-
From the
Check and Repair section of the action bar, click Wall Thickness Analysis
. The Wall Thickness
Analysis dialog box appears.
-
Select the body of interest. The selected body is then set as the
current object.
-
Keep
Sphere as the computation method. The other
method available is
Ray.
-
Keep
Tolerance as the parameter defining the
calculation precision you want. The other possible parameters are tessellation
parameters:
Sag and Step.
-
Enter the value to define the tolerance you want. In this example,
enter 0.4mm. The analysis result will therefore fall within the specified
tolerance value.
-
Check the
Thread/Tap option if you want to integrate the
threads/ taps in the analysis. If the analyzed body contains threaded/tapped
holes, their specifications such as type or dimension will be taken into
account.
-
Click the
Colors tab to access ranges of colors for your
display.
-
Autoscale provides dynamic range scaling for
thicknesses. By default, the number of values to be used
to calculate different ranges is 10. For the purpose of our scenario, keep
this value. Setting 10 values lets the system compute 11 ranges of
thicknesses. A color is assigned to each range by the system. The bright red
color identifies the thinnest areas of the part, that is, the areas with
thickness greater than 0 mm and less than or equal to 10 mm. The blue colors
identify the thickest areas, that is, the areas with thickness greater than
90 mm and less than or equal to 100 mm.
-
Click
Run
to launch the analysis. The measure is performed over the
whole selected body. A window appears, informing you about the operation
progress.
When the computation is done, the colors assigned to the different value
thickness show the thickness variation of the part, so that you can
immediately observe critical areas where the thickness is not appropriate.
The part looks like this:
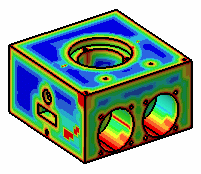
-
In case you are interested in only a few thicknesses and therefore
prefer to ignore some areas of the part, just clear the color you do not want
to display on the part.
-
For the purpose of our scenario, select all colors again.
-
Click the
Options tab to access display options. By
default,
On the fly is selected. This option lets you
know the thickness value at the point where you position your pointer on the
part. The value is displayed in mm, and is not persistent.
-
As you have chosen Sphere as a computation mode,
No sharp edge is available and selected by default:
this option filters out the areas close to edges and which thickness is less
than the value set in the corresponding value field. Let's look closely at an example. If you keep the default value, that is
1.1mm, we obtain this display:
-
Change the value to 2.1mm and look at the updated display:
-
Click the
Sections
tab
-
Right-click on the pad where you want the section cut to be done
and select
Add section at specified location. You can
also click
Section Cut
to display a section plane.
Click to add a new section or right-click on the red section and select
Add Section.
A new dialog box appears.
-
Name the section, choose the status among
None, To be
Reviewed, Refused,
Validated and
Unresolved.
By default, the status selected is None.
-
Choose the
severity from 0 (most severe) to 9 (least
severe).
By default, the severity selected is 3.
-
Click
OK
to close the Wall Thickness Analysis Section.
-
Click
OK to close the Wall Thickness Analysis dialog
box.
Analysis results are stored in the tree, below the Thickness
Analysis mode.
|