Anisotropic Yield
Anisotropic yield can now be used with the extended Drucker-Prager and
crushable foam plasticity models.
Anisotropic yield is used for materials that exhibit different yield behavior
in different directions, mostly for composite materials. You can now use anisotropic
yield with the extended Drucker-Prager plasticity model for pressure-dependent yield or
with the crushable foam plasticity model for energy absorption structures. Previously,
you could use anisotropic yield only with metal plasticity and critical state (clay)
plasticity.
Benefits: This feature extends the material modeling capabilities in Abaqus.
For more information, see
Hill Anisotropic Yield/Creep
Multiscale Material Modeling in Abaqus/Explicit
Multiscale material modeling is now available in Abaqus/Explicit.
You can now use mean-field homogenization to model composite materials in Abaqus/Explicit. Previously, this material model was available only in Abaqus/Standard. The mean-field homogenization approach is used for multiscale material modeling.
This approach can calculate composite responses using properties of the constituents; it
can also decompose the composite strain into constituent strains and compute the
constituent-level responses. The mean-field homogenization approach can be useful to
predict behaviors of fiber-reinforced composite assembly parts manufactured through the
injection molding process; it can also be useful to model progressive failure of
fiber-reinforced composites by modeling failure at the constituent level.In the
example below, the fiber orientation is predicted by an injection molding simulation,
as shown in the first figure. The model is then reduced to a simple cylinder, and a
rigid rod is added to the model to simulate a service load, as shown in the second
figure. The fiber orientation tensor field is mapped from the injection molded part to
the reduced model, as shown in second figure.
There is a "weld line" in the
cylinder caused by the gate location in the injection molding process; the weld line
is the line where the flow fronts meet during the molding process and can result in
weakness of the structure. The structural analysis is carried out with Abaqus/Explicit, and a multiscale material is used to model the plastic part. Plasticity with
ductile damage is specified in the matrix material, and damage evolution is also
specified. The third figure shows the deformed shape of the cylinder. As expected, the
failure location agrees very well with the location of the weld line.
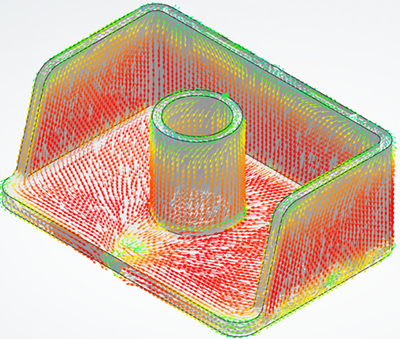
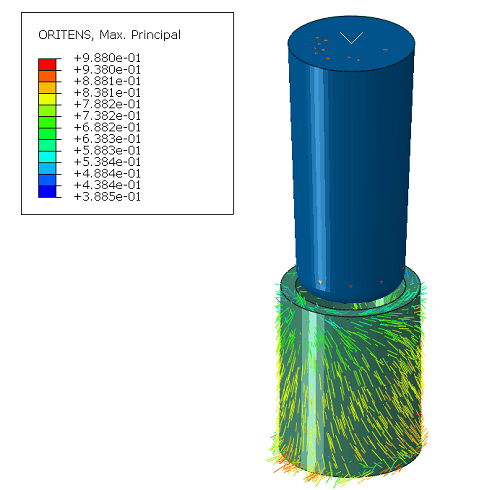
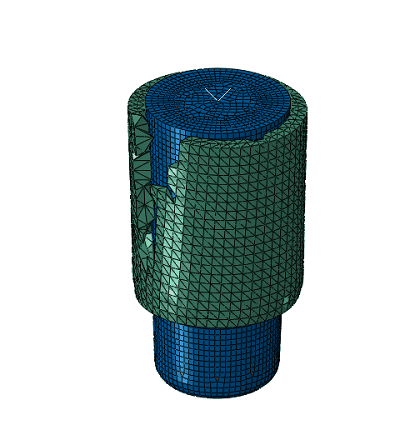
Benefits: This feature extends the multiscale material modeling capabilities in Abaqus.
For more information, see
Mean-Field Homogenization
Plasticity Corrections
You can now use Neuber and Glinka plasticity corrections to estimate the
effects of plasticity in a model analyzed with purely elastic material.
