Smoothing of Common Curved Surface Geometries
One method of surface smoothing applies to surface regions that are roughly axisymmetric, roughly spherical, or part of a toroidal surface. The smoothing method applies to general contact and surface-to-surface contact pairs. For example, the pin insertion model in Figure 1 could benefit from this smoothing: the body of the pin is cylindrical, the head of the pin is hemispherical, and the hole is conical. Surface-to-surface contact smoothing would also be effective if the surfaces were not perfectly axisymmetric, spherical, or toroidal; for example, if the pin body were slightly elliptical.
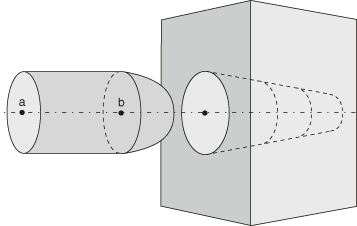
Effects of Contact Surface Smoothing
The impact of contact smoothing based on comparison of initial faceted surface geometry to initial idealized surface geometry can be demonstrated by a simple model. Figure 2 shows the initial mesh geometry for a two-dimensional model of concentric cylinders with an interference fit. The concentric cylinders are modeled with first-order elements of different sizes.
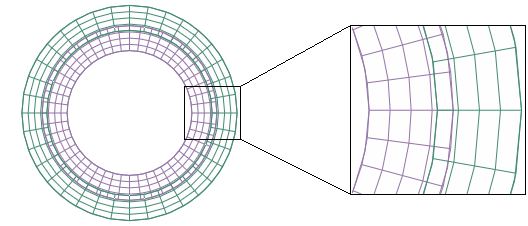
Discrepancies between the true surface geometry and the faceted surface geometry result in noise in the contact pressure solution if surface smoothing is not used. If the interference distance and resulting deformation distance is small with respect to the geometry discrepancy, this noise can have a significant effect on the accuracy of the solution. Although surface-to-surface contact typically handles these discrepancies better than node-to-surface contact, it is not unusual for the maximum deviation from the analytical pressure solution to be upward of 100%. The effects of the noise become less apparent for larger deformations, but they are never completely eliminated.
Applying Smoothing of Common Curved Surface Geometries to General Contact
Smoothing of common curved surface geometries for general contact is enabled by surface property assignments. Surface property assignments specify which surfaces are to be smoothed and the smoothing method to be used. The underlying geometry correction methods are the same for general contact and contact pairs:
-
The circumferential smoothing method is applicable to surfaces approximating a portion of a circle in two dimensions or a portion of a surface of revolution in three dimensions.
-
The spherical smoothing method is applicable to surfaces approximating a portion of a sphere in three dimensions.
-
The toroidal smoothing method is applicable to surfaces approximating a portion of a torus in three dimensions (i.e., a circular arc revolved about an axis).
For each surface, you must specify the appropriate geometry correction method and either the approximate axis of revolution (for circumferential or toroidal smoothing) or the approximate spherical center (for spherical smoothing). For toroidal smoothing, you must also specify the distance of the center of the circular arc from the axis of revolution, and the line joining point (Xa, Ya, Za) and the center of the circular arc should be perpendicular to the axis of revolution.
Example: Pin-in-Hole with General Contact
To improve contact pressure accuracy for the model in Figure 1, contact smoothing can be applied to both the main and secondary surfaces. Two different geometric correction methods are required for the pin (the secondary surface), so additional surfaces are defined corresponding to regions of the secondary surface. Spherical smoothing is defined for the tip of the pin. Since the body of the pin and the hole share an axis of revolution, circumferential smoothing is applied to both of these surfaces. This surface smoothing definition applies even if the cross-sectional shapes of the pin and hole deviate from perfect circles.
SURFACE INTERACTION, NAME=FRICTION1 CONTACT CONTACT INCLUSIONS PIN, HOLE CONTACT PROPERTY ASSIGNMENT , , FRICTION1 SURFACE PROPERTY ASSIGNMENT, PROPERTY=GEOMETRIC CORRECTION, DEFINITION=COORDINATES PIN_TIP, SPHERICAL, Xb, Yb, Zb PIN_BODY, CIRCUMFERENTIAL, Xa, Ya, Za, Xb, Yb, Zb HOLE, CIRCUMFERENTIAL, Xa, Ya, Za, Xb, Yb, Zb
Applying Smoothing of Common Curved Surface Geometries to Surface-to-Surface Contact Pairs
Smoothing of common curved surface geometries for contact pairs that use a surface-to-surface contact formulation is enabled by creating a surface smoothing definition. A contact pair definition references this smoothing definition to apply geometric corrections in the contact formulation (the physical geometry of the model is not altered).
The surface smoothing definition lists all of the faceted regions in the contact pair surfaces that must be smoothed, as well as the geometry correction method that should be applied to each region. Three geometry correction methods can be employed:
-
The circumferential smoothing method is applicable to surfaces approximating a portion of a circle in two dimensions or a portion of a surface of revolution in three dimensions.
-
The spherical smoothing method is applicable to surfaces approximating a portion of a sphere in three dimensions.
-
The toroidal smoothing method is applicable to surfaces approximating a portion of a torus in three dimensions (i.e., a circular arc revolved about an axis).
Each surface-to-surface contact pair refers to a single smoothing definition; therefore, a smoothing definition must list all of the smoothed regions and applicable geometry correction methods for the contact pair. Geometry corrections can be applied to main surfaces and to secondary surfaces; you can also apply corrections to selected regions of each surface. A surface smoothing definition can include multiple regions and different geometric correction methods for each region. For each region, you must specify the appropriate geometry correction method and either the approximate axis of revolution (for circumferential or toroidal smoothing) or the approximate spherical center (for spherical smoothing). For toroidal smoothing, you must also specify the distance of the center of the circular arc from the axis of revolution, and the line joining point (Xa, Ya, Za) and the center of the circular arc should be perpendicular to the axis of revolution.
Example: Pin-in-Hole with Contact Pairs
To improve contact pressure accuracy for the model in Figure 1, contact smoothing can be applied to both the main and secondary surfaces. Two different geometric correction methods are required for the pin (the secondary surface), so additional surfaces are defined corresponding to regions of the secondary surface. Spherical smoothing is defined for the tip of the pin. Since the body of the pin and the hole share an axis of revolution, circumferential smoothing is applied to both of these surfaces. This surface smoothing definition applies even if the cross-sectional shapes of the pin and hole deviate from perfect circles.
CONTACT PAIR, TYPE=SURFACE TO SURFACE, INTERACTION=FRICTION1, GEOMETRIC CORRECTION=SMOOTH1 PIN, HOLE SURFACE INTERACTION, NAME=FRICTION1 SURFACE SMOOTHING, NAME=SMOOTH1 PIN_TIP, , SPHERICAL, Xb, Yb, Zb PIN_BODY, HOLE, CIRCUMFERENTIAL, Xa, Ya, Za, Xb, Yb, Zb