Root Product | Before Simulation | Last Simulated Position in the Mechanism Player | After Closing the Mechanism Player | After the PLM Update |
Case 1: an instance of a submechanism | 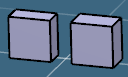 | 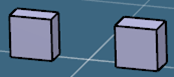 | 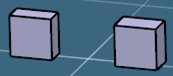 | 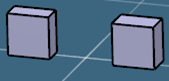 |
After both commands, the simulated position of the parts is
saved. The Nominal Mode is applied: the new
configuration of the mechanism is saved as the permanent configuration of the
model. |
Case 2:- n instances of a submechanism
- a flexible product
- commands with no values
| 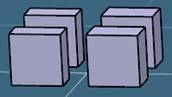 | 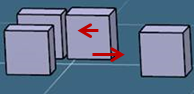 | 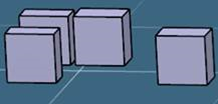 | 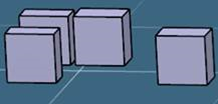 |
After both commands, the parts' simulated position is different and maintained. When several instances of the same mechanism can be animated, their position is kept only if the current mechanism contains a flexible product without controlled constraints. The instances keep a different position, with respect to the father. |
Case 3:- n instances of a submechanism
- product not flexible
| 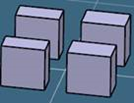 | 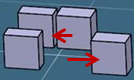 The
instances move in different directions. | 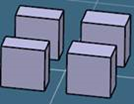 | 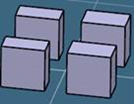 |
After both commands, the parts move back to their initial
position. If a product is not flexible, the nominal position is not applied. Note:
if
the parts have the same simulated position with respect to the father product, then
the simulated position is kept, like in Case 5.
|
Case 4:- n instances of a submechanism
- a flexible product
- commands with values
| 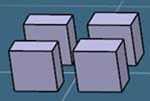 | 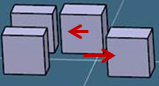 | 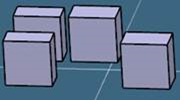 The parts' simulated position is maintained. |  The parts
move to have all the instances at the same positions. |
If you did not specify values for the constraints, the
position of a single instance is kept, while the others align to the same
position. |
Case 5:- n instances of a submechanism
- product not flexible
| 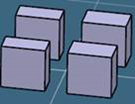 |  The
instances of the submechanism are in the same direction. |  |  |
After both commands, the parts' simulated position is maintained if it is the same, with respect to the father. |