-
From the Markup section of the action bar,
click Section
.
You can also select the geometry before launching the command. The selected geometry
is used to define the section plane. Based on the type of geometry, more geometry
selections might be required.
A section plane appears, cutting through the object. A context toolbar also appears.
-
Optional: To customize your section, choose from the following options in
the context toolbar:
Note:
Depending on their position, some markup objects (such as measurements or
annotations) can be hidden to improve the display of cut objects.
-
To position your section plane, choose from the options available in the filter bar.
Filters let you position the section by snapping the Robot on the respective geometry type.
Option | Description |
---|
Point
 |
The Robot is snapped on a point and the axes of the Robot are mapped to the reference axes of the root product. |
Center
 |
The Robot is snapped on a center of a circle and the axes of the Robot are mapped to the reference axes of the root product. |
Axis System
|
The Robot is snapped on an axis system. |
Line
 |
The Robot is snapped on a line. The origin is the point on the line where it is snapped and
the w-axis lies on the line. |
Plane
 |
The Robot is snapped on a planar surface. The origin is the point where it is snapped and the
w-axis is normal to the planar surface. |
Cylinder/Cone
 |
The Robot is snapped on a cylindrical or conical surface. The origin is the intersection
point between the axis of the cylinder or cone and the line normal to this axis,
passing through the point where the Robot is snapped. |
Surface
 |
The Robot is snapped on any surface. The origin is the point where it is snapped and the
w-axis is the line normal to the surface. |
Product
 |
The Robot is snapped on the plane formed by the two of the main axes, closest to the viewer
plane. The Robot is positioned at the center of the product bounding box. |
Note:
For all the filters except the surface and product filter, the high quality
representation of the selected geometry is loaded in the session.
For line, surface, cylinder, cone, plane, and product, a temporary
representation is displayed while snapping the Robot.
-
Change the position of the section plane using one of the following methods:
Areas that can be manipulated are highlighted when you hover your mouse over
them.
- To rotate the plane, drag its edges.
- To resize the plane, drag its corners.
- To position the plane on a specific surface of the object, use the Robot and the ruler, to position it precisely.
Notes:
- You can manually position the origin of the ruler.
- You can enter the required value on the ruler for exact positioning of the
section plane.
- In 3DPlay Web App, the ruler is displayed with less opacity.
- To translate the section plane, you can:
- Drag its surface
- Drag the Robot handles and enter the required value on the rule.
- Drag the slider to translate the
section plane by the specified increment value.

Note:
To
specify the increment value, click View Menu
and
enter the required value in the Increment box. The
increment value should be between the minimum and maximum increment values that
are computed as below:
- Maximum increment value: closest & lowest decimal value to the
distance between near and far planes divided by 10)
- Minimum increment value: closest & lowest decimal value to the
distance between near and far planes divided by 100)
The near plane is the
plane parallel to section plane and tangent to the assembly bounding
sphere which is the nearest to the viewing position. The far plane
is the plane parallel to the section plane and tangent to the assembly
bounding sphere which is the farthest to the viewing position. For
example:
- If the distance between near and far plane is 333 mm, the maximum
increment value is 10 mm (333/10 = 33.3 ~ lowest decimal value is 10).
While the minimum increment value is 1 mm (333/100 = 3.33 ~ lowest
decimal value is 1).
- If the distance between near and far plane is 7500 mm, the maximum
increment value is 100 mm (7500/10 = 750 ~ lowest decimal value is 100).
While the minimum increment value is 10 mm (7500/100 = 75 ~ lowest
decimal value is 10).
You can also select the Detailed View option
to replace the slider with the value box for precise positioning of the section
plane. You can enter the precise position within a specific range, otherwise, the
closest limit value is taken into account. The range is the distance between
near and far plane. Notes:
When the w-axis of the section plane is
aligned with one of the axes of the global axis system, the origin is the as same
of the global axis system. If after manipulation, the w-axis of the section plane
is not aligned with one of the axes of the global axis system, the origin is same
as that of the origin of the Robot. In this case, the origin is reset every time you start the edition of section
plane.
- Optional:
To see the cut elements more clearly and access them more easily while creating the
section, click Hide Section Plane
.
The section plane is hidden. You can now measure items that were previously not
accessible because to the section plane. For more
information, see Measuring Items.
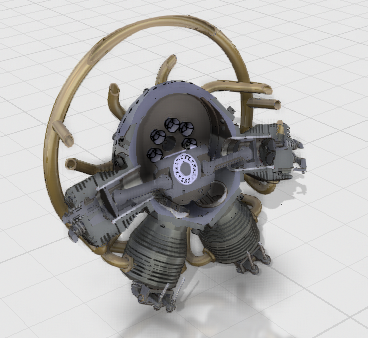
To display the section plane again, click Hide Section Plane
.
- Optional:
To see the contours on the section plane, do one of the following:
- From the Tools section of the action bar,
click Preferences
and select the Compute contour check
box.
- Right-click the section plane, select Properties
, and then in the Section tab, select
the Compute contour check box.Notes:
- You can choose to compute contours for one or more sections, using this
contextual command.
- The contours are displayed only if the loading is already complete.
|