You can choose to retain the initial ply shell curvature or
tangency constraint on the first pair of curves, on the last pair
of curves, or on both pairs of curves.
For each ply, the ply shell is computed, then the ply shell is deformed. The following
diagrams help you understand how the deformation is computed in relation to the entered
data, that is, reference/target curves and possible spine.
3D view, where:
- r1, r2 are the reference curves,
- t1, t2 are the target curves,
- P is a plane normal to the spine (orange line).
Planar view, where:
- Ir1: is the intersection between P and r1,
- r2: is the intersection between P and r2,
- It1: is the intersection between P and t1,
- It2: is the intersection between P and t2.
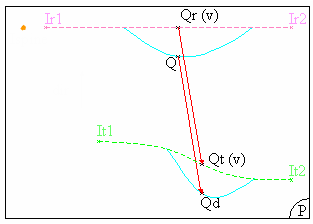
The deformation is
computed in each plane P, normal to the spine.
In each plane P, the system computes the intersection between the plane and each
curve.
A curve (Cr) is created between the first intersection point (Ir1) and the
last intersection point (Irn) on reference curves, passing through all the intersection
points between these two.
Similarly, a curve (Ct) is created passing through all
the intersections points between the first (It1) and the last intersection point (Itn)
on target curves.
Then, for each point Q, resulting from the intersection of the surface to be deformed
with the plane, Q is projected onto the curve Cr according to the projection direction
(dir).
This projection direction is the vectorial product of: Vector(lspine, lr2)
^ vector normal to P.
The result of the projection of point Q is the point Qr,
its parameter on Cr is v.
Similarly, a point Qt is created on the curve Ct, with
the same v parameter as point Qr on curve Cr.
Then Qd, that is the transformation
of point Q according to the wrap curve deformation, is obtained by adding:
Q+vector(Qr,Qt).
The boundary of the deformed ply shell is computed and is
specified as the result contour of the skin swapping.