AGG_1 (1)
|
Aggregation
|
Aggregated
object
does not know its aggregating object
|
Aggregated object does not know its
aggregating object
|
Deletes aggregation
|
None
|
AGG_2 (2)
|
Aggregation
|
Undeletable view, Copy Paste failure, etc.
|
Corruption of an aggregation link between
two objects (reciprocity broken). An aggregated object does not know its
aggregating object
|
Updates aggregation link
|
The view is removed,
works, etc.
Data needs to be updated
|
AIR_2 (2) |
Assembly |
Incorrect thread analysis. Unable to distinguish
edges to fillets coming from assembly impacts. |
Inner data structures (bridge) are erroneously
duplicated during the application of a move constraint to a
representation. |
Keeps only the correct data structure, and removes
the incorrect ones. |
The representation is no longer synchronized in the product
structure. You need to update the root (whole product data
structure) to synchronize repaired links. You also need to
update documents. |
BOL_0 (2)
|
Part Design
|
Visualization problems due to Boolean
between Solid body (old) and hybrid body (new)
|
Boolean operation between solid body (old)
and hybrid body (new)
|
Moves operand body under the part
|
Tree
changes because operand body has been moved from Boolean to part
|
BOL_1 (2)
|
Part Design
|
Visualization problems due to Boolean
between two hybrid (new) bodies
|
Boolean operation between two hybrid (new)
bodies with operand body not aggregated to the Boolean feature, however
displayed under it, leads to visualization problems
|
Moves operand body under the part
|
Tree changes because operand body has been
moved from Boolean to part
|
BOL_2 (2)
|
Part Design
|
Solid body containing a Boolean feature is
not processed when Part to Part data filtering is done. Then, the geometry
associated to the Boolean feature is not visible in the 3D area
|
Scope of the Boolean feature is missing
because the geometry of the Boolean feature is not seen in the 3D area
|
Deactivates then re-activates the Boolean
feature. This creates the scope of the Boolean feature
|
Geometry associated to the Boolean feature
is visible in the 3D area.
Document needs to be updated
|
BOL_4 (2) |
Part Design |
A color cannot be applied to the whole tool if it
contains boolean trim operation |
Even if the trim feature has the correct
configuration level to apply the new color algorithm, this algorithm
is not applied on the trim feature. This is due to a wrong
initialization of the color mode attribute. |
If the trim feature has the correct configuration
level, the color mode attribute is correctly set. |
After the clean operation, users need to apply the
same color to the whole tool. |
BST_1 (3)
|
Mechanical Modeler
|
External user cannot see CAA features
created with a previous version
|
When startup catalog for CAA features is
not present, features cannot be displayed
|
Declares object's backup startup class
|
External user can see CAA features
|
CAT_0 (2)
|
Specs Modeler
|
A core dump may occur when accessing some
data
|
A Catalog Manager does not point to a
catalog document
|
Removes the link to the document that is
not a catalog
|
No more core dump when accessing data
|
CIV_0 (1) |
Civil Engineering |
Issues during Cut-Copy-Paste or Delete
operations |
An element of type 'Alignment2DVertical', "CbaNewPatternSupport", or
"CbaNewPatternDeck" is not aggregated and not used by any
element. |
Removes the orphan feature. |
The Cut-Copy-Paste or Delete operations are
successfully applied. |
CPF_0 (3)
|
Part Design
|
Size of a part is abnormally huge
comparatively to the number of elements
|
Unreferenced BREP features in Part Design
features
|
Deletes unreferenced BREP features
|
Model size is reduced
|
CPF_1 (3)
|
Part Design
|
After a semantic painter operation, some
faces of the feature are transparent
|
The opacity of these faces is not restored
to its original value after the semantic painter operation. The opacity is set
to 30, making these faces transparent.
|
Sets the faces opacity to 255 to correct
transparency issues
|
The faces are no longer transparent
|
CRV_0 (2)
|
Sketcher Modeler
|
Curves created outside the
Sketcher workbench with no endpoints
|
Resulting geometry associated to the sketch
is not consistent
|
Adds required endpoints
|
Sketches are seen as not up-to-date.
Document needs to be updated
|
CRV_1 (3)
|
Sketcher Modeler
|
Update result is wrong because the update
propagation is wrong. Some features are not impacted by geometries
modifications, e.g. Output features
|
Attributes of several features are set to
sp_NEUTRAL instead of sp_IN
|
Sets quality of curves attributes to sp_IN
|
No impact, except when cleaned geometries
are published by outputs features.
Representation
needs to be updated
|
CST_2 (2)
|
Sketcher Modeler
|
CPU loop or problem with the activation/
deactivation of a constraint
|
Bad quality of constraints attribute
|
Changes quality of attribute
|
Representation needs to be updated.
Constraint can be used again
|
CST_3 (1)
|
Sketcher Modeler
|
Some
Sketcher constraints are wrongly
displayed or ignored during update
|
Value of a constraint attribute is lost
|
Deletes constraint
|
Representation needs to be updated.
The constraint can be used again
|
DAC_4 (2)
|
Drafting Annotation
|
A Roughness symbol is reversed when
changing the standard through
Page Setup. Roughness has an orientation
link on the extension line (with interruption) of a dimension.
|
The orientation link on the extension line
of a dimension with interruption could not be correctly built in previous
releases before V5R14. In this case, the orientation link can return a wrong
orientation direction. Thus, the roughness orientation on dimension is wrong.