Plasticity corrections provide an efficient method to evaluate the extent of
plasticity in a structure based on a purely linear elastic solution. Two types of
plasticity correction are now available in Abaqus: Neuber and Glinka. Both methods apply a correction to the elastic results to
capture the effects of local plasticity. The accuracy of the solution is generally
quite good when the loading conditions lead to plastic deformation localized in small
regions, such as in typical durability load cases. However, a full nonlinear analysis
is recommended for loading conditions that lead to extended plastic deformation of the
structure. In addition to the general static procedure, the Neuber and Glinka
plasticity corrections are supported with the static linear perturbation procedure
with multiple load cases, which can further substantially decrease the analysis
time.
To illustrate the application of the method, consider a Body-in-White
(BIW) model of a car subjected to the boundary conditions and loads shown in the first
figure (courtesy of the Public Finite Element Model Archive of the National Crash
Analysis Center at George Washington University). The stresses and plastic strains in
the car body component highlighted in the figure are estimated using the Neuber and
Glinka rules with a linear elastic analysis. The results are compared with those
obtained from a full nonlinear elastic-plastic analysis. The stress and plastic strain
results are presented in the second and third figures, respectively. The predictions
based on plasticity corrections show good agreement with those obtained using a full
elastic-plastic analysis, which is expected because plastic deformation is highly
localized in small areas of the part. The Neuber's rule overestimates the equivalent
stress and plastic strain, which is usually the case. As expected, the Glinka
equivalent stress and plastic strain are lower than Neuber’s values. In this case,
Glinka's rule slightly underestimates the elastic-plastic results.
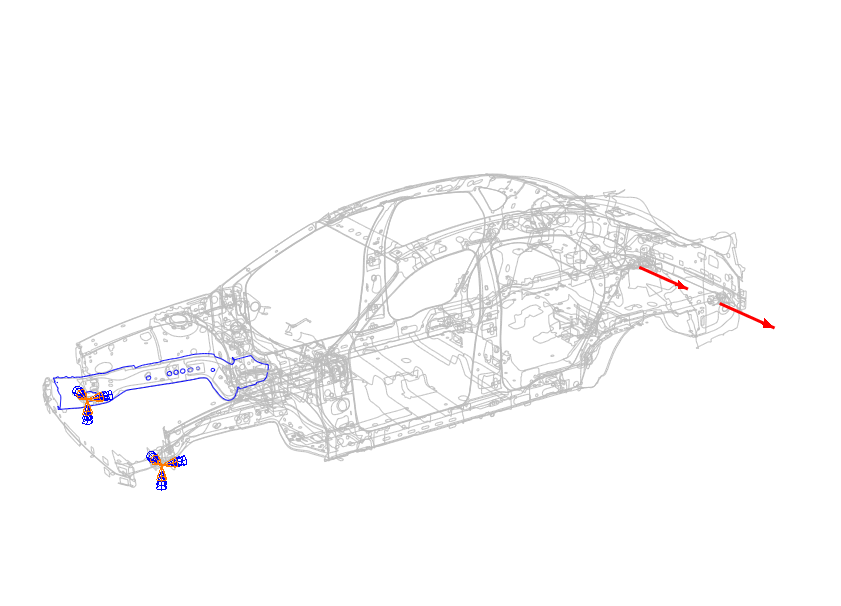
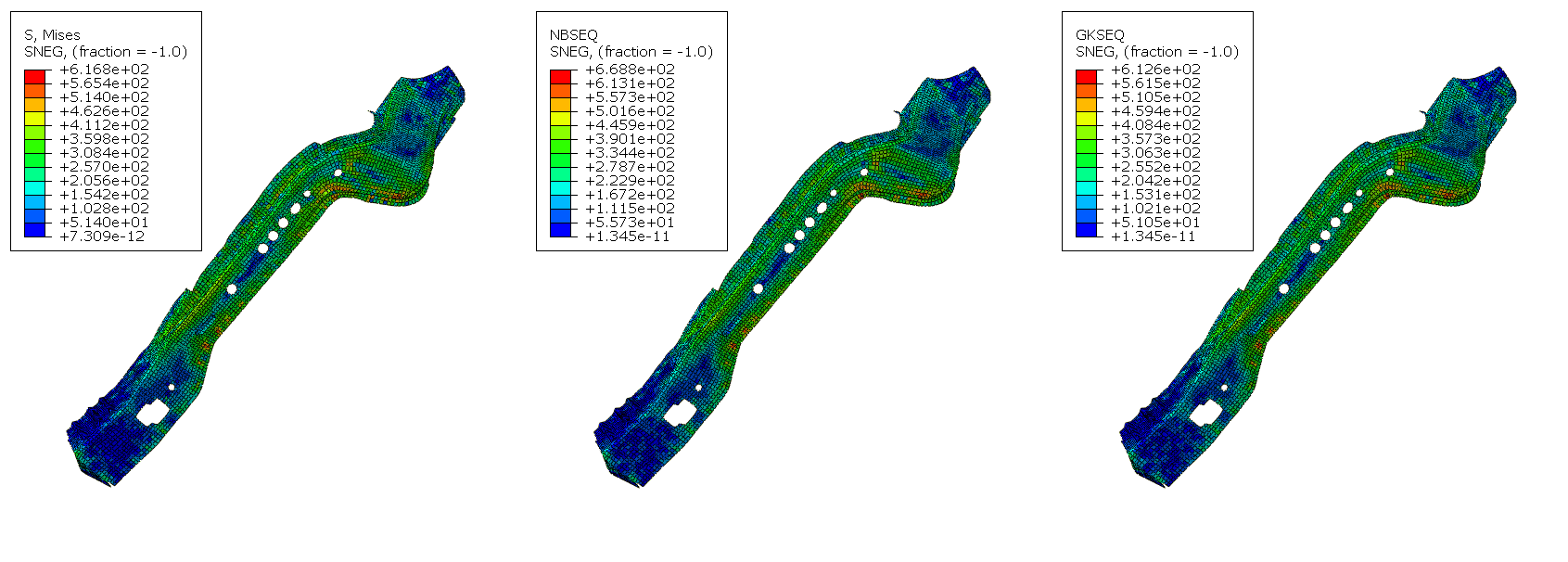
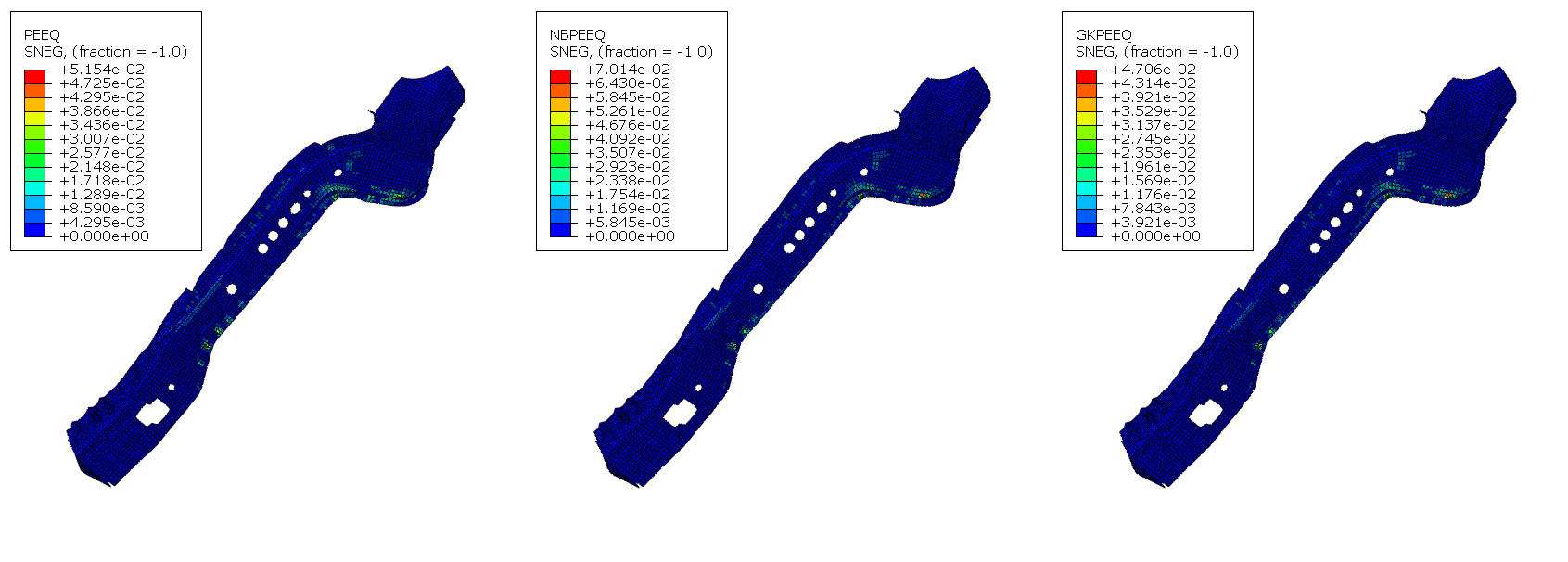
Benefits: This method provides a substantial computational cost reduction compared to a
full nonlinear elastic-plastic analysis, which is particularly valuable in optimization
studies during the early design phase of a product or for concept design
workflows.
