Frictional effects
Problem description
In this series of tests the free rolling angular velocity, , of a circular disk in contact with a flat rigid surface is calculated for different disk geometries, contact pressures, friction coefficients, material models, and element types. The ground velocity is specified as either a straight-line translational velocity of = 2.0 or as a cornering angular velocity of = 0.02. By specifying a large cornering radius, = 100.0, straight line rolling with velocity = 2.0 is recovered. The results obtained with Abaqus are compared to numerical results published by Faria (1989).
The model consists of a ring with outer radius = 2.0 and variable inner radius . Three different geometries ( = 0.2, 1.0, 1.7) are considered. The model is fully fixed on the inside, and plane strain boundary conditions are imposed along the axial direction.
Two material models are considered: a linear elastic material with E = 800.0 and = 0.3 and an incompressible hyperelastic material with = 80.0 and = 20.0. The friction coefficients considered are = 0.02 and = 0.2. The first analysis step is a static analysis where the rigid surface is displaced a distance = 0.05 or = 0.1 to establish a contact pressure. The friction coefficient during this step is held constant at zero. This step is followed by a steady-state transport analysis where the ground traveling velocity and spinning angular velocity are applied and the friction coefficient is ramped to its final value.
The problem is discretized with different types of three-dimensional elements. The models that are discretized with first-order elements use 34 element divisions along the circumference and 5 element divisions in the radial direction. The second-order and cylindrical element models use 18 elements along the circumference and 3 elements in the radial direction. All the models are discretized with one element in the axial direction. A first-order finite element mesh for the case = 1.0 is shown in Figure 1.
Results and discussion
Additional frictional tests
Additional verification tests are performed to verify contact between a spinning deformable body and a spinning rigid body. In all these tests the deformable body uses the properties and discretization described earlier. The rotating rigid body is in contact either with the inside surface of the deformable body (such as in the case where a tire is mounted on a rigid rim) or with the outside surface of the deformable body (such as in the case where a tire is in contact with a rotating drum). No reference solutions are available for the case where the rigid body is in contact with the inside surface of the deformable body. By specifying a large radius for the rigid body in the case where a rigid spinning drum is in contact with the outside surface of the deformable body, straight line rolling is recovered. We selected a rigid body radius of = 1000.0 and an angular velocity of = 0.002, which corresponds to straight line rolling with a velocity = 2.0.
Another verification test is performed to verify contact between a rolling gear-like thick cylinder with an outer radius of 8.5 and a flat rigid surface. The model is generated by revolving a single three-dimensional 15° sector about the symmetry axis. The gear-like cylinder travels at a ground velocity of 2.7778 with an angular velocity varying from 0.2 to 0.5. The results are compared to those obtained from a transient Lagrangian analysis.
Input files
- pstca4shhfa.inp
-
Axisymmetric model using CAX4H elements and a hyperelastic material.
- pstc38shhfs.inp
-
C3D8H elements, hyperelastic material, = 1.0, = 0.1, = 0.02, straight line rolling with = 2.0 (requires two-dimensional input file pstca4shhfa.inp).
- pstca4syhfa.inp
-
Axisymmetric model using CAX4RH elements and a hyperelastic material.
- pstc38syhfs.inp
-
C3D8RH elements, hyperelastic material, = 1.0, = 0.05, = 0.2, straight line rolling with = 2.0 (requires two-dimensional input file pstca4syhfa.inp).
- pstca8sfefa.inp
-
Axisymmetric model using CAX8H elements and an elastic material.
- pstc3ksfefs.inp
-
C3D20 elements, elastic material, = 0.2, = 0.10, = 0.02, straight line rolling with = 2.0 (requires two-dimensional input file pstca8sfefa.inp).
- pstca8srefa.inp
-
Axisymmetric model using CAX8R elements and an elastic material.
- pstc3ksrefs.inp
-
C3D20R elements, elastic material, = 1.7, = 0.05, = 0.02, straight line rolling with = 2.0 (requires two-dimensional input file pstca8srefa.inp).
- pstca4siefa.inp
-
Axisymmetric model using CAX4I elements and an elastic material.