|
Restores a correct orientation link
|
Roughness symbol is reversed and a possibly
missing extension line is created
|
DAF_0 (3)
|
Drafting Annotation
|
The area fill is an empty space
|
The area fill not associated to any
geometrical elements
|
Deletes the area fill
|
The area fill has disappeared
|
DAF_1 (3)
|
Drafting Annotation
|
The area fill cannot be selected
|
The area fill is not aggregated
|
Deletes the area fill
|
The area fill has disappeared
|
DAF_3 (3)
|
Drafting Annotation
|
Drawing
contains some Area Fills that the user cannot see (only by using the Search
function)
|
Area Fill without pattern
|
Deletes the area fill
|
The area fill has disappeared
|
DAO_2 (2)
|
Drafting Feature
|
Extension line is not visible (or not
correctly) when creating extension line for roughness
|
View scale was badly taken into account for
associative position on dimensions extension line (overrun). Extension line for
roughness creation was not using the good length of dimension extension line
(overrun)
|
View scale is taken into account for
associative position dimensions extension line (overrun)
|
Extension line for roughness is now
correctly visible
|
DCT_2 (1)
|
Drafting
|
No visibility
|
Some features in CATDrwCont should have a
father but are actually not aggregated anywhere: these corrupted/useless
features are not visualized but can have links to external documents
|
Deletes non-aggregated feature
|
No impact. Representation size is reduced.
|
DCT_4 (3)
|
Drafting
|
Error panel when opening the representation
saying that a used font is not available, although this font is not used by any
annotation
|
A DrwMappingTable feature keeps a
reference
to a no more used font
|
Reference to the font is removed from the
representation
|
No more error panel when opening the
representation
|
DCT_5 (2)
|
Drafting Annotation
|
Impossible to use new fonts on dimensions
inside the document
|
Internal font list is full
|
Removes unused fonts from the list and adds
space in the list if needed
|
New fonts can be used and existing
annotation now use the right font
|
DCT_6 (1)
|
Drafting Annotation
|
V6 to V5 specs checker has annotations
specific errors.
|
Unused FTA specific drafting features. FTA
data is removed but the FTA specific drafting features are not removed.
|
Removes unused FTA specific drafting
features if they are not being pointed by any other user feature.
|
V6 to V5 as Spec checker will not have any
annotation specific errors. V6 to V5 as Spec migration should be possible.
|
DDI_4 (2)
|
Drafting
|
Dimension attribute is not valuated
|
Dimension display does not match dimension
properties
|
Updates dimension properties
|
Dimension value does not go any more on the
dimension line after view update
|
DDI_11 (2)
|
Drafting
|
Dimension text does not use the right font
|
Link from font and dimension visualization
has been lost through undo/redo operation
|
Dimension visualization is rebuilt
|
Correct fonts are used for dimension
visualization
|
DDI_16 (2)
|
Drafting
|
Dimension may usethe wrong format for the
tolerance display
|
The dimension visualization does not use
the format specified by the model
|
The dimension visualization is updated to
use the right tolerance format
|
The dimension tolerance is displayed with
the right format
|
DDI_17 (2)
|
Drafting
|
Dimension may not display it before, after,
upper and/or lower texts
|
The dimension before, after, upper and/or
lower texts are not displayed as specified by the model
|
The dimension visualization is updated to
display the before, after, upper and/or lower texts
|
The dimension before, after, upper and/or
lower texts are correctly displayed
|
DDI_18 (2) |
Drafting |
Fake dimension may not correctly display the
alphanumerical fake value. The decimal part is missing. |
The fake dimension value is not displayed as
specified by the model. |
The dimension vizualization is updated in order to
correctly display the value. |
The alphanumerical fake value of the dimension is
correctly displayed. |
DDU_2 (1)
|
Drafting
|
Unexpected link on a Drawing document leads to the detection of the
problem. |
Feature (which leads to the invalid link) is set under DrwCont instead
of being aggregated under a view. |
Deletes axis lines, center lines, or thread that are directly under
DrwCont container. |
No more unexpected links when running the File >
SendTo command. |
DET_10 (1) |
Drafting |
The New Drawing command
generates an extra text. |
When opening a 2D Component Reference in a
2DLayout, objetcs are aggregated in a wrong way and cannot be
correctly managed. |
Deletes objects that are aggregated in a wrong
way. |
All the aggregated objects of a cleaned 2D
Component Reference are correctly aggregated. |
DFM_0 (2)
|
Drafting
|
When opening a representation which was created with a previous version,
the format of some sheets are flipped. |
DrwFormats whose width should not be
strictly greater than height. Indeed, in representations with CATIA V5 embedded
standard, every DrwFormat's characteristics should be width >= height.
DrwFormats that can be cleaned must match the following criteria (otherwise
they are ignored):
- They are aggregated by a Sheet (DrwFormats in the Drawing
list are ignored)
- They are in a representation with a CATIA V5 embedded
standard.
|
Cleaning such corrupted DrwFormats involves
the following operations:
- Retrieve width, height and orientation stored on
DrwFormat
- According to the retrieved data, compute and set new
values for those attributes
|
Corrupted formats of the sheet are flipped
back to normal
|
DRF_0 (3)
|
Part Design
|
When deleting the draft, some related data
are left in the representation
|
Data model inconsistency
|
Removes User Features from Geometrical Set
to PartBody under Draft feature
|
Data model inconsistency is now solved for
this draft feature. If deleting the draft the life cycle management will be
better.
Representation needs to be updated
|
DRF_1 (3)
|
Part Design
|
When creating a new draft feature, the
geometry selected to define the pulling direction is inconsistent with the
pulling direction vector
|
Inconsistency between the vector and the
selected object in the definition of default values
|
Resets default pulling direction in object
and vector
|
Default draft pulling direction is changed.
