A typical workflow for an eigenstrain additive manufacturing analysis is
outlined below. Each step corresponds to the sections displayed in the
Assistant.
Before you begin: Position the model within the workspace.
- Setup the model.
- Create or select a finite element model.
- Assign separate mesh sizes for the build geometry, the build
tray, and the supports.
- Define the shell thickness for the supports.
- Create the
Meshes.
- Define the
Part & Support Properties.
- Define an
Eigenstrain Library.
Choose a library that contains the strain patches used to represent
the buildup of layers in the additive manufacturing simulation. For more
information, see
About Additive Manufacturing Libraries.
- Specify the
Eigenstrain Assignment to define how the
material is activated.
Material is activated as it is deposited on the part by the
manufacturing process. The material activation includes a reference to the
library data and instructions for how the data is used to produce the model.
- Define an eigenstrain time constant to ramp up eigenstrains at
element activation.
Applying the eigenstrains gradually can aid in solution
convergence, especially if there is plasticity in the model. The default time
constant is zero.
- Define a build coordinate system.
The coordinate system is used as a reference for the build
direction (local direction 3), the eigenstrain patterns, and the scanning
regions in which eigenstrain patterns are assigned.
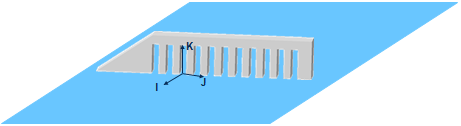
- Assign the slice thickness.
The slice thickness partitions the model into of slabs (slices)
of uniform thickness along the build direction. The slicing starts from the
base of the part.
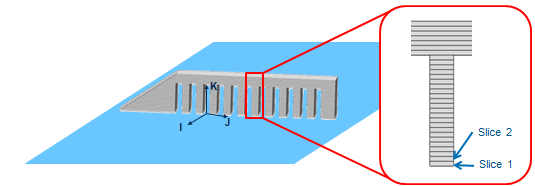
- Define one or more eigenstrain patterns.
An eigenstrain pattern is a rectangular domain that is
partitioned by a "quilt" of one or more patches. A patch is a rectangular area
that is assigned both an eigenstrain and a local rotation of the eigenstrain.
You assign the height and width of each patch. Ensure that the assigned sizes
and locations of the patches completely fill a rectangular area and that the
patches do not overlap. For more information, see
About Additive Manufacturing Libraries.
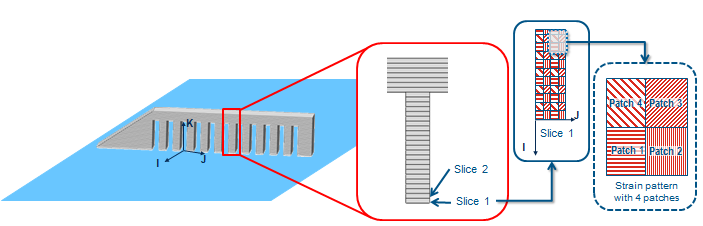
- Define a scan region in which the eigenstrain patterns are
applied.
A scan region is a rectangular cuboid whose sides align with the
build coordinate system. Define a set of one or more nonoverlapping scan
regions that completely enclose the additive manufacturing model. A single
eigenstrain pattern is assigned to each scan region.
Note:
An eigenstrain pattern can be assigned to multiple scan
regions, and every pattern can be rotated by a fixed angle for each successive
slice in the build direction.
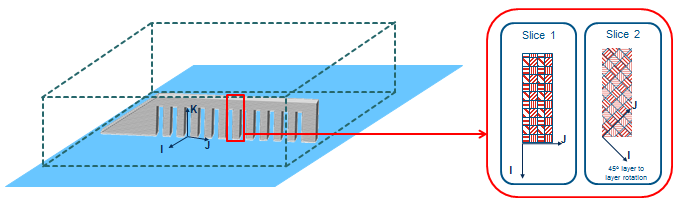
- Create
Structural Restraints & Loads.
- Simulate.
- Postprocess the
Results.