Motions Parameters
Properties
- Edits the motion selected in the dialog box.
Delete
- Deletes the motion selected in the dialog box.
and 
- Changes the rank of the motion selected in the dialog box.
Goto Point
- Creates a tool motion
defined by the point the tool tip has to reach. Geometry is selected as follows:
- Direct selection on the part (points, vertices, and so on)
- Direct indication in a pre-selected surface.
Only selection done within the topological limits of the surface
are taken into account.
- Indication of points to be projected onto a user-defined
indication plane.
This indication plane is considered as infinite (it has no
topological limits). This allows point indication outside the part
boundaries. It is a temporary element used as an aid for
selection. It is not saved after operation edition.
Go Delta- Creates a tool motion defined by a displacement relative to a previous
Goto Point, Goto Position or Go Delta motion location. Types of Go Delta
motion are defined from the dialog box that appears, and are as follows:
- Components: relative motion defined by DX , DY, and DZ
displacements from previous motion location.
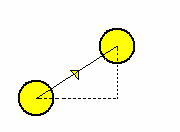
Specifies DX , DY, and DZ displacements.
- Along X axis: relative motion along X axis (current axis system) on a specified Distance, from previous motion location.
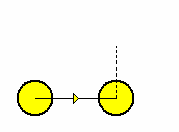
Specifies DX displacement.
- Along Y axis: relative motion along Y axis (current axis system) on a specified Distance, from previous motion location.
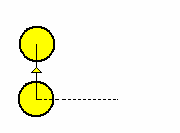
Specifies DY displacement.
- Parallel to Line: relative motion on a specified
Distance, parallel to a selected Line, from previous motion
location.
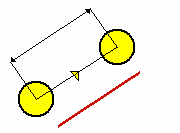
Specifies Offset and Local feedrate.
- Normal to Line: relative motion on a specified Distance, normal to a selected Line, from previous motion location. The tool motion is done in a plane perpendicular to the tool axis.
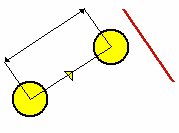
Specifies Offset and Local feedrate.
- Angle to Line: relative motion on a specified
Distance, along a line computed from defined Angle and Line.
The tool motion is done in a plane perpendicular to the tool axis.
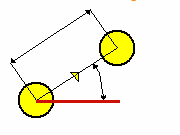
Specifies Angle, Offset, and Local feedrate.
Goto Position
- A tool motion is defined by positioning the tool in contact with a
part element, a drive element, and possibly a check element, while
taking To / On / Past conditions into account. The tool axis for
this motion is perpendicular to the selected part.
It is defined from the dialog box that appears:
- Part
- Select part element in the 3DEXPERIENCE platform.
- Part thickness
- Specifies part thickness.
- Position on drive
- Specifies To / On / Past positioning conditions.
- Offset on drive/check
- Specifies drive and check offsets.
- Position on Check
- Specifies To / On / Past / Tgt positioning conditions.
PP words- Insert PP words.
Strategy Parameters
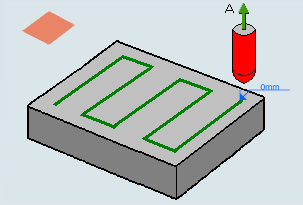
- First compensation
- Specifies the tool corrector identifier to be used in the operation. The corrector type (P1, P2, and P3, for example), corrector identifier,
and corrector number are defined on the tool. When the NC data
source is generated, the corrector number is generated using
specific parameters.
- Machining tolerance
- Specifies
the maximum allowed distance between the theoretical and computed
tool path.
- Offset along tool axis
- Defines
an offset along the tool axis for all positions of the tool path
(it is taken into account for all the positions of the operation).
Feedrates and Speeds Parameters
- Transition
- You can locally set the feedrate for a transition path to a
machining operation B from a machining operation A or from a tool
change activity. This is done by selecting the Transition check box in the Machining Operation dialog box for
operation B.
For more information, please refer to the Setting a Transition Feedrate.
- Spindle output
- This check box manage output
of the SPINDL instruction in the generated NC data file:
- If the check box is selected, the instruction is generated.
- Otherwise,
it is not generated.
Note:
The spindle speed is defined in linear (length per minute) or angular (length per revolution)
units.
- Angular: length in revolutions per minute and unit is set to mm_turn.
- Linear: length in feed per minute and unit is set to mm_mn.
- Quality
- The feed and speed values are computed according to the
Quality setting on the operation.
- Compute
- Feeds and speeds of the operation is updated according to tooling feeds and speeds by clicking the Compute button located in the Feeds and Speeds tab of the operation.
Feeds and speeds of the operation is updated automatically
according to tooling data and the rough or finish quality of
the operation. This is described in
Updating Feeds and Speeds in Machining Operations.
NC Macros
You can define transition paths in your machining operations by means
of NC macros:
- Approach: to approach the operation start point,
- Retract: to retract from the operation end point,
These transition paths are built from
elementary motions.
The proposed macro mode are:
For more information, please refer to the Defining Macros.
The following macros are available in a Point to Point operation for Build by user macro mode:
Axial motion
PP word
Axial motion to a plane
Distance along a line motion