The next created draft will use this new default pulling direction
|
DTA_1 (2)
|
Drafting Annotation
|
Tables in instantiated 2D components do not
keep their orientation. The table gets instantiated, but the orientation
remains horizontal.
|
The orientation of the table is not taken
into account while the visualization is done.
|
The visualization takes into account the
orientation of the table.
|
All instantiated tables move to the correct
orientation.
|
DTA_2 (2)
|
Drafting Annotation
|
When opening a pre-CATIAV5R15 CATDrawing on
any CATIA level other than the drawing creation level, the width of the table
is larger.
|
The left margin of pre-CATIAV5R15 tables
may not be correctly managed.
|
Restores the valid value of the margin.
|
The table is correctly displayed.
|
DTA_3 (2) |
Drafting Annotation |
When opening a CATIAV5R25 CATDrawing imported
within 3DEXPERIENCE, if a table has an associative position link on
another table, then the position link may be unstable. |
The model information of associative position and the display of the
position table are not synchronized. An update may change the
position of the secondary table. |
Restores the correct information to avoid a change
of position while an update is done. |
The table is correctly visualized. |
DTE_2 (2)
|
Drafting
|
1. Text with position link to another text
is not up-to-date after canceling text edition of reference
2. Text leader with Positional Link with a 2D Line is
pointed to other element
|
1. Associative position with text as
reference was not updated after canceling text edition
2. Text leader with Positional Link with a 2D Line was not
updated
|
Updates position link to get the correct
position
|
Position of text or leader is moved to the
right location
|
DVM_0 (2)
|
Drafting
|
Error when saving a Drawing
|
Useless view makeup detected
|
Deletes useless view makeup
|
Drawing is correctly saved. Reduces the
size of the representation
|
DWR_0 (3)
|
Drafting
|
No visibility
|
Useless relation has been detected: either
the in or the out of the relation is not valuated
|
Deletes useless DrwRelation
|
Representation size is reduced
|
DWS_0 (2)
|
Drafting
|
Impossible to select a view (not allowed),
Grid disappears, or impossible to activate
Drafting workbench
|
Internal value which determines the order
of the views is not correctly set
|
Internal value correctly set: the order of
the views is correct
|
View can be selected
|
DWS_1 (1)
|
Drafting
|
No visibility
|
Corrupted sheet has been detected: either
it has not the minimum required views (background and main view), or it is not
under the drawing
|
Deletes corrupted sheet
|
No impact. Representation size is reduced
|
DWV_0 (1)
|
Drafting
|
No visibility
|
One or several rules for a view in the
drawing is not respected:
1. A view must have a parent
2. A view of type Pure_sketch must not have a sheet as its
parent
3. A view which is not of type Pure_sketch must have a sheet
as its parent
|
Deletes view
|
Drawing is correctly saved. Representation
size is reduced
|
DWV_4 (3)
|
Drafting
|
Axis elements of the sketch support
associated with a view that has been put in the No Show space before V5R14
cannot be visualized in the Show space anymore
|
Sketch support is in the No Show space
|
Puts sketch support in Show Space and puts
its axis elements in No Show space
|
Sketch support axis elements can be seen in
the Show space (provided that the user puts them in it)
|
DWV_5 (1) |
Drafting |
Corrupted links appear in the Edit Links and
Relation command for drawings. |
A useless link exists on the view to an external
document. |
Removes the invalid link. |
Corrupted links do not appear anymore in the Edit
Links and Relation command. |
DWV_6 (3)
|
Drafting
|
File size for Drawing or Part containing
some 2DLayoutData is too big
|
Update mechanism has lead to the creation
of the Geometrical result of Drafting/2DLayout Views and 2D
Component
references.
|
Useless geometrical results are removed
from CGM container data. This data can represent MB of file size
|
Representation size is reduced
|
DWV_8
|
Drafting
|
Section Views have got renamed to Front
View with earlier Defined Front View seen as isolated.
|
Certain Auxiliary or Section Views might
have lost the Projection/Section Operator Spec information completely.
|
There is no way for the user to clean such
Views (Auxiliary / Section Views) and recover the lost Operator Spec
information. End User would need to re-create these Auxiliary / Section Views
again using NON-Isolated Front View.
|
Non fixable
|
FGM_1 (3)
|
Geometric Modeler
|
The size of the part is not minimal.
|
Presence of some unnecessary geometric
objects or unnecessarily extrapolated surfaces
Note:
This error may appear or disappear after any operation
(including but not limited to: feature creation, modification or deletion,
update, save/open). It does not indicate a defective, failed or incomplete
operation.
|
Removes the unnecessary geometric objects
and de-extrapolate surfaces when possible
Note:
If the de-extrapolated surfaces are extrapolated again
their new shape may differ from the previous one.
|
The part is the same but with a smaller
size
|
FIL_0 (2)
|
Part Design
|
During edition of fillet an error "Internal
error in mechanical modeler" is displayed
|
Support of some PointOnEdges (used to
define radius for variable fillet) belongs to a ribbon other than the one to
which the PointOnEdge itself belongs. Hence, when the support edge is removed
(de-selection from user Interface), the corresponding PointOnEdge is not
removed. This PointOnEdge then remains without support and gives an error
"Internal error in mechanical modeler" when we try to access its support
|
Moves the PointOnEdge (FilletRadius object
containing it) to the appropriate ribbon
|
Some objects (the fillet concerned and its
impacted features) are seen non-updated.
Representation needs to be updated
|
FIL_1 (2)
|
Part Design
|
If you open an EdgeFillet definition and
select objects to fillet edges one by one, some of them represent the same edge
in 3D
|
The objects to fillet were not set properly
on an previous level, and have the same domain (Cells)
|
Keeps only one of the edges and removes the
other objects to fillet
|
Document needs to be updated
|
FMP_4 (2)
|
Part Design
|
Functional feature using a "to-shell"
length does not correct the shell
|
Wrong shape is referenced by the feature
|
Changes reference to the correct shape
|
Part is red (not up-to-date).
Representation needs to be updated
|
FMP_5 (2)
|
Part Design
|
Feature does not update
|
"Ignore update" flag is incorrectly set
|
Clears the "Ignore update" flag
|
Part is red (not up-to-date).
Representation needs to be updated
|
FMP_6 (2)
|
Part Design
|
Functional feature using body thickness for
its wall value does not update when body thickness is changed
|
Incorrect parameter is referenced by the
feature
|
Changes reference is to the correct
parameter
|
Part is red (not up to date).
