Typical Applications
Shear panel elements are special surface elements for modeling thin reinforced plates and shells, such as thin skin panels in aircraft wings and fuselage structures. These elements can transmit shear forces only along their edges (see Figure 1). They cannot transmit normal forces, and they have no bending stiffness. The shear panel elements should not be used alone and should typically be used together with reinforcing truss or beam elements.
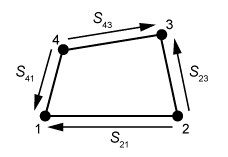
The elements have only displacement degrees of freedom. They are intended to be used only in small-displacement analyses. Large-rotation effects, thermal strain effects, and material/element-based viscous damping effects are not included. The elements can be used only with linear elastic material behavior.