Shear Plasticity Behavior
The shear plasticity model of the matrix is formulated in the local directions of the bidirectional fabric-reinforced material and is assumed to be decoupled from the response along the local 1 and 2 fiber directions. The following elastic relation gives the in-plane shear stress in terms of the elastic shear strain, :
where is the shear modulus of the matrix, is the total shear strain, and is the plastic shear strain.
The yield surface and flow rule are defined as:
where is the yield stress, is the equivalent plastic strain, and is the equivalent plastic strain rate.
The hardening behavior and strain rate dependency are incorporated into the yield stress assuming this separable form:
where is the static yield stress, and is a ratio, defined as at .
The hardening behavior defines the evolution of the yield surface size, , as a function of the equivalent plastic strain, . This evolution can be introduced by specifying directly as a function of in tabular form or by using the Johnson-Cook law:
where is the yield stress at zero plastic strain and and are material parameters. A schematic figure of the hardening curve based on the Johnson-Cook law is shown in Figure 1.
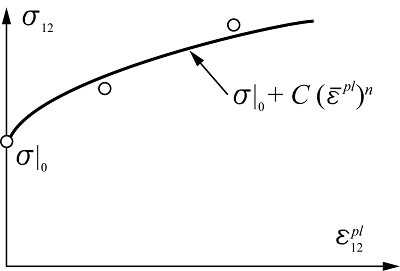
You can specify rate-dependent effects using the Cowper-Symonds overstress power law form or the Johnson-Cook form. For more information on these methods, see Rate-Dependent Yield.