Representation needs to be updated
|
FMP_7 (2)
|
Part Design
|
"Shellable" feature does not change "wall"
direction when the part's shell properties wall direction (inward/outward) are
changed
|
Incorrect parameter is referenced by the
feature
|
Changes reference is to the correct
parameter
|
Part is red (not up to date).
Representation needs to be updated
|
FMP_8 (2)
|
Part Design
|
Functional modifier is trying to modify the
features of another part
|
Modifiers target list contains the features
of another part
|
Removes the targets of the list that are
not in the same functional body
|
Part is red (not up to date).
Representation needs to be updated
|
FMP_9 (2)
|
Functional Modeling Part
|
Unable to update part using force update
and part is corrupt
|
Shell property feature which is mandatory
for wall based features is missing
|
Creates missing shell property feature with
zero wall thickness
|
Shell property feature is created in the
part. On update, part gets updated and build is OK
|
FMP_11 (2)
|
Functional Modeling Part
|
Deleting a Solid Functional Set or a FMP
feature impacts wrongly FMP features from other Functional Sets.
Parent/Children shows abnormal relationships between FMP features from
different functional sets.
|
Some useless B-reps pointing onto other
functional sets were aggregated by the FMP feature being directly or indirectly
deleted or by the FMP feature being analyzed through Parent/Children analysis.
|
Deletes useless B-reps features.
|
Solid Functional Set needs to be updated.
The parent/Children analysis does not show anymore abnormal links.
|
FMP_12 (2) |
Functional Modeling Part |
Technological results coming from assembly impacts
done with Assembly Features with protected bodies are missing. It
results in some missing thread/tap display, which you can also
notice by doing a Thread/Tap analysis. |
There are naming issues on protected bodies. These
naming issues have already been fixed. Parts & features created
before this previous fix need to be fixed by this clean
action. |
Upgrades the protected bodies (specifications of
Assembly Features) and the impacts. |
Protected bodies (specifications of Assembly Features) need to be
updated. Parts including the impacts of these Assembly Features
need to be updated too.
Documents need to be updated.
|
FTA_12 (3) |
Functional Tolerance Annotation |
No 3D annotation view found for a 3D
annotation |
The link between FTA 3D annotation and FTA view
was lost, even if the Drafting view, which is considered as FTA View
support, is kept. |
Creates a new FTA view and reroot it on FTA 3D
annotation and on the associated Drafting view. |
A new FTA view appears in 2D graph. The query from
FTA 3D annotation to FTA view is possible with the context
menu. |
FTA_19 (3)
|
Functional Tolerance Annotation
|
Inconsistent Repetitive Feature Identifier
|
Either the repetitive feature identifier
does not correspond to the number of pattern elements the dimension is linked
with, or there is none or several repetitive feature identifiers, or there is
no space ("") character between the repetitive feature identifier and the text
placed before or after it.
|
Changes the Inconsistent Repetitive Feature
Identifier.
|
The Repetitive Feature Identifier becomes
consistent.
|
GNC_1 (1) |
Part Design |
When using Copy-Paste on a body into a 3D shape,
the operation fails and an error pops up |
The naming of the feature inside the body is
incorrect. |
No fix available by default. |
A message indicating how to fix the error manually
is provided to the user. |
GSD_0 (3)
|
Generative Shape Design
|
Sometimes the user can only see invalid
"Parent/Children" or impact analyses
|
An object is aggregated under "Component"
attribute but it is never used elsewhere
|
Suppresses useless object
|
Visually no impact, better
"Parent/Children" or impact analyses, reduces the size of the Representation
|
GSD_1 (1)
|
Generative Shape Design
|
Reference planes have datum mask on their
icon and must have been moved with the compass
|
Reference planes are turned into datum or
flagged as contextual features
|
Resets datum and\or contextual flags to 0.
If a reference plane has been moved, a new one is created and added at the
place of the moved reference plane. The moved reference place is renamed with
the "moved by cleaner" to its alias
|
Icon of the reference plane has not the
datum mask any more. A reference plane is removed and a new reference plane is
created
|
GSD_2 (2)
|
Generative Shape Design
|
When updating a part containing axis
systems created before CATIA V5R12SP2, orientation is inverted for some of them
|
Axis system algorithm was modified without
versioning. When updating the axis system, which was built using old algorithm,
its orientation might change since it now uses the new algorithm
|
Axis system attribute has been modified so
that it maintains the same orientation with new algorithm
|
Update the axis system. Axis system
orientation is not inverted. Axis System and dependent features seen not
up-to-date.
Representation needs to be updated
|
GSD_7 (2)
|
Generative Shape Design
|
Opening a CATPart in Catia V5 fails due to
an invalid link
|
CATParts contain features that have their
references in external documents. When opening a CATPart in Catia V5, their
startup is not known.
|
Re-plugs the reference to the startup
|
The CATPart can be opened.
|
HIE_8 (2)
|
Specs Modeler
|
None in V5, as other links are expected
between the two documents so
,
,
behave as expected
|
Some links are created as external links
during the creation of a local reference, links that should be within the local
reference's structure
|
Offending links are re-routed within the
local reference's structure (internal links)
|
None in V5.
Representation needs to be updated
|
HLV_1 (1) |
Generative Drafting |
The drawing document size can be out of
proportion regarding the useful data contained inside. Unrelated
document can be pointed by the drawing document ( appears using Send
To). |
A generative view is not aggregated. |
The non-aggregated generative view is
deleted. |
The drawing document size is normal again. No more invalid links in
Send To command. |
HOL_0 (1)
|
Part Design
|
Hole's Activity parameter does not work
correctly
|
In CATIA V5R17 for the Hole feature, there
are 3 Activity parameters visible to the user among which 1 is valid and 2 are
invalid. If the rule is set on invalid Activity parameter, such rule would not
work
|
Rule set on the invalid activity parameter
of the Hole is copied and set on the valid Activity parameter. The rule set on
invalid Activity parameter is then deleted
|
A new rule would be seen under the Relation
Set which would be same as the old rule. Update would be required on the data
after which the rule would correctly work.
