Discretized geometry
Finite elements and nodes define the basic geometry of the physical structure being modeled.
Each element in the model represents a discrete portion of the physical structure, which is, in turn, represented by many interconnected elements. Elements are connected to one another by shared nodes. The coordinates of the nodes and the connectivity of the elements—that is, which nodes belong to which elements—comprise the model geometry. The collection of all the elements and nodes in a model is called the mesh. Generally, the mesh is only an approximation of the actual geometry of the structure.
The element type and the overall number of elements used in the mesh affect the results obtained from a simulation. The greater the mesh density (that is, the greater the number of elements in the mesh), the more accurate the results. As the mesh density increases, the analysis results converge to a unique solution, and the computer time required for the analysis increases. The solution obtained from the numerical model is generally an approximation to the solution of the physical problem being simulated. The extent of the approximations made in the model's geometry, material behavior, boundary conditions, and loading determines how well the numerical simulation matches the physical problem.
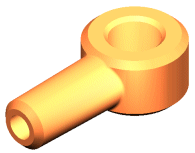
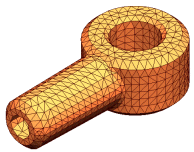