
General Parameters
The Tool Axis command in the
Turning Operations dialog box is represented by an arrow
when creating a part operation.

See Defining the Tool Axis.
- General tab
-
Set the general specifications for the scenario.
- Orientation
- Specifies the type of machining according to the location of the
area to machine on the part.
You can specify:
- Internal
- External
- Frontal
- Location
- Specifies location as:
- Front: The profile is machined
toward the head rough stock.
- Back : The profile is machined
from the head rough stock.
- Machining Direction
- Specifies the machining direction with respect to the spindle
axis. This option is only available for
frontal orientation. You can specify:
Note:
If start and end limit mode defined in
Geometry tab are in conflict with
the machining direction, then these is reversed
automatically.
- Contouring for Outside Corners
- Specifies contouring of corners as:
The part profile is respected in this case.
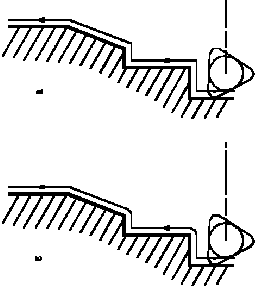
- Recess Machining
- Select this check box for a recess machining path after the
profile finish path.
Note:
An asymmetric groove tool
insert whose nose radius (left or right) is greater than
half its width allows complete machining.
- Under Spindle Axis Machining
- Select this check box to request machining under the spindle
axis. This option is available for the
Frontal orientation.
- CUTCOM
- Specifies
cutter compensation so that the NC
output includes CUTCOM instructions in approach and retract paths for cutter
compensation.
You can specify:
-
None
- On : CUTCOM/RIGHT
instruction generated if tool is to the right of the
tool path and CUTCOM/LEFT if tool is to
the left of the tool path.
- Reverse: CUTCOM/RIGHT
instruction generated if tool is to the left of the
tool path and CUTCOM/LEFT if tool is to the right of
the tool path.
See Cutter Compensations with Finish Turning Operations.
- Tool Compensation
- Select a tool compensation number
corresponding to the required tool output point.
The usable
compensation numbers are defined on the tool assembly linked
to the Machining Operation. By default, the output point corresponding to
type P9 is used, if you do not select
a tool compensation number.
- Profile Output
- Select Profile Output on Part to compute
tool path related to the profile output on part, which is the
resultant of the Part Geometry and the tooltip.
When
Profile Output is set to
Profile Output on Part, two tool
paths are displayed during the Simulate or Display. This provides you with the visualization of the
generated tool path position, of the part profile geometry
using CNC machine controller and CUTCOM options:
- The tool path with respect to the Tool compensation
point (orange color).
- The tool path related to the Profile
Output on Part (while color).
- Part Profile
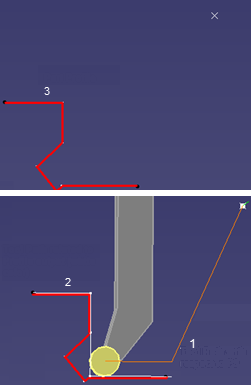
Without damaging the part, an interpolation is
allowed wherever it is not possible to compute the tool path
related to the Profile Output on
Part, as explained below:
- Interpolation is allowed.
- Interpolation is not allowed - The output is the
design profile.
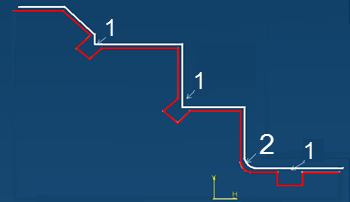
Profile Output on Part is
run with or without Recess
machining.
With Recess machining selected:
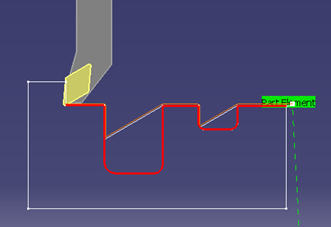
Although the Simulate or Display shows both tool paths, the apt source output file
contains the tool path corresponding to the
Profile Output on Part with clear
start and end blocks.
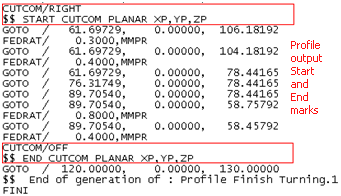
Use the options in the Corner
processing tab to obtain a corner complying
with the designer requirements.