Representation needs to be updated
|
IGS_0 (3)
|
Sketcher
|
Use edges created when constraints are
created, then when deleting these constraints, use edges that are not deleted
and are therefore unnecessary (severity 3 since CATIA V5R9SP3)
|
Use edges that are not deleted when
associated constraints are deleted. Unused elements (phantom operators) stay in
the representation
|
Deletes unused elements
|
Representation needs to be updated.
Representation is the same but smaller
|
IGP_1 (1)
|
Robotics
|
When cleaning any mechanism that has a
constraint created by FramesOfReference in Device Building, the constraint is
also deleted
|
TagConnectors created on the constraint
definition are not aggregated to any parent. When cleaning the document, the
LIF_8 rule deletes all the floating connectors, so the TagConnector is deleted.
Therefore, the Parts associated with the constraint are disconnected.
|
Aggregates the floating TagConnector with
the TagGroup, its logical parent
|
TagConnectors are no longer deleted when
cleaning the document
|
IGP_2 (2)
|
Robotics
|
The
File/Send To Directory command shows
references to not-found files if the document contains joint targets in robot
tasks
|
The robot task copied and pasted across the
documents has invalid links when there are joint targets with auxiliary devices
|
JointTarget objects are considered invalid
if any of their attributes is pointing to objects in a different document
|
The
File/Send To Directory command no longer
leads to invalid links due to joint targets
|
IGP_3 (1)
|
Robotics
|
The TagList node under the Product node is
not valid. For some reason, content with the TagList node is present under the
Product node.
|
When a user copies and pastes a TagList,
only the TagGroups under it are pasted. The TagList itself cannot be pasted. In
some cases (CXR23SP5 copy-paste), the TagList node (and the TagGroup under it)
is pasted directly under the Product Node:
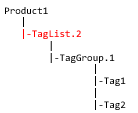
|
Removes any TagList present directly under
the Product node. The TagGroup node is re-parented to the Product node.
|
The valid structure is displayed:
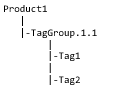
|
IGP_4 (1)
|
Robotics
|
The
SendTo command fails and displays the
following message: "At least one file is not saved on a file system (probably
loaded from a database)"
|
The content has an additional robot task
that is not visible in the user interface. All modifications are impacting the
visible robot task and not the additonal one. The additional robot task makes
some operations impossible, like SendTo.
|
Removes the additional robot task that is
not visible
|
The SendTo operation is successful
|
IGP_5 (1)
|
Robotics
|
After a CCP on the activity from the
original process to a new process with resources, the original document is seen
in Save Management for copied documents editor scope. File/SentTo can detect an
invalid link.
|
After a CCP is done on an activity from one
process document to another process document along with resources and items,
invalid links are found in the Device Plug pointing to the original process
document. Due to this, the original document could be modified when saving
copied documents.
|
Finds and deletes the Device Plug that
contains the invalid link
|
The invalid Device Plug with invalid links
is removed
|
IGP_6 (1)
|
Robotics
|
Creating a swept volume fails and the
following error message is displayed: "Swept volume could not be created"
|
The Part bodies under TagGroups are
logically incorrect. Such content does prevents the creation of swept volumes.
The children of TagGroups are checked and the invalid Parts are removed.
|
Finds and deletes the invalid Parts under
the TagGroups
|
Invalid Part under TagGroups are removed,
and the error message no longer appears when creating a swept volume
|
KWE_1 (1)
|
Knowledge
|
No visible symptom
|
Knowledge objects are not aggregated
|
If these objects are not pointed, they are
removed. If it is a parameter that is pointed, it is added to the parameter
set. If it is a relation that is pointed, it is added to the relation set
|
No visibility
|
KWE_11 (1)
|
Knowledge
|
In Enterprise Knowledge Language (EKL), the
function Distance (body, body) may return an inaccurate result depending on the
order of the arguments within formulas.
|
Internal distance computation operator
error. This will be fixed later, but is versioned so the usage of the Upgrade
command is required.
|
Runs the upgrade mechanism to ensure the
formula uses the last version of the distance operator.
|
The function Distance (body, body) returns
an accurate result. The document needs to be updated.
|
KWE_12 (3) |
Knowledge |
It is not possible to delete a parameter into a
body. A Material parameter has been detected. |
A useless Material parameter has been imported to
3DEXPERIENCE. |
Deletes the Material parameter. |
The Material parameter is removed. The document
needs to be updated. |
LSC_1 (1)
|
Drafting
|
An error panel appears, showing the presence of a invalid link |
A invalid link is created during the ccp process by the 2DL section,
that points to a 2DL filter of an external |
Unsets the link between the 2DL section and
the 2DL filter.
|
The error panel does not appear anymore
|
LIF_1 (1)
|
Mechanical Modeler
|
Size of part too big compared to the number
of elements or, some mechanical features are absent from the tree although
detected in some commands
|
Unused elements (geometrical feature) are
present or used elements should appear in the tree
|
Deletes unused elements. Some used elements
(such as GSD features, geometrical sets and part bodies) are regenerated
properly under the part in the tree
|
Part is the same but smaller. Used GSD
features, geometrical sets and part bodies are all visible in the tree
|
LIF_3 (3)
|
Mechanical Modeler
|
No visibility except the size of the
representation (constraints deletion cases)
|
Unused elements (mechanical constraints)
are present
|
Deletes unused elements
|
Representation is the same but smaller
|
LIF_5 (3)
|
Mechanical Modeler
|
Invalid link in
selection
set
|
After deletion of some elements in part or
product,
links are kept in selection set
|
Deletes unused elements
|
No more invalid links
|
LPR_1 (1)
|
Drafting
|
When deleting a specific profile, other
Profile2DL objects are impacted, and seen as not up-to-date. If automatic
update is selected in
,
the update error panel is triggered with the error "Unable to evaluate the
profile. No profile definition found in the layout view"
|
An internal structure definition for
Profile2DL is shared by many Profile2DL objects, instead of being unique for
one Profile2DL. When a Profile2DL is deleted, it deletes its internal
definition, and deletes it for all Profile2DLs sharing this definition. The
remaining Profile2DLs cannot access their internal structure, and cannot be
rebuilt afterwards
|
Two corrections exist depending on the
geometrical result of the Profile2DL:
- if the Profile2DL has a geometrical result, the profile
is isolated. The profile can be used as a datum geometry.
