The common information in both
Balance Turning and
Follow Turning operations is described below.
Copy of Data from Rough Turning Operation to Sibling
Operation
During creating
Balance and
Follow turning operations, data from
Strategy,
Geometry,
Feeds and Speeds,
and
Macros
tabs is copied from the master
Rough Turning operation to the
Sibling Operation.
Note:
For
Macros,
Copy-Transformations are applied before copying the data
If a
Sibling Operation is modified, then changes
are copied to the corresponding sibling
Machining Operationonly.
Global View in Synchronization Wizard
The
in synchronization column helps to recognize the
Balance and
Follow turning operations in the
synchronization Global View
.
Place the pointer over the
Synchronization column to display tooltips for
Balance and
Follow turning operations.
The
Synchronization editor is disabled and
synchronization position for both the
Machining Operations
is
Start-Start.
Deletion of Sibling Operations
If a
Sibling Operation is deleted, a warning
message appears to get confirmation. Deleting a
Sibling Operation breaks all the existing
links, remove synchronization, changes tool path status in
Activities Process tree,
and delete
Balance and
Follow turning operations associated with the
Sibling Operation. Deleting a
Sibling Operation does not delete the tool
under which it was created.
Apt Output
Define NC_Command (NC_BALANCING) in PP word table
*START_NC_COMMAND
NC_BALANCING
%MFG_BALANCING
*END
The APT output for
Balance turning operation is:
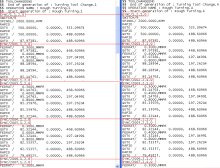
Define NC_Command (NC_FOLLOWTURNING) in PP word table
*START_NC_COMMAND
NC_FOLLOWTURNING
%MFG_ NC_FOLLOWTURNING
*END
The APT output for
Follow turning operation is:
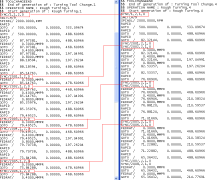
Copy-Paste and Cut-Paste of Machining Operation
For copy-paste, the new pasted
Machining Operation
does not have the
Balance and
Follow turning operation parameters of the
master
Rough Turning operation. Pasted
machining operation acts an individual
Machining Operation.
For cut-paste,
Balance and
Follow turning operations are managed. If a
Machining Operation
is pasted at some location and if new location is incompatible, then the
Machining Operation
gets deleted. You can retrieve the deleted
Machining Operation
by
Undo. If the location is compatible, then
Machining Operation
gets pasted successfully and links between the
Sibling Operation gets renewed.
See
Creating a Balance and Follow Turning Operationand
Creating and Editing Synchronization.