By default, the Automated FEM creates one child FEM representation for each leaf product to be meshed and one FEM
representation that assembles all the child FEM representations. This is known as an assembly
of meshes. Alternatively, you can change the Automated FEM execution options to create one FEM representation for the entire assembly (a mesh of
assembly). The
following image displays how each type of meshing references the geometry of each part in an assembly:
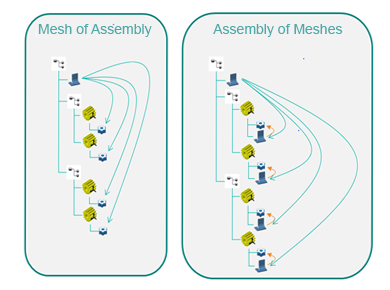
- Mesh of Assembly
- One mesh is created at the assembly level for geometry of the entire assembly. The mesh
references the 3D Shape representations for each part within the assembly to mesh the
entire assembly. This option can be faster to configure, but does not provide as much
control for specific parts of the mesh.
- Assembly of Meshes
- A mesh is created at the part level for each part in an assembly. Each mesh at the part
level references the 3D Shape representation for that part. There is also one mesh at the
assembly level that assembles the meshes for each part. With an assembly of meshes, you
can configure the FEM representation for each part. This can be useful to configure meshes
differently for parts with different geometries.