- if the Profile2DL does not have a geometrical result, the
profile is destroyed, as nothing can be done with it: it cannot re-build its
geometrical result because it does not have any more definition specifications
|
All profiles that shared the same internal
structure definition are either isolated or deleted. All children of these
profiles are impacted.
- If a profile is isolated, children objects are not
up-to-date.
- If a profile is deleted, children objects can have an
update error.
Representation needs to be updated
|
MFG_0 (1)
|
Manufacturing
|
No visibility except abnormal size of
Representation
|
Unused machining feature is not deleted
(activities cases)
|
Deletes unused machining feature
|
Representation is the same but smaller
|
MFG_1 (1)
|
Manufacturing
|
No visibility except abnormal size of
Representation
|
Unused pattern definition is not deleted
(pattern cases)
|
Deletes unused pattern definition
|
Representation is the same but smaller
|
MFG_3 (1)
|
Manufacturing
|
No visibility except abnormal size of
Representation
|
Toolpath not referenced by an activity is
not deleted
|
Deletes the unused toolpath
|
Representation is the same but smaller
|
MFT_1 (1)
|
Mechanical Modeler
|
When a solid is deactivated, the previous
solid's result is damaged
|
Inactive feature storing the result of the
previous feature
|
Reconstruction of the internal result when
possible
|
Representation needs to be updated
|
MGN_6 (1)
|
Mechanical Modeler
|
Size of a part on disk is too big
|
Useless Mechanical modeler data
|
Removes useless data
|
Representation size is reduced
|
MGN_7 (2)
|
Mechanical Modeler
|
Some cells of Datum feature cannot be
selected. Copy/Paste operation aborts
|
Cells cannot be selected because they have
no naming
|
Adds a naming to the cells
|
All cells can be selected, and other
features may be applied.
Document needs to be updated
|
MGN_9 (1)
|
Mechanical Modeler
|
Some existing cleaning rules (LIF_1) are
too generic and delete data, and there is no easy way to repair them
|
Problem should occur only when the user
creates publication in the part on non aggregated BRep features by using a
batch. If geometry is changed, publications are not put to non updated status
and features using them are not updated
|
Deletes invalid BRep features and re-plug
the publication on equivalent BrepAccess. In some particular case, error may be
returned as 'Non fixable'. Then a detailed comment explain to end user how to
clean manually its data
|
Existing cleaning rules LIF_1 will no
longer appear in these cases, publications will be pointing correct geometry,
and update/no update status will work correctly
|
MGN_12 (3)
|
Mechanical Modeler
|
Size of the document is too big
|
Some Brep features pointing geometry with
big history even if correct are really big
|
Compresses these Brep features to minimize
the size
|
Brep feature and part need to be updated.
Representation needs to be updated
|
MGN_13 (2) |
Mechanical Modeler
|
Some Brep features are in error
|
Some Brep features are in error because
they have lost some specifications
|
Tries to retrieve the lost specifications
|
Less Brep features in error.
Representation needs to be updated
|
MGN_22 (2) |
Mechanical Modeler |
Sub-geometrical elements of the feature are not
selectionable. |
Some data was lost during a copy-paste
operation. |
Arbitrarily sets new data. This may lead to
unusual selection behaviors, as the data is regenerated from
scratch. |
Selecting sub-geometrical elements is
possible. |
MGN_23 (2) |
Mechanical Modeler |
Sub-geometrical elements of the feature are not
selectionable. |
Some data was lost during a copy-paste
operation. |
When errors are detected, users are informed that
they can manually modify the data (break a link) to make the rule
fixable. |
Non fixable error. |
MGN_24 (2) |
Mechanical Modeler |
Dynamic B-Rep links (used by FTA annotations, for
example) might be broken after an isolate or an upgrade
operation. |
Dynamic B-Rep links do not contain the required
data to be automatically rerouted. |
The data required to reroute the links is
recomputed within the dynamic B-Rep links. These links nee to be
updated afterward. |
Dynamic B-Rep links are no longer broken after an
isolate or upgrade operation. |
MIR_0 (2)
|
Part Design
|
When updating a corrupted mirror feature,
an error with message " One or several features of the list have been deleted.
Data is no longer consistent. You must delete the transformation feature." is
displayed
|
One or many reference elements kept in
Generative Tool for mirroring are lost
|
Reference elements kept in Generative Tool
are created again
|
Representation needs to be updated
|
MMR_0 (1)
|
Mechanical Modeler
|
Severe global malfunctions in the part
|
At least one of the part's reference planes
(xy, yz, zx) is damaged or missing
|
Part's reference planes (xy, yz, zx) are
regenerated or repaired
|
Representation needs to be updated
|
MMR_2 (2) |
Mechanical Modeler |
Several global malfunctions in many operations
that require a main body |
There is no main body (PartBody) in the
part |
Creates a main body |
The main body is created |
MMR_7 (2)
|
Mechanical Modeler
|
After FBDI, some External References
without context can have an update status that does not reflect the correct
status of the feature
|
The features that depend on these External
References cannot retrieve correct information about them
|
The impacted External References without
context and the features that depend on them are set to Not UpToDate
|
Document needs to be updated
|
MMR_11(2)
|
Mechanical Modeler
|
Some links under constaints or
publications, that rely on at least one specific feature, cannot be resolved
either at creation or after reopen.
|
There is at least one persistent unique
identifier associated to many features. Links that rely on those features are
persisted using these identifiers. There is an ambiguity when trying to resolve
those links we cannot find the correct feature from the persistent identifier.
