The
rosette is an axis system positioned on the part.
- It is defined in Composites Parameters.
- Its representation in the 3D area looks like this
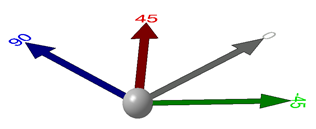
- The represented orientations depend on those defined in Composites Parameters.
- Only orientations between -180° and 180° are represented.
- Within that range, each orientation is represented by an arrow and its value.
- There is only one arrow per orientation value.
- The color of the arrow matches that of the orientation.
- Reframe On and Center tree commands are available.
- Double-click the rosette to edit it.
- You can define the rosette zoom behavior.
The Rosette Transfer defines how the rosette is positioned at any location of the reference surfaces of the Composites design. At this location, the X-axis of the rosette corresponds to the 0° orientation of the fiber. This information is of high value for the designer.
- The rosette transfer type is defined during the rosette definition.
- Modify the transfer type to allow the selection of multiple geometric entities or the specification of parameters.
- It cannot be updated, but an update error is displayed when an input is missing.
- It does not have a 3D area representation.
3DEXPERIENCE proposes several types of rosette transfer:
- Cartesian
- At a given point, the rosette is transferred on a plane tangent to the reference surface. The computation is performed only by geometric transformations of vectors.
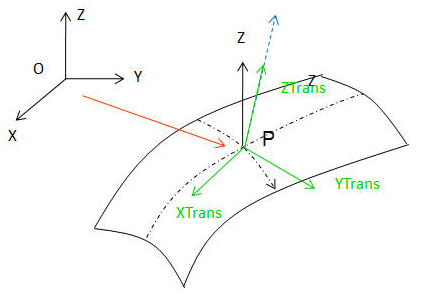
- Guided by Curve
- The X-axis of the rosette sweeps along the guide curve (neutral fiber) to be brought to the
plane tangent to the reference surface at this point.
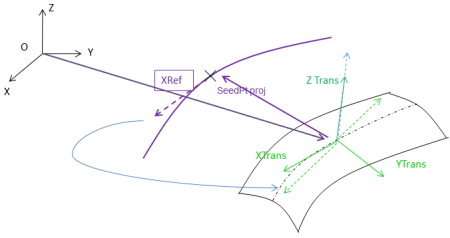
Two options are proposed:
- 0° guided by curve where the tangent to the guide curve
is the 0° orientation, that is, the X-axis of the rosette.
- 90° guided by curve where the tangent to the guide curve
is the 90° orientation.
- External
- Dedicated to external CAA users.
Cartesian Vs Guided by Curve
With the
Cartesian type, if the angle between ZTrans and X is small (less
than 10°), the result of the scalar product may vary a lot as in the example below. The
reason is that the X-axis of the rosette is locally closed to the normal of the surface at
the point.
In the example below, the white axis system is the initial rosette. The red
circle shows the transferred rosettes.
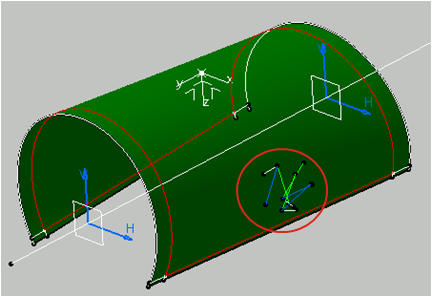
The pertinency of the rosette
transfer depends on the position of the point on the surface and on the shape of the surface.
For U-shaped surfaces, the guided by curve transfer type is recommended: The transferred
rosettes are more stable, thanks to the neutral fiber.
In the example below, the red circle
shows the rosettes transferred in relation with the neutral fiber, shown by the red arrow.
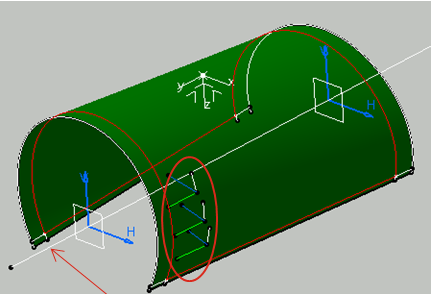
Downward Compatibility
When opening an older model, you are asked to upgrade it to the new rosette feature. This upgrade
is done in two steps:
- Migration to the extended laminates, if pertinent.
- Migration to the new rosette feature. This step is only available after the first one
has been completed.
- A report is available at the end of the migration.
Note:
Migrate both Engineering and Manufacturing stackings, or mirror parts, or
stackings to merge before synchronization.
The migration to the new rosette feature is done as follows:
- Only nonidentical rosette features are created (identical rosette features have the same axis
system, rosette transfer type and transfer type inputs).
- A rosette feature is created for each axis system referenced by a Composites entity. This axis system becomes an input of the rosette.
- The rosette transfer type of this rosette feature is given by the grid panel, or the plies group, or the zone group.
- If two transfer types exist for one single axis system, one rosette feature is created for each axis system/transfer type couple.
- If a ply has a different axis system than its ply group, an additional rosette feature is
created with the axis system of the ply and the rosette transfer type of the ply group.
This also applies to cut-pieces/ply, zone/zones group and virtual ply/grid panel.
Examples
The impact of the rosette transfer is quite visible in Fiber Direction. In the images below, the rosette is the white axis system. The other axis systems are transferred rosettes at different locations on the surface. In those axis systems, the green line is the X-axis of the transferred rosette, and the white line its Y-axis. The green line corresponds to the 0° orientation of the fiber. In this example, the 45° orientation of the fiber is represented by the blue line.
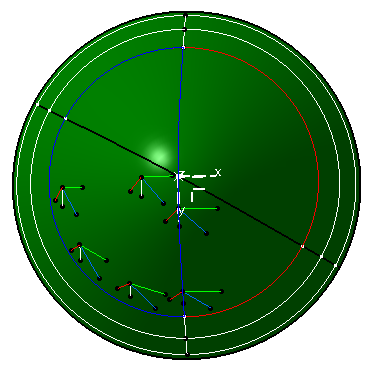
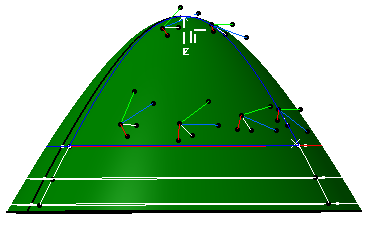
With Producibility, the rosette is transferred on the seed point.
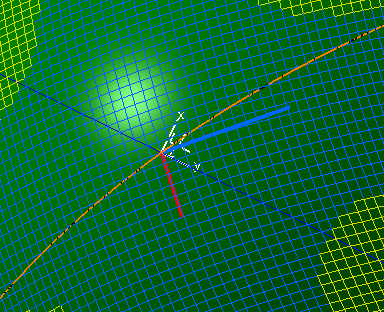