- Activate the Manufacturing Program.
- Select
Axial Machining
section.
- Click Drilling
. -
Select the Macro Parameters tab in the Machining Operation dialog box.
The initial status of all the macros in the Macro
Management list is Inactive
 .
- Right-click the Approach
macro line and select Activate in the context menu.
Note:
You can also activate or deactivate macros by double-clicking an item in
the list.
The macro line is activated.  Turns to  , meaning
some definition data exist but may require modifications. - In the Current Macro Toolbox, select
the Circular horizontal axial mode from the list.
A sensitive icon representing the three
elementary paths of this macro appears.
- Double-click each elementary path
to display a dialog box that allows you to specify the
exact characteristics the path.
The current elementary path is displayed in magenta. -
In the dialog box corresponding to the circular path, set the
Radius to 15 mm and the Angular section to 90
deg with the Angular orientation at 0 deg. To have a 10mm vertical path
followed by a 15mm radius circular path.
The sensitive icon is updated. 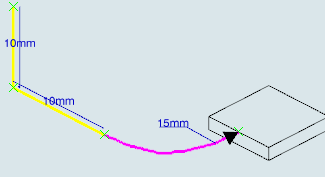
-
Click Display or
Simulate to check the circular approach.
The yellow light turns to green, meaning the data are
up-to-date.
- Under Macro Management:
- Activate the Retract
macro line and create a circular
retract macro.
- Activate the Linking Retract macro line and select
Axial. Assign a 20mm value to the retract
path.
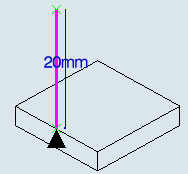
The Linking Approach/Retract macros have a common behavior and are seen
as the same object. It allows to handle
Activate/Deactivate for both
Approach and Retract.
Consequently, they share the same name and you cannot rename one
independently from the other. The same applies to Between
passes and Between passes link
macros. - Select the Linking Approach
line, then select the Axial
mode. Assign a 20mm value to the approach path.
- In the Options tab, select
the Cornerized clearance with radius check
box, then enter a corner radius value of 3mm.
-
In the Display or
Simulate dialog box, select the Different colors mode to
visualize feedrate changes.
The tool path is
displayed with the following default colors:
- Yellow: Approach feedrate
- Green: machining feedrate
- Blue: retract feedrate
- Red: Rapid feedrate
- White: user-defined feedrate.
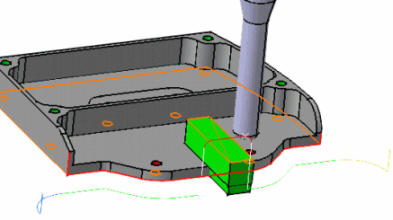
Note:
Transition Paths are represented by dashed white
lines.
The statuses of the macros are now Up to date.
- Click OK
The Machining Operation is
updated with the specified macros.
|