The proposed formats are:
- Default format with plies group column with
the following template:
Plies Group
|
Sequence
|
Ply
|
Material
|
Orientation
|
Starting Plane
|
End Plane
|
LEFT LIMIT
|
Offset
|
RIGHT LIMIT
|
Offset 2
|
|
|
|
|
|
|
|
|
|
|
|
- Default format without plies group column with
the following template:
Sequence
|
Ply
|
Material
|
Orientation
|
Starting Plane
|
End Plane
|
LEFT LIMIT
|
Offset
|
RIGHT LIMIT
|
Offset 2
|
|
|
|
|
|
|
|
|
|
|
- Long skinny part format (4 limits & 4
offsets) with the following template
Plies Group
|
Sequence
|
Ply
|
Material
|
Orientation
|
Limit 1
|
Offset 1
|
Limit 2
|
Offset 2
|
Limit 3
|
Offset 3
|
Limit 4
|
Offset 4
|
|
|
|
|
|
|
|
|
|
|
|
|
|
Default Format with or without Plies Group Column
Both formats require a reference plane.
For example, the data found in this spreadsheet

are used to create the grid reference elements, taking the
reference plane into account. In the images below:
- 1 is the reference plane.
- 2 is the starting plane. 2000 is its distance to the reference
plane (smaller double-headed arrow).
- 3 is the end plane. 4000 is its distance to the reference plane
(longer double-headed arrow).
- The left limit is shown in pink.
- The right limit is shown in red.
Other required inputs are:
- The
Grid panel.
- The
Ramp supports step.
- The
Construction Inputs such as the
Parallel type and
Parallel mode. See
Specifying a Ramp Definition
for more information.
Long Skinny Part Format (Limits and Offsets)
For the following data
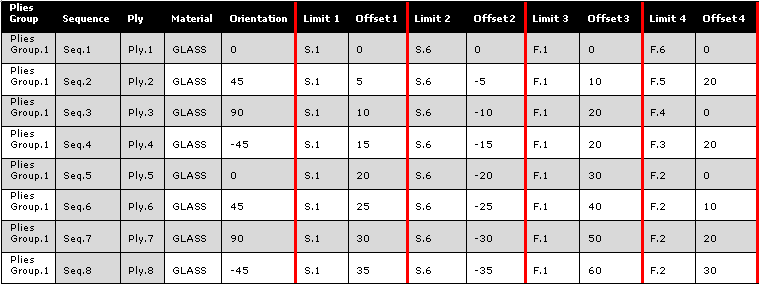
import requires:
- The
Grid panel that contains the Reference
Elements (S.1...S.6, F.1...F.6) to create the grid reference elements.
- The
Ramp supports step.
- The
Construction Inputs such as the
Parallel type and
Parallel mode. See
Specifying a Ramp Definition
for more information.
Note:
The
Ramp supports step is the default step used to
create all the automatic ramp supports. If the offset values are not a multiple
of this step, the import stops.