|
Replaces duplicated persistent identifiers by new ones. |
Broken links, relying on duplicated
feature's persistent unique identifier, created before the clean, will still be
broken. They have to be manualy removed or replaced. New links will be ok.
|
MMR_13 (2) |
Mechanical Modeler |
The model update fails, and the following error
message appears in the Update Diagnosis window: "Mix of polyhedral
and exact inputs are not allowed for this operator. Convert exact
inputs into polyhedral data to perform the operation." |
One or several links required for the automatic
tesselation to work correctly are missing. |
Restores the missing links required for the
automatic tesselation. |
The model can be updated correctly. The document
needs to be updated. |
MMR_14 (3) |
Mechanical Modeler |
During the update of a generic feature, its
generic feature set is not updated. Therefore, the features that are
using those sets are not updated either. |
In the generic feature set definition, there is no
attribute sp_IN that makes the feature out of date. Therefore, this
feature is never seen as updatable, and is never updated. |
Declares the _FtrList attribute of the generic
feature set catalog as sp_IN, and automatically updates all the
generic feature sets when their children are updated. This clean
rule is used to change the quality of the attributes for old parts. |
After the update, the generic feature set is
updated. |
MMV_1 (3)
|
Mechanical Modeler
|
Visualization of a part is black
|
Invalid graphic property on the part
|
Deletes invalid property
|
Part is correctly visualized
|
MMV_2 (3)
|
Mechanical Modeler
|
Visualization of previously dressed-up
geometry (used in
Free Style workbench) can be wrong: the
dress-up can still be visualized after removal. This problem can only occur for
documents created before CATIA V5R10
|
In some cases, dress-up properties could be
duplicated, so that one property remained even after removal
|
Restores correct dress-up properties
|
Correct visualization, corresponding to the
dress-up properties
|
MMV_3 (3)
|
Mechanical Modeler
|
If multi-viewer infrastructure is available
on the part body (e.g. in
SheetMetal workbenches), wrong view names
appear in
Views and
Add view dialog boxes of the contextual
menu. These view names appear in addition to the correct ones (i.e.
3D View and
Flat View)
|
This problem can only happen for Part
documents created in CATIA V5R10. On that level, wrong attribute values were
streamed on the part body
|
Deletes wrong attribute names
|
Both multi-viewer windows contain only the
correct view names
|
MTR_0 (2)
|
Mechanical Modeler
|
Generated drafting view is not complete:
some elements are missing compared with the 3D visualization of the part
|
Wrong plug of attribute from the mechanical
body to its last solid
|
Correctly resets attribute
|
Representation needs to be updated
|
MTR_2 (2)
|
Mechanical Modeler
|
Visualization and/or update errors among
solids
|
Wrong plug between solids
|
Correctly re-plugs solids
|
Representation needs to be updated
|
OLE_0 (2)
|
Drafting
|
No visibility
|
DrwOLE object points to a startup not
located in the same CATDrawing
|
OLE startup will be imported into the same
drawing as the DrwOLE object if necessary. The DrwOLE object will then point to
the right OLE startup
|
No visibility
|
PAT_0 (1)
|
Part Design
|
Representation cannot be updated. Error
obtained when update is called on part having user pattern, which has redundant
instances in its Generic Tool
|
If user pattern has user defined feature as
one of its item to pattern and if there are any redundant instances of features
to pattern in Generic Tool of the pattern object, the model is corrupted
|
Redundant instances in Generic Tool of user
pattern are deleted
|
Instances available in Generic Tool of user
pattern are correct. Document can be updated.
Representation needs to be updated
|
PAT_1 (2)
|
Part Design
|
Some instances of the rectangular pattern
are lost after modifying the parameters of the occurrence feature.
|
The Generic Tool of the rectangular
pattern is corrupted. The location of the instance is wrong.
|
Removes the incorrectly located instances
and creates new instances at the right location regarding the pattern grid
definition.
|
The instances available in Generic Tool of the rectangular
pattern are correct.
Representation needs to be updated.
|
PAT_2 (2)
|
Part Design
|
If you select the edge/face of an instance
of circular pattern (made of user pattern), the edge/face of another instance
of circular pattern will be also selected
|
Generic naming of instances of circular
pattern was incorrect because of a confusion point in the user pattern. The
confusion point was not ignored during the naming of instances of user pattern
|
Confusion point is now ignored during the
naming of instances of user pattern. It leads to the correct naming of
instances of circular pattern
|
Each instance of circular pattern can be
selected individually. Representation needs to be updated
|
PAT_3 (2)
|
Part Design
|
The resulting geometry of the user pattern
is not displayed. Only the reference appears in the geometry.
|
The sketch used for the feature of the
generative tool (internal tool of a pattern) keeps constraints with external
geometry.
|
Removes constraints with external geometry.
Instances of the pattern are correctly located.
|
The result of the pattern is correct and all instances are
correctly located.
Representation needs to be updated
|
PAT_4 (2)
|
Mechanical Design
|
Some instances of the pattern are missing
|
The feature's plug in-out of the pattern's
internal tool is wrong.
|
Corrects the feature's plug in-out.
|
Instances are correctly displayed in the
geometry. The representation needs to be updated.
|
PAT_5 (2)
|
Mechanical Design
|
If we open older CATPart on a higher level
(CXR23 onwards) then in some cases it shows 'Object=No Selection".
|
The object to pattern attribute was not set
properly mostly by "RectPattern" which was created until "V5R14" level.
|
Corrects the object to pattern attribute.
|
The object to pattern of "RectPattern" is
displayed correctly when edited.
|
PIC_0 (3)
|
Drafting
|
Drawing picture disappears after a
copy/paste
|
Non aggregated picture
|
Deletes non aggregated Drawing picture
|
Representation is smaller
|
PIC_1 (2)
|
Drafting
|
When opening Drawing, reframe on is
infinite
|
Some pictures have been created with a
position set to a very huge value (value>float max value)
|
Modifies picture position value (set at
0;0) and moves to No Show space
|
New position set on picture to have a
correct reframe on when opening Drawing
|
SCS_0 (2)
|
Sketcher
|
Sketch solving result is not stable.
