
Thread tab
- Tool Axis
The Tool Axis command in the Turning
Operations dialog box is represented by an arrow when
creating a part operation.

See Defining the Tool Axis
- Profile
- Specifies a thread profile.
You can specify:
- ISO
- Trapezoidal
- UNC
- Gas
- Other: The
Other allows defining a specific
thread profile.
- Orientation
- Specifies the type of machining according to the location of the area to
machine on the part.
You can specify:
- Location
- Specifies location.
You can specify:
- Front: The profile is machined toward
the head rough stock.
- Back: The profile is machined from
the head rough stock.
- Thread unit
- Specifies the thread unit.
This option is activated when the
Profile is specified as
Other. Thread unit
is automatically set to Threads per Inch for
the ISO, Trapezoidal
UNC, and Gas
types.
- Threads per Inch
- Specifies the threads per Inch.
This option is activated when the
Profile is set to
Other and Thread
unit is set to Threads per
Inch.
- Number of Threads
- When value is specified greater than 1, then this value allows you to
specify whether a multi-start thread is to be machined.
This option is
activated when the Profile is set to
Other and Thread
unit is set to Threads per
Inch.
- Nominal Diameter
- This value must be given when Thread type is
Internal and Profile
is Other.
- Thread Pitch
- This value must be given when the Thread type is
set to Pitch or the
Profile is ISO or
Trapezoidal.
- Thread Depth
- This value must be given when the Thread profile
is Other
Strategy Parameters
- Threading Type
- Choose the desired threading type.
You can specify:
- Constant depth of cut
- Constant section of cut
- Depth of cut
- Specifies the depth of cut.
This option is available only when
Threading Type is set to
Constant depth of cut.
- Number of passes
- Specifies the number of passes.
This option is available only when
Threading Type is set to
Constant section of cut. When the number
of passes is defined, the section of cut value is automatically
set.
- Thread Penetration
- Specifies thread penetration.
You can specify:
- Straight
- Oblique: Also specifies the
Penetration angle.
- Alternate: Also specifies the
Penetration angle.
This option is available only when Threading
Type is set to Constant depth of
cut
- First Passes
- Select First passes check box to manage
penetration on first passes.
This option is available when
Threading type is set to
Constant section of cut. When activated,
you must specify values for:
- Number of first passes
- First section rate.
- Last Passes
- Select Last passes check box to manage
penetration on the last passes.
This option is available when
Threading type is set to
Constant section of cut. When activated,
you must specify:
- Number of last passes
- Depth of cut for last passes.
- Spring Passes
- Select Spring passes check box to manage
penetration on the spring passes.
This option is available when
Threading type is set to
Constant section of cut. When activated,
you must specify Number of spring
passes
Options
- Clearance on crest diameter
- Specifies the clearance on crest diameter.
- Lead-in Distance
- Specifies the Lead-in Distance with respect to the
cutting direction.
The tool is in RAPID mode before this
distance.
- Lift-off Distance and Lift-off Angle
- Specifies the Lift-off Distance and
Lift-off Angle to define the lift-off vector at
the end of each pass with respect to the cutting direction.
The figure
below shows the effect of a positive lift-off angle for external
machining.
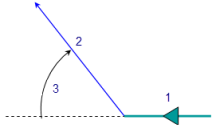
- Cutting direction
- Lift-off vector
- Positive lift-off angle
- Tool Compensation
- Select a tool
compensation number corresponding to the desired tool output
point.
The usable compensation numbers are defined on the tool assembly
linked to the machining operation. The output point corresponding
to type P9 is used, if you do not select a tool
compensation number.
- Change Output Point
- Select the Change Output Point check box to
automatically manage the change of output point.
Change Output
Point option is available for
Trapezoidal or Other
profile.
- Output Cycle Syntaxes
- Select the Output CYCLE syntax check box to generate CYCLE statements. You must also select the Output CYCLE syntax check box in the NC Output Generation dialog box, otherwise GOTO statements are generated.
For more information on the parameters available for PP word syntaxes for this type of operation, see PP Tables and Word Syntaxes - PP Word Tables.
- Editing CYCLE Syntaxes
- Select Edit Cycle
to display the Cycle Syntax
Edition dialog box. This dialog box displays:
- Unresolved syntax of the NC Instruction of the operation. This is the
syntax as specified in the PP table referenced by the current Generic Machine.
- Resolved syntax that is resolved either by geometric selection or user
entries.
- You can access all the CYCLE syntaxes contained in the current PP table by
clicking PP Instruction
. You
can then select the required syntax to be used. For more information, see Inserting Post-Processor Instructions.
-
Notes:
- Only one cycle syntax (delimited by keywords) is allowed for each PP
Instruction.
- Do not modify the syntax directly in the Current
Selection box of the PP Words
Selection dialog box, or in the Resolved
Syntax box of the Cycle Syntax
Edition dialog box. Otherwise, the syntax on the
machining operation is not updated with any modification you make to
the PP Table syntax. Instead, modify the syntax of the machining
operation by selecting a syntax from the Available
Syntaxes list of the PP Words
Selection dialog box.
Geometry
- Part profile
- Part profile is required. It is specified by selecting edges either
directly or after selecting the By Curve
context menu command.
See Selecting Edges and Faces to Define Geometry.
- Limit Mode
-
- Start Limit Mode: This option allows you
to specify a point, line, curve, or face as the start element of
the profile to be machined. If a face is specified, the start
element is the intersection of the face and the working plane.
The position of the start of machining is also defined with
respect to this element. In / On / Out
allows you to specify the Go-Go type positioning of the tool
with respect to the start element. The On
option is always used for a point type end element. If needed,
the profile may be extrapolated to the start element.
- End Limit Mode: This option allows you to
specify a point, line, curve, or face as the end element of the
profile to be machined. If a face is specified, the end element
is the intersection of the face and the working plane. The
position of the end of machining is also defined with respect to
this element. In / On / Out allows you to
specify the Go-Go type positioning of the tool with respect to
the end element. The On option is always
used for a point type end element. If needed, the profile may be
extrapolated to the end element
Note:
To avoid collisions of tool with limit geometry or unwanted
machining beyond limits with In option,
either define limits with suitable offset value or include limit
geometry as part element (this is better wherever applicable) and
avoid limit definition.
Relimiting the Area to Machine by means of Limit
Mode:
- If you specify a point, it is projected onto the part
profile. A line through the projected point parallel to the
radial axis delimits the area to machine.
- If you specify a line, its intersection with the part
profile is calculated (if necessary, the line is
extrapolated). A line through the intersection point
parallel to the radial axis delimits the area to
machine.
- If you specify a curve, its intersection with the part
profile is calculated (if necessary, the curve is
extrapolated using the tangent at the curve extremity). A
line through the intersection point parallel to the radial
axis delimits the area to machine.
- Start Limit offset
- Specifies the distance with respect to the start element (only if start
element is a line, curve or face, and when In or
Out is set for start element
positioning).
- End Limit Offset
- Specifies the distance with respect to the end element (only if end
element is a line, curve or face, and when In or
Out is set for end element positioning).
- Length
- This value must be given when the In / On / Out
is set for Start Limit offset and
None is set for End Limit
offset, and vice versa.
|