
Right-click an error and select the Fix error command to solve
it.
When headlight sight distance is not sufficient, a warning appears giving
instructions to solve the problem manually.
-
When necessary, rework the sags to improve the headlight sight distance by:
- Giving the sag required length to the vertical curves. When there are sags,
longer sight distances and longer vertical curves should be provided.
- Increasing the horizontal curve radius.
- Reducing the design speed.
- Adding passing lanes.
Check the Drainage Control
To allow water drainage, road superelevation always has a normal slope at 2%. You
can run drainage controls on existing parabolas in vertical alignment and adapt the vertical
curves for drainage improvement on sags/crests and flatter grades.
On crests, it is recommended to ensure proper drainage near the hight
point of the vertical curves, for example: at a point about 15m from the crest/sag, a
minimum grade of 0.30% should be provided within 15m of the high point.
-
To check the vertical alignment according to design rules, expand the
Criteria section in the Alignment
assistant dialog box and click the Drainage control
option (not selected by default).
-
Click Check.
The following values, defined in the design rule script, are checked:
- Lane type: one way or two ways, width, slope. Given the high velocity on
highways (high-speed conditions), the drainage control must be higher.
- Grade: 15m on the left and on the right from the lowest point (sag) or the
highest point (crest) of the parabola.
Error messages are listed in the Message Reporting explaining
that the curve is too flat and a minimum rate of grade is required within a certain
distance of the level point.
The Fix error contextual command is not available for
Drainage control.
-
Right-click an error and select the command to solve it.
When drainage is not sufficient, a warning appears giving instructions to solve the
problem manually.
-
When necessary, modify the curve shape by:
- Changing grades (in or out): modify the tangent at the start and end of the
parabola.
- Changing parabola length manually.
Check the Passenger Comfort
Undulating grade lines may cause a passenger discomfort. If the sag vertical curves
have a short length, it has an effect on passenger comfort. These conditions must be
considered in vertical alignment. To improve the comfort of drivers, you can define the
comfort range, and provide checks for defining the geometry that will be the safety
zone. In sag vertical curves, the rate of change of grade may lead
to discomfort due to the gravitational and vertical centripetal forces.
-
To check the vertical alignment according to design rules, expand the
Criteria section in the Alignment
assistant dialog box and click the Passenger
comfort option (not selected by default).
-
To set a tolerance, select a value in Passenger comfort (in
m_s2) as the centripetal acceleration threshold.
The m_s2 value corresponds to distance in meter and the
vertical acceleration (s2). The higher the value is, the higher the slope can be. If you
decrease this value, the slope must be flatter.
-
Click Check.
The following values, defined in the design rule script, are checked:
- Lane type: one way or two ways, speed
- Vehicle type
- Speed: Given the high velocity on highways (high-speed conditions), the sag
vertical curves must be longer.
Error messages are listed in the Message Reporting explaining
that passenger comfort is not satisfactory in sag.
-
Right-click an error and select the Fix error command to solve
it.
When driver comfort is not achieved, a warning appears giving instructions to solve
the problem manually.
-
To satisfy the passenger comfort, rework the sags by:
- Giving the sag-required length to the vertical curves: decrease the gradient
design to obtain a smooth grade line with gradual changes, being consistent with the
type of road.
- Increasing the horizontal curve radius.
- Reducing the design speed.
|