Table 1. Simulation Results
Choose Results |
Part Operation/ Program |
Recent Activity |
Scenario Results |
Simulation Results
You can choose which simulation result to display in the dialog box with the
Choose Result options.
- Choose Result
-
- Part Operation/ Program: Results from a part operation or manufacturing program.
- Recent Activity: Results from the latest
single or multimanufacturing operation.
- Scenario Results: Results from the latest
scenario computation (applicable only with MSR context).
If you start another simulation on a part operation or manufacturing program, then the existing Part Operation/ Program list clears and a new list takes its
place. In this case, the Recent Activity list also clears since they are now
irrelevant.
If you start a new Recent Activity simulation, then the new results overwrite the old
results. This only occurs for the Recent Activity list while the Part Operation/
Program list remains uncleared.
If you start a scenario computation or you view already computed results through
View scenario clash results, the Recent Activity list
results are cleared and the new results are displayed under Scenario
Results.
If you recompute the toolpath of an activity, then the faults that correspond to that
activity in the Part Operation/ Program list are marked as out-of-date.
Fault Type
The Fault Type contains the following options:
- Types of faults
-
Note:
The design part must be closed and this is only available for milling
simulation.
The fault type also displays which part of a tool (shank, holder, and so
on) is in collision with which solid (rough stock, fixture).
The following items are available when you right-click a collision:
Clash is between:
- Non cutting part of tool, such as a shank, holder, or a non cutting
area at the tool center.
- Versus rough stock or fixture.
Or
- Cutting part of tool in Rapid movement.
- Versus rough stock or fixture.
Therefore the Tool Clash is: Rapid – rough stock,
Rapid – Fixture, Shank – rough stock, Shank – Fixture, Holder – rough
stock, Holder – Fixture, NC Center –
rough stock, NC Center – Fixture.
The following items are available when you right-click the
Fault Type header:
- Filter on Travel Limit Exceed
- Filter on Tool Clash
- Filter on Gouge. See Volume.
It is possible to create the
gouge solid to add measures with standard CATIA commands
after leaving simulation. This is then analyzed in
Shape > Digitized Shape
editor. See Export the gouge solid as a CldPolygon.
When Filter on gouge or when selecting
a gouge, all gouge solids are displayed in the work area.
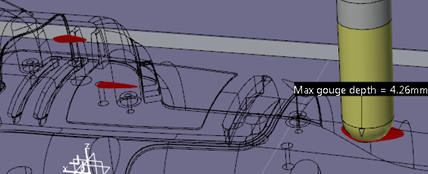
An arrow is pointing the current gouge solid with a max
depth information. When a gouge is Set
solved, the solid is displayed in green
color
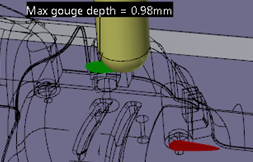
.
When the clearance mode is activated with a positive
clearance value, the fault is reported in the
Fault List as a Clearance with
this specific icon
. The faults are also be filtered by a Clearance.
When a gouge is selected, the rough stock is not displayed.
To display the design, click Hide/Show Parts
Elements
in the View section of the action bar.
- Show All
Activity Name
Shows the activities that were being simulated when the fault was detected. The icon
corresponding to the activity appears.
- Activity context menu
-
The following items are available when you right-click the clash
activity:
- Definition: Opens the manufacturing
activity list.
- Filter: Allows you to filter the faults
based on the activity.
- Show All: Displays all activities.
The menu options Previous Operation and
Current Operation allow you to choose between
the first and last collision activity in the fault list. They are
available for link/transition collisions only.
Tool
- Tool context menu
-
The following items are available when you right-click a tool:
- Filter on Assembly
- Show All
Volume
- Volume context menu
-
It is possible to filter by volume:
- Sort Smallest to Largest
- Sort Largest to Smallest
- Show All
The volume is computed for a clash between a tool and the rough
stock-fixture only during a material removal.
For others problems (Travel limit…), no volume is computed and
None appears in the column.
Note:
The context menu in the Volume column gives you the ability
to Filter on Volume or Show
All status.
Time
- Time context menu
-
Shows the simulation time when the fault was detected. This time is based
on the simulated activity.
Notes:
- If you perform an ISO-based simulation, an additional column
appears to indicate the ISO Line that caused the fault.
- You can report several collisions at the same time and
select one of the collision lines in the Fault
List. In this case, the actual point of
collision is indicated by a red cross in the work area and not by the machine or tool position. This case may
occur when the time step used for simulation is higher than
the time required for the cut duration between consecutive
tool
path points.
- Depending on the time step or mode chosen for simulation,
the Travel Limit fault can appear several times in the
Fault List.