- pstc38siefc.inp
-
C3D8I elements, elastic material, = 10.2, = 0.05, = 0.02, cornering with = 0.02 and = 100.0 (requires two-dimensional input file pstca4siefa.inp).
- pstca3shhfa.inp
-
Axisymmetric model using CAX3H elements and a hyperelastic material.
- pstc36shhfc.inp
-
C3D6H elements, hyperelastic material, = 1.0, = 0.10, = 0.02, cornering with = 0.02 and = 100.0 (requires two-dimensional input file pstca3shhfa.inp).
- pstc38shhfd.inp
-
Contact between a rigid drum and the outside surface of a deformable body, C3D8H elements; similar to pstc38shhfs.inp (requires two-dimensional input file pstca4shhfa.inp).
- pstc38syhfd.inp
-
Contact between a rigid drum and the outside surface of a deformable body, C3D8RH elements; similar to pstc38syhfs.inp (requires two-dimensional input file pstca4syhfa.inp).
- pstca3shhfr.inp
-
Axisymmetric model using CAX3H elements and a hyperelastic material.
- pstc36shhfr.inp
-
Contact between a rigid “rim” and the inside surface of a deformable body and contact between a flat rigid foundation and the outside surface of a deformable body, C3D6H elements; similar to pstc36shhfc.inp (requires two-dimensional input file pstca3shhfr.inp).
- pstcc12shhfs.inp
-
CCL12H elements, hyperelastic material, = 1.0, = 0.1, = 0.02, straight line rolling with = 2.0 (requires two-dimensional input file pstca4shhfa.inp).
- sstransp_per_hyper_preload.inp
-
3D sector model using C3D8H elements and a hyperelastic material with viscosity. Preloaded with an internal pressure.
- sstransp_per_hyper_rolling.inp
-
Contact between a flat rigid surface and a gear-like deformable cylinder (requires three-dimensional input file sstransp_per_hyper_preload.inp).
References
- Tire Modeling by Finite Elements, Ph.D. dissertation, The University of Texas at Austin, 1989.
Tables
Input file | Reference solution | Abaqus | % Difference |
---|---|---|---|
pstc38shhfs.inp | 0.95009 | 0.94635 | 0.39 |
pstc38syhfs.inp | 0.98006 | 0.98213 | 0.21 |
pstc3ksfefs.inp | 1.02970 | 1.02726 | 0.24 |
pstc3ksrefs.inp | 1.00297 | 1.00283 | 0.01 |
pstc38siefc.inp | 1.02180 | 1.00674 | 1.47 |
pstc36shhfc.inp | 0.95195 | 0.94568 | 0.66 |
Material type | Reference solution | Abaqus | % Difference | |||
---|---|---|---|---|---|---|
Hyperelastic | 0.05 | 0.2 | 0.02 | 0.99349 | 0.99219 | 0.13 |
1.0 | 0.02 | 0.97977 | 0.98053 | 0.08 | ||
1.7 | 0.02 | 0.87183 | 0.84974 | 2.53 | ||
1.0 | 0.20 | 0.98066 | 0.98212 | 0.15 | ||
0.10 | 0.2 | 0.02 | 0.98558 | 0.98422 | 0.14 | |
1.0 | 0.02 | 0.95009 | 0.95059 | 0.05 | ||
1.7 | 0.02 | 0.73057 | 0.65790 | 9.95 | ||
1.0 | 0.20 | 0.95195 | 0.95100 | 0.10 | ||
Linear elastic | 0.05 | 0.2 | 0.02 | 1.02180 | 1.02332 | 0.15 |
1.0 | 0.02 | 1.02415 | 1.02574 | 0.16 | ||
1.7 | 0.02 | 1.00297 | 1.00263 | 0.03 | ||
0.10 | 0.2 | 0.02 | 1.02970 | 1.03410 | 0.43 | |
1.0 | 0.02 | 1.02810 | 1.02872 | 0.06 | ||
1.7 | 0.02 | 0.99156 | 0.99542 | 0.39 |
Figures
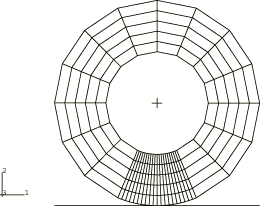