Three-dimensional continuum element library
Three-dimensional continuum elements can be hexahedra (bricks), wedges (triangular prism), or tetrahedra.
A library of solid elements also includes two-dimensional elements. The most commonly used two-dimensional continuum elements are as follows:
- Plane strain elements suitable for modeling thick structures (out-of-plane strain is zero); for example, a cross-section of a dam under water pressure.
- Plane stress elements suitable for modeling thin structures (out-of-plane stress is zero); for example, thin slabs with one dimension smaller than the other two.
- Axisymmetric elements suitable for analyzing structures with axisymmetric geometry subjected to axisymmetric loading; for example, an O-ring pressed into a groove by a top plate.
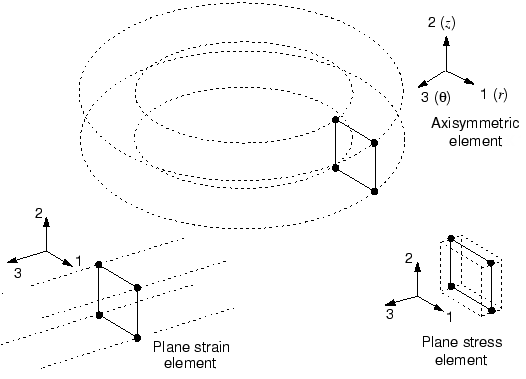