-
From the Weld section of the action bar, click User Weld
.
-
Select a weld body or a bundle of welds in the
tree.
-
Select the faces as supports.
Note:
To control the faces you need:
- To add or remove faces defining the supports (as
displayed in the
Supports list),
press
Ctrl + Click.
- You can add to or remove faces from a support using
the
Edit selection
context menu
from the
Supports list.
- Clicking a face in the
work area
adds it to the list.
- To remove a face from the list, use
Remove
selection.
- Click Weld Seam and select the shape defining the seam. In our example, the shape is a triangle.
- Optional: Select the preparation you want to use.
Note:
The shape of the preparation can be longer than the weld.
- Optional: To trim the weld to a surface or another weld, select the limits.
-
Click
Preview to show the user weld wireframe.
- Optional: Specify a weld symbol, a weld size and a weld length in Drafting Parameters. This information can be retrieved when extracting weld annotations for a drawing.
-
Optional: To define the shape of the weld, click the
Manufacturing tab and select an option. The shape
defines the weld seam shape representation in drafting context. If you select
Convex
or
Concave
, specify a curvature value in
Offset.
The offset is the maximum distance between the weld
face and arc.
For more information about manufacturing options,
see
Manufacturing.
Note:
Shapes are extracted on drawings.
- Optional: To define the shape of the weld, click the
Manufacturing tab and select an option. If you
select
Convex
or
Concave
, enter a curvature value in
Offset. The offset is the maximum distance between
the weld face and the arc.Notes:
- The shape is retrieved on drawings.
- If you generate a V-butt or a bevel-butt weld and select Broad Root Face, the welding symbols extracted on a drawing are
and .
For more information about manufacturing options, see
Manufacturing. -
Optional: Select
Generate Weld Impacts.
The app performs a Boolean subtract of the weld shape from the
plates being welded.
-
Click
OK.
The user weld is created but affected representations are
not prepared for the welding.
- Click
Update
.
The affected representations are now prepared for the welding.
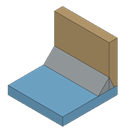 The user weld appears in the tree.
- Its supports and their external references appear under the
user weld.
- External references appear under the
External References node too.
- The weld preparation appears as
Assembly features
.
- The body containing information about the weld seam and the weld preparation appear in No Show status.
- An assembly protected weld preparation is created and appears under the
Assembly features
node.
- The welded 3D shapes are prepared.
|