- True Stress and Strain
-
If the deformation of a bar in tension becomes significant, its cross-sectional area
will change. The traditional engineering definitions for stress and strain are no
longer accurate, and new measures, namely true stress and true strain, are introduced.
Alternative names for these quantities are Cauchy stress, logarithmic strain, and
natural strain.
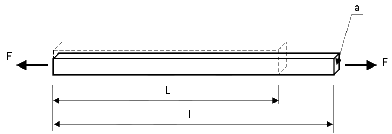
The true stress is
, where
is the final deformed cross-sectional area.
The true strain is
, where
is the final length and
is the initial undeformed length of the bar.
- Engineering Stress and Strain
-
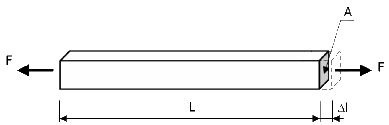
The engineering stress (or nominal stress) is
, where
is the initial undeformed cross-sectional area.
The engineering strain (or nominal strain) is
, where
is the change of the bar's length and
is the undeformed bar's lengh.
Stresses are related to the strains through constitutive laws, which are governed by material
properties. The simplest of the stress/strain laws is Hooke’s law, which is given by
.