Geometries can move when the sketch is edited
|
Some geometrical constraints do not have
Help parameter. This parameter is used
by constraint solver to help solving the sketch
|
Adds missing
Help parameter to sketcher constraint
|
Solving result is stable. When editing a
sketch, geometries do not move.
Representation needs to be updated
|
SHM_0 (2)
|
SheetMetal
|
Some SheetMetal objects cannot be
deactivated
|
Information managing the activity is
missing on some SheetMetal objects
|
Adds information. The activity will be at
Yes after the operation
|
Activity is at
Yes.
Representation needs to be updated
|
SHM_2 (2)
|
SheetMetal
|
Some functionality like
CutOut,
Hole, etc. fail if they are created on
the part
|
Failure occurs during unfolding transaction
because all cylindrical transformations are not correctly defined
|
Restores invalid cylindrical transformation
to a valid one
|
Failing functionality can be applied
successfully.
Representation needs to be updated
|
SHM_5 (2) |
SheetMetal |
When a sheet metal feature is deactivated, the
previous sheet metal result is damaged |
The sheet metal feature storing the result of the
previous sheet metal feature result is inactive |
The inactive sheet metal feature result is
restored with the proper results |
The inactive sheet metal feature is
restored. Document needs to be updated. |
SHM_6 (2) |
SheetMetal |
When a sheet metal feature is activated, the
previous sheet metal result is damaged |
The sheet metal feature storing the result of the
previous sheet metal feature result is inactive |
The active sheet metal feature result is
reconstructed. |
The feature is not up-to-date. Document needs to
be updated. |
SKS_2 (2)
|
Sketcher Modeler
|
O point, H and V vectors of the absolute
axis of the sketch are missing in the tree and are not visualized
|
O point, H and V vectors of the absolute
axis of the sketch are missing in the model
|
Recreates missing elements of the absolute
axis of the sketch
|
O point, H and V vectors of the absolute
axis of the sketch are in the tree and in the 3D visualization.
Representation needs to be updated
|
SKS_3 (1)
|
Sketcher Modeler
|
Data cannot be imported in
3DEXPERIENCE
using FBDI
|
The SketchSupport must be aggregated under
a father element
|
Removes the non-aggregated SketchSupport
|
Data can be imported using FBDI
|
SKT_0 (1)
|
Sketcher Modeler
|
Sketch absolute axis is seen as up-to-date,
but there is no resulting associated geometry
|
Operations within the Sketcher cannot be
performed properly
|
Marks non up-to-date absolute axis
|
Sketches are seen as not up-to-date.
Representation needs to be updated
|
SKT_27 (2)
|
Sketcher Modeler
|
Output features are badly aggregated
|
Output features are aggregated as brothers
of the sketch they are from and not under the dedicated node in the sketch
|
Modifies the aggregation of such outputs.
The outputs are replaced under the dedicated node under the sketch they belong
to
|
|
SMG_16 (2)
|
Sketcher
|
Updates of sketches must be performed many
times to get sketches updated
|
Constraints re-impacted during the feature
update
|
Corrects constraints update
|
Result of the update is correct. Sketches
are seen as not up-to-date.
Representation needs to be updated
|
SSS_1 (3)
|
Mechanical Modeler
|
Selective loading on documents having
selection sets containing elements outside their scope can have unexpected
behaviors.
|
Selection set contains elements that are outside its scope. It was
created before selecting elements outside the scope of a selection
set that was prohibited. It is recommended to delete the selection
set and to create another one containing only elements within its
scope. If you decide to keep the selection set as is, this might
generate invalid links |
Non fixable error.
The message associated to the rule recommends you to
delete the selection set and to create another one containing only elements
within its scope
|
Non fixable error.
The message associated to the rule recommends you to
delete the selection set and to create another one containing only elements
within its scope
|
TER_0 (2)
|
Mechanical Design
|
Update status of the Technological Result
node does not change when adding/modifying a feature in the body. The
consequence is that the technological result information may be inconsistent
with the body content
|
Output is not plugged to the last shape
feature (or its ResultOut) of the tool in which it has been created
|
Re-plugs invalid Technological Result
Output to the last shape feature (or its ResultOut) of the tool in which it has
been created
|
Update status changes when adding/modifying
a feature in the body.
Representation needs to be updated to refresh Technological
Result information
|
THD_1 (3)
|
Part Design
|
A relation has been defined on the Thread
Description attribute of a Thread with an external parameter. Changing the
value of the external parameter does not update the Thread Description through
the relation, which creates an error in the Thread feature
|
Thread Description attribute of Thread is
sp_NEUTRAL. This attribute is linked to an external parameter through a
relation. Change in value of the external parameter does not lead to update of
Thread Description through the relation before the update of the Thread
feature. Hence, the Thread feature is in error
|
Thread Description attribute is made an
sp_IN attribute, thus change in value of external parameter leads to the update
of Thread Description through the relation, before the update of PartBody. This
results in valid update of the Thread feature
|
Part needs to be saved because of the
change in attribute quality
|
UPD_0 (2)
|
Specs Modeler
|
Update cycle on the object cannot be
seen/edited
|
An object has been created which is a
direct input of itself in terms of update
|
Unsets the link to itself (breaks the
cyclic dependency)
|
Update should no longer fail due to the
update cycle
|
UPD_2 (2)
|
Specs Modeler
|
Update status: propagation problem. Data
which should be not up-to-date is shown as up-to-date
|
The update stamp limit has been reached
(MinInt = -2147483647) and the last feature modification has not been detected
by the update engine
|
Increments the update stamp of the feature
|
Representation may need to be updated if
impacted features are active and belong to an update graph of the document
|