-
Right-click the general operation in the tree and select .
The Define Position dialog box appears.
-
Select the palette resource.
The image below shows how the two holes on the base of the engine assembly are
to be positioned on the two locating pins.
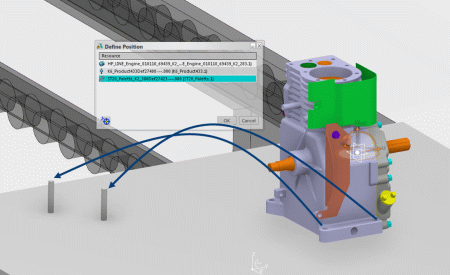
-
Use the Robot to move the engine assembly vertically above the palette, so that it is
at a level above the top of the locating pins.
-
In the Define Position dialog box, click Cumulative
Snap.
The
Cumulative Snap dialog box appears. It comprises:
- A list of options for specifying the type of geometry to use in the snap
- Two commands for inverting the snap direction by a 180 degree rotation of the U-axis
or V-axis.
-
Select Arc center from the drop-down menu, and select the first
hole on the base of the engine.
-
Select Line only from the drop-down menu, and select a locating
pin on the palette.
-
Use the Robot to move the engine so that the center of the hole and the axis of the
locating pin are aligned.
The first constraint is defined.
- Select Arc center from the drop-down menu, then select the second hole on the base of the engine.
-
Select Line only from the drop-down menu, and select the other
locating pin on the palette.
-
Use the Robot to move the engine so that the center of the second hole and axis of the
second locating pin are aligned.
The second constraint is defined. The first constraint is also
respected.
Note:
The holes are aligned with the locating pins, but the engine is not yet
lying on palette.
- Select Plane only from the drop-down menu, then select the base of the engine.
-
Use the Robot to move the engine so that it lies on the palette, and is positioned
using the locating pins.
The third constraint is defined. The second and third constraints are also respected.
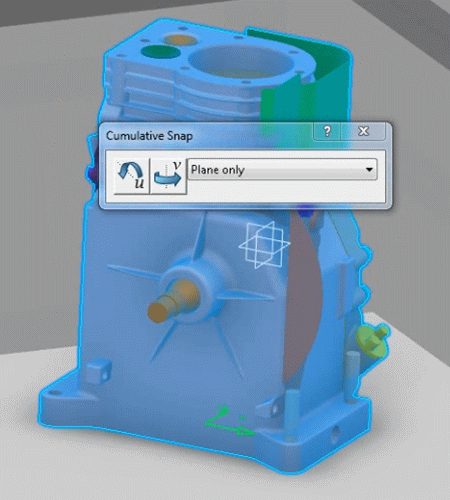
-
Close the Cumulative Snap dialog box. In the Define
Position dialog box, click OK to define the new
operation position.