
General Parameters
- Tool
Axis
The Tool Axis command in the Turning
Operations dialog box is represented by an arrow when
creating a part operation.

See Defining the Tool Axis
- Orientation
-
Specifies the
orientation of the groove to be machined as:
- Internal
- External
- Frontal
- Other: Specifies the
Angle of Incline, for an
Other orientation.
- Machining Direction
- Specifies the machining direction as:
- To head rough stock or From
head rough stock for
Internal orientation.
- To head rough stock or From
head rough stockInternal
for External orientation.
- To Spindle or From
Spindle for Frontal
orientation.
- Right of Groove or Left of
Groove for Other
orientation.
Note:
If start and end limit mode defined in
Geometry tab are in conflict with the
machining direction, then these is reversed
automatically.
- Contouring for Outside Corners
-
Specifies the contouring of corners as:
Note:
The geometry part profile is respected in this
case.
- Under Spindle Axis Machining
- This option allows you to request machining under the spindle
axis.
Note:
This option is activated when orientation is in
Frontal mode.
- CUTCOM
- Specifies cutter
compensation so that the NC output
includes CUTCOM instructions in approach and retract paths for cutter
compensation. You can specify:
- On: CUTCOM/RIGHT instruction
generated if tool is to the right of the tool
path and CUTCOM/LEFT if tool is to the left of
the tool path.
- Reverse: CUTCOM/RIGHT instruction
generated if tool is to the left of the tool path and
CUTCOM/LEFT if tool is to the right of the tool path.
See Cutter Compensation with Finish Turning Operations.
- Tool Compensation
- Select a tool
compensation number corresponding to the required tool
output point.
The usable compensation numbers are defined on the tool
assembly linked to the machining operation.
By default, the
output point corresponding to type P9 is
used, if you do not select a tool compensation number.
- Change Output Point
- Select the Change Output Point check box to
automatically manage the change of output point. .
The two selections:
None: If the
output point is consistent with the flank of the groove to be machined,
the output point is changed when the other flank of the groove is
machined. At the end of the Machining Operation, the output point is the same as it
was at the start of the Machining Operation. See Tool Output Point Change.
- Profile Output On Part
-
This computes a tool path is the result of Part Geometry and tooltip
Coordinates. When Profile Output on Part
option is selected, the tool path replay displays both tool paths.
For example, tool path with respect to tool (p9) compensation point
(orange color) and tool path related to profile output on part
(white color).
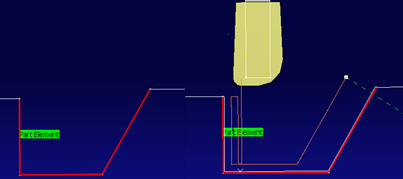
Note:
Profile Output on Part has a
specific APT generation with clear start and end marks. Groove
finishing MO tool paths haves the corresponding CUTCOM call with
proper end statements.
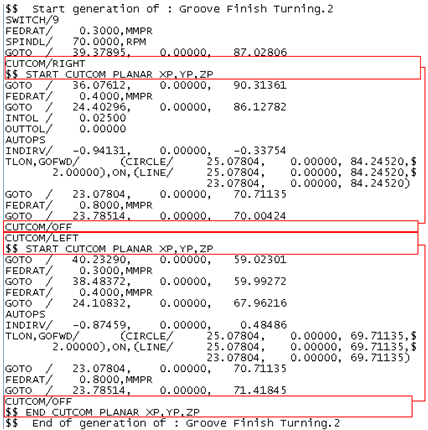
Most of the standard CNC machine controls have a feature that
enables the CNC programmer to apply an offset command to compensate the
cutter nose radius. Here the part is programmed by its contour as
per drawing dimensions and the control system does the required
calculations and adjustments automatically. The figures below shows
how the controller behaves with and without CUTCOM.
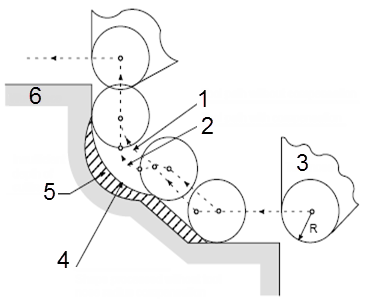
- Tool path without compensation
- Tool path with compensation
- Tool Nose
- Shape processed without tool nose radius compensation
- Insufficient depth of cutting
- Workpiece
Without tool nose radius compensation, the imaginary tool nose path
is the same as the programed path.
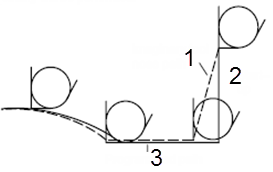
- Imaginary tool nose path
- Start-up
- Programmed path
Without tool nose radius compensation, the imaginary tool nose path
is the same as the programmed path.
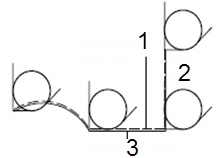
- Imaginary tool nose path
- Start-up
- Programmed path
Here a Part programmed is nothing but valid tool path with respect to Profile output
on part. This allows you to control the pertinence of the tool path position related
to the part profile geometry using the CNC machine controller and CUTCOM option. It
is a convenient way to have a clear visualization of the tool path.
With a Material Removal/Machine Simulation: Only the cutter center tool path is
taken in to account during tool path replay. Tool path replay is not based on the
tool path related to profile output on part.
Limitations: The
controller has to take care moving from one CUTCOM to another, as this alters the
CUTCOM side, and there is no change from existing behavior. Only
the cutter center tool path is taken into account and simulation is done based on
this.
