Material Behavior
The real behavior of filled rubber elastomers under cyclic loading conditions is quite complex as shown in Figure 1.
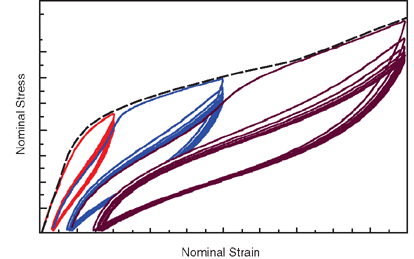
The observed mechanical behaviors are progressive damage resulting in a reduction of load-carrying capacity with each cycle, stress softening (also known as Mullins effect) upon reloading after the first unloading from a previously attained maximum strain level, hysteretic dissipation of energy, and permanent set. This section is concerned with modeling permanent set; therefore, the idealized representation of permanent set is described below.
Idealized Material Behavior
From Figure 1 it is clear that the observed permanent set is different for each cycle, but the material has a tendency to stabilize after a number of cycles of loading between zero stress and a given level of strain. For a given load level along the primary loading path shown with the dashed line in Figure 1, the idealized representation of permanent set will be a single strain value after unloading has taken place. Since rate and time effects are ignored in this model, idealized loading and unloading take place along the same path, whether Mullins effect is included or not.
The permanent set behavior is captured by isotropic hardening Mises plasticity with an associated flow rule. In the context of finite elastic strains associated with the underlying rubberlike material, plasticity is modeled using a multiplicative split of the deformation gradient into elastic and plastic components:
where is the elastic part of the deformation gradient (representing the hyperelastic behavior) and is the plastic part of the deformation gradient (representing the stress-free intermediate configuration).
An example of modeling permanent set along with Mullins effect for a rubberlike material can be found in Analysis of a solid disc with Mullins effect and permanent set.