For more information, see
Plasticity Corrections
Valanis-Landel Hyperelastic Model
You can now define the volumetric response of the Valanis-Landel hyperelastic
model by providing volumetric test data.
The Valanis-Landel model is an isotropic hyperelastic model in which the
strain energy function is determined numerically from test data that you specify. The
model can reproduce both compressive and tensile test data exactly. Previously, you
could define the volumetric response of the model either by specifying a constant value
of the Poisson’s ratio or by providing lateral strain information from a uniaxial
test.In the example below, the Valanis-Landel material is used to model the rubber
sealing in the boot seal assembly shown in the first figure. The shaft is modeled as a
rigid body, and contact is specified between the shaft and the inner surface of the
seal. The shaft is first rotated 20° about the axis perpendicular to the shaft, and
then the angulated shaft moves around the entire circumference. Two analyses were
performed with the same Valanis-Landel material defined using two different
methods.
In the first case, the material was defined by providing uniaxial test
data with lateral strains shown in the second figure. In the second case, an
equivalent material definition using uniaxial test data without lateral strains
(dashed line in the second figure) and the volumetric test data (third figure) was
used. As expected, the stress results are identical in both cases because the same
material response was specified using two different methods. The stress distribution
in the seal at the end of the analysis is shown in the fourth figure.

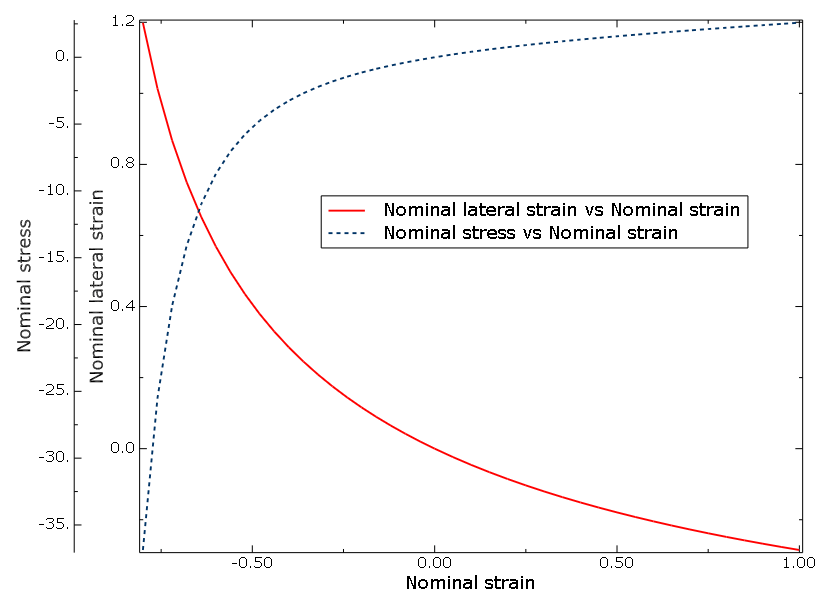
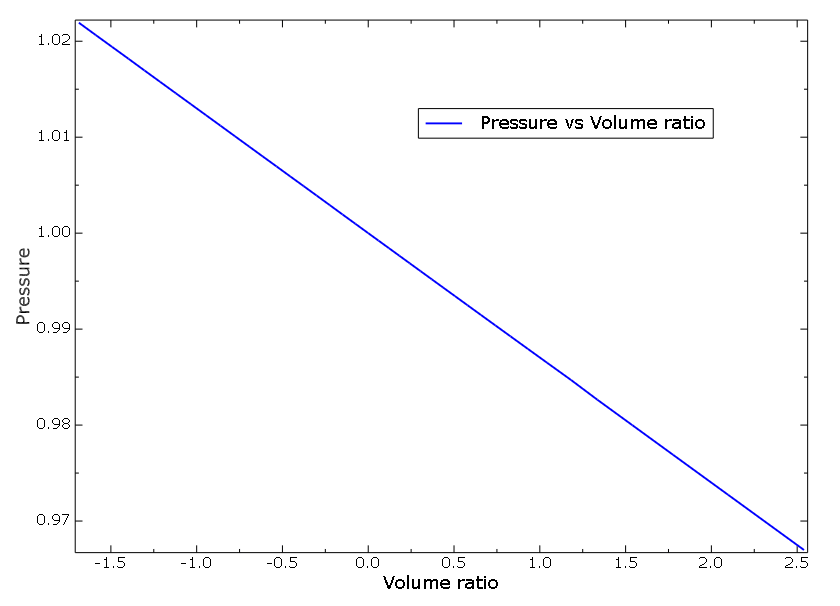
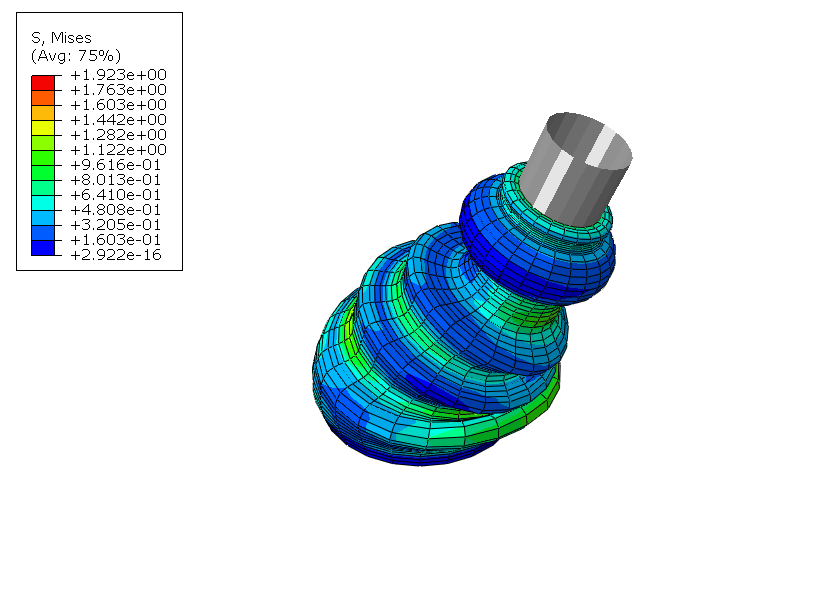
Benefits: This enhancement allows you to optionally specify volumetric test data to
calibrate the volumetric response of the model. This is convenient in cases when
volumetric test data and uniaxial test data without lateral strains are
available.
For more information, see
Hyperelastic Behavior of Rubberlike Materials
No Compression and No Tension Elasticity Models in Abaqus/Explicit
The no compression and no tension models for linear elasticity are now
available in Abaqus/Explicit.
The no compression and no tension models are intended to model linear elastic
structures where compressive or tensile principal stresses should not be generated.
Examples include cables and membrane structures with no compression stiffness. You can
now use these models in Abaqus/Explicit. Previously, they were available only in Abaqus/Standard.
Benefits: The availability of the no compression and no tension models in Abaqus/Explicit expands the Abaqus materal modeling capabilities.
For more information, see
No Compression or No Tension