Machining Parameters
- Insert-holder constraints
- Specifies insert-holder constraints as:
The following attributes (located on the Insert-holder's
Technology tab) may influence machining: See
Creating and Editing Milling, Drilling, and Probing Tools
- Gouging angle
- Trailing angle
- Leading angle
- Maximum recessing depth
- Maximum cutting depth
- Maximum boring depth
These attributes take tooling accessibility into account and may reduce
the machined area.
Note:
Use the Insert-Holder
Constraints option to either ignore or apply these
attributes. You can replay the Machining Operation to verify the influence of these attributes on the generated tool
path.
- First flank lead-in
- Defines the type of
lead-in at lead-in feedrate on the first flank of the
groove.
You can specify:
- Linear: Lead-in up to the point where
first flank machining starts is defined by the first
lead-in distance and first lead-in
angle parameters.
- Circular: Lead-in is circular and tangent
to the point where first flank machining starts. It is defined
by the first lead-in radius and
first lead-in angle parameters.
The first lead-in angle is defined with respect to the normal to the
cutting direction. The figure below shows the effect of a positive first
lead-in angle for external machining (1 - First lead-in vector, 2 -
Positive first lead-in angle, 3 - Cutting direction).
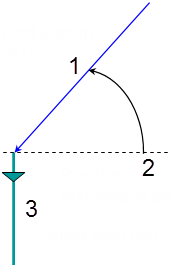
- Last flank lead-in
- Defines the type of lead-in at lead-in feedrate on the last flank of the
groove.
You can specify:
- Linear: Lead-in up to the point where
last flank machining starts is defined by the last
lead-in distance and last lead-in
angle parameters.
- Circular: Lead-in is circular and tangent
to the point where last flank machining starts. It is defined by
the last lead-in radius and
last lead-in angle parameters.
The last lead-in angle is defined with respect to the normal to the
cutting direction. The figure below shows the effect of a positive last
lead-in angle for external machining(1 - Last lead-in vector, 2 -
Positive last lead-in angle, 3 - Cutting direction).
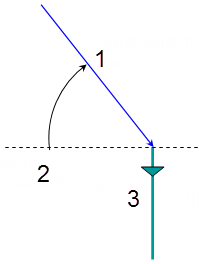
- Other Flank Lead-in
- Defines the type of lead-in required to machine flanks other than the first
and last flanks, for a groove that has multiple recesses. You can specify:
- Lift-off Type
- Defines the type of lift-off from the groove at lift-off feedrate.
You
can specify:
- Lift-off Distance: When lift-off type is
Linear.
- Lift-off Angle: When lift-off type is
Linear or
Circular.
- Lift-off Radius: When lift-off type is
Circular.
The lift-off angle is defined with respect to the normal to the cutting
direction. The figure below shows the effect of a positive lift-off
angle for external machining(1 - Lift-off vector, 2 - Positive lift-off
angle, 3 - Cutting direction).
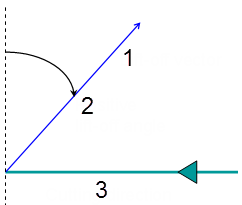
- Other Flank Lead-in Distance
- Specifies other flanks of the groove when other flank lead-in type is
Linear.
- Other Flank Lead-in Angle
- Specifies other flanks of the groove when other flank lead-in type is
Linear or
Circular.
Note:
The Other Flank Lead-in
Angle is defined with respect to the cutting
direction.
- Other Flank Lead-in Radius
- Specifies other flanks of the groove when other flank lead-in type is
Circular.
Note:
The Other Flank Lead-in Radius is defined
with respect to the cutting direction.
- Machining Tolerance
- Specifies the maximum allowed distance between the theoretical and computed
tool path.
- Clearance (1)
- This value defines the clearance to be applied to the next flank after the
first machined flank. The bottom of the groove (2) is machined up to the
position defined by this clearance value.
Note:
For machining operations with Orientation specified as
Other, the clearance value is not applied
for grooves with an inclined groove bottom.
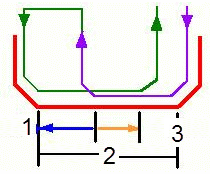
- Overlap (3)
- This value defines the amount of machining overlap at the bottom of the groove.
Note:
The sum of the Clearance and the
Overlap must be less than or equal to the
groove bottom width. Otherwise a warning message is issued. The
groove bottom width is the horizontal bottom of the groove, or the
length of the bottom element of the groove where there is no
vertical component. For a circular groove, the groove bottom width
is zero.
Corner Processing Parameters
- Entry, Exit, and Other corners
- Entry Corner means the first corner on the part
profile in the specified machining direction. Exit
Corner means the last corner on the part profile in the
specified machining direction. Corner processing is proposed for
Entry, Exit , and
Other corners. . The
Entry/Exit corners are determined according to
the specified machining direction and not by the tool motion.
You can specify:
- None: No corners are to be machined along
the profile.
- Chamfer: Only 90 degree corners of the
profile are chamfered.
- Rounded: All corners of the profile are
rounded.
The following options availability depends on the following conditions:
- Chamfer Length: If Other
corner processing mode is
Chamfer.
- Corner Radius: If Other
corner processing mode is
Rounded.
- Entry Corner Chamfer Length: On first
flank of groove when Entry corner
processing mode is Chamfer.
- Entry Corner Radius: On first flank of
groove when Entry corner processing mode
is Corner.
- Entry Corner Angle: On first flank of
groove when Entry corner processing mode
is Corner.
- Exit Corner Chamfer Length: On last flank
of groove when Exit cornerprocessing mode
is Chamfer.
- Exit Corner Radius: On last flank of
groove when Exit corner processing mode
is Corner.
- Exit Corner Angle: On last flank of
groove when Exit corner processing mode
is Corner.