RTCP Mode
With RTCP mode activated, the tool tip remains stationary with respect to the workpiece whenever the tool orientation changes.
RTCP mode is available for the following machining operations: axial, circular milling, profile
contouring, pocketing, 4-axis pocketing, facing, and for 4-axes and 5-axes operations. We
recommend to use RTCP mode with both generic and imported machines with at least one rotary
axis. It is supported on machines that have maximum 5-axis defined. If your machine has more
than 5-axis, lock the extra axes.
When activated, RTCP mode applies to all the axes of the machine.
To use RTCP mode, you must activate it on the machine in session first. Note that 3-axes generic machine are not supported.
You can activate it RTCP mode on a machine by selecting the following check boxes:
- RTCP Support: when selected, specifies that the machine supports RTCP mode
- RTCP ON (Default Mode): when selected, activates RTCP mode on the machine.
These check boxes are available in the
Numerical Control tab of the
Machine dialog box that appears when you edit a machine. For more information, see
Creating a Generic Machine and Managing Its Parameters.
You can use the NC_RTCP_ON
and NC_RTCP_OFF
NC instructions to output the RTCP mode at the beginning of each manufacturing program.
You can deactivate RTCP mode locally on operations:
- Between Two Operations
- You can deactivate RTCP mode for transition paths by clearing the RTCP ON check box. This check box is available in the Feedrate and Spindle Speed tab of any operation dialog box compliant with RTCP mode. This option is deactivated if RTCP mode is deactivated on the machine associated with the operation.
When RTCP mode is deactivated on transition paths, specific NC instructions are generated in the APT file:
NC_RTCP_OFF
is generated before the first point of the current machining operation.NC_RTCP_ON
is generated after the first point of the current machining operation.
- For One Operation
- You can deactivate RTCP mode for linking motions within one operation by right-clicking the clearance motion in the Macro Parameters tab of any operation dialog box compliant with RTCP mode. This option is deactivated if RTCP mode is deactivated on the machine associated with the operation.
When RTCP mode is deactivated, dotted lines appear along tool path motions on the workpiece to indicate that linking motions are not the ones taken into account during simulation.
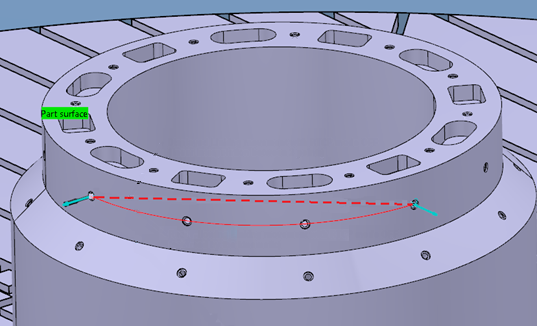
To display linking motions with RTCP mode deactivated, use Machining Validation app.
When RTCP mode is deactivated on linking motions within one operation, specific NC instructions are generated in the APT file:
NC_RTCP_OFF
is generated at the beginning of the linking motions.NC_RTCP_ON
is generated at the end of the linking motions.
For axial operations, you must define linking approach and retract motions between two consecutive holes, to generate NC instructions specific to RTCP mode.
Polar Mode
With polar mode activated, you can specify the axes to use during the machining. You can either machine a part using all linear axes and the machine head axes, or specific linear axes and the table axes.
Polar mode is available for the following machining operations:
axial, circular milling, profile contouring, pocketing, 4-axis
pocketing and facing.
The machine simulation, APT output and post-process are automatically updated with the polar mode parameters defined.
Here is an example of the typical PP Words generated when polar mode is activated: POLAR / ON, C, X, LINEAR, 100, Y1, MINUS
.
PP Word | Axis |
---|
C | Rotary axis |
X | Locked linear axis |
100 | Offset defined on the locked linear axis |
Y1 | Moving axis |
Minus | Initial position on the moving axis. |