-
From the Surface Machining section of the action bar, click
Stiffener.
A Stiffener entity is added to the
manufacturing program.
The Stiffener dialog box opens at the Geometry tab  .
-
Still in the Geometry tab:
- Click the red area representing the part to machine.
The dialog box disappears.
- Select a part.
- Double-click anywhere in the work area to validate the selection and revert to the dialog box.
The red area has turned green.
- Click Bottom and select it.
The bottom of the part must be selected before searching the stiffeners, especially in symmetric parts: The faces under the bottom plane are then ignored. - Go to the Strategy tab
and define the tool axis.
As stiffeners are searched for in the part, with respect to the tool axis, you need to define both before starting the selection of stiffeners. -
Back in the
Geometry tab, click the red area representing the Drive.
- In the Face Wizard that appears, click Stiffener Selection
.Automatic detection of the stiffeners will select most stiffeners. You need to select the rest manually. See Selecting Faces to Define Geometry for more information. The Stiffener selection dialog box appears with a sensitive icon on the right and selection criteria on the left.
- Define the Width of the stiffeners, with a possible +/- tolerance.
- Define the domain of the search by selecting the corresponding check boxes.
- Horizontal planes. Requires no other input.
- Inclined planes. You must enter the value of the Slope, with a possible +/- tolerance.
- Fillets linked to planes. You must enter the Radius, with a possible +/- tolerance.
- To retrieve an existing Slope, Width or Radius value:
- In the Stiffeners Selection dialog box, pick the corresponding representation.
The dialog box vanishes. - Pick the corresponding area on the part.
The Stiffeners Selection dialog box re-appears. The value has been updated with the existing one.
- Click Add.
The faces corresponding to the criteria are added to the selection.
- Repeat this scenario with other values as needed to complete the
selection.
- Click Close when the selection is complete.
- Back in the machining operation dialog box, select the Radial tab and select the Activate radial steps check box to create radial passes along the inclined stiffeners.
They are created only if a single pass is not sufficient to remove all the material. - Select to the Tools tab
to select a tool.For most cases, use a milling cutter with a radius to work from bottom to top.
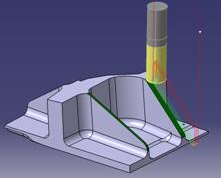 and a large milling cutter to ensure a good quality on planes.
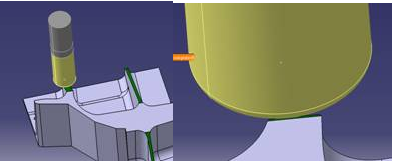
-
Click Display or
Simulate to check the validity of the machining operation.
- The tool path is computed.
- A progress indicator is displayed.
- You can cancel the tool path computation at any moment before 100% completion.
|