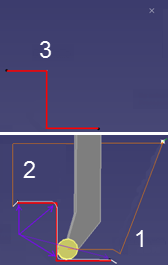
- The tool path with respect to the Tool compensation
point P9 (orange color).
- The tool path related to the Profile
Output on Part (while color).
- Part Profile
Simulation is done based on compensation point
but not based on the Profile Output on
Part.
Note:
Local Invert is not supported
for Profile Output.
- Tool Axis Flip
- Flips the tool axis.
- Tool Axis tab
-
Select the Tool Axis Strategy with other parameters respective to the
strategy selected.
- Tool Axis Strategy
-
Define multiple Tool Axes along the profile to achieve a
more accurate profile finishing.
- Fixed Tool Axis : The tool
axis remains at a constant angle as specified until
the operation is completed.
- Interpolation: Create
multiple axes at different points on the part
profile. Along the part profile between two defined
axes the seeding of the points is done by the
software.
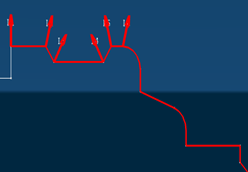
Note:
Seeding is a process where the software divides the
portion between two consecutive points, into a
number of intervals. This is similar to the
process of discretization between two consecutive
points or axes. For example, the path between the
two defined axes has been seeded, by creating
intermediate axis (orange line) at specific
intervals. These intermediate axes are created
such that, their angles and position depend on the
two defined axis.
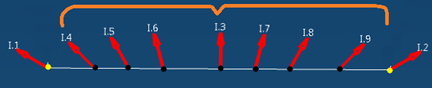
This depends on two parameters, the
discretization angle and the discretization step
size. The angle specifies the maximum angular
change of tool axis between tool positions. And
discretization step ensures linearity between
points that are far apart.
The intermediate tool axes are computed by the
interpolation axis defined. The intermediate
positions are defined by applying rotation to the
initial tool axis, in a plane defined by the
interpolation axis defined.
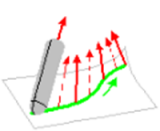
Select the arrow to define the Interpolation
axes, which open up a viewer panel, which has all
the tool axes defined by you over the part
profile. Click over the sensitive red tool axis
icon at the end of the art. The interpolation axis
is defined by picking a point on the part profile.
the commands in the viewer are to define, delete,
and edit the tool axis. The tool axis is created
by specifying a contact point and then defining
the axis over it.
- Normal to Curve: Is computed
by the software internally. In this case along the
part profile, the tool axis is created normal at
each point.
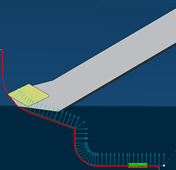
A lead angle can be specified over the
normal to the curve.
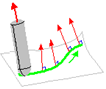
For a concave curve the intersection
between curve 1 and 2 the normal is computed at
the intersection point.
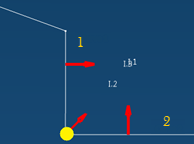
The normal is computed for each contact point
over the part profile. Normal to curve strategy
allows you to customize the calculation of normal
by defining a lead angle. This parameter is
applied over the normal calculated over the
profile.
- Through a Guide: This is used
to machine revolute surfaces. The tool orientation
is controlled by a geometrical curve (guide) that
must be continuous. An open guide can be
extrapolated at its extremities.
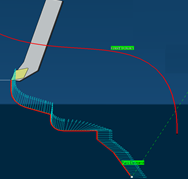
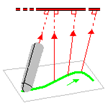
The tool is oriented by the
point that gives the shortest distance between the
guide and the contact point.
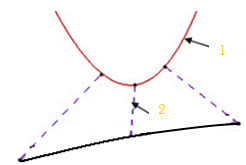
A lead angle can be specified over the Normal
computed over the Guide Curve selected.
Select the red curve in the sensitive icon and
select a curve in the 3D viewer. The tool can be
oriented From or To the guide. The normal
calculated over the guide curve is transformed
over part profile. Also customize the axis
computed over the Guide Curve by specifying a lead
angle over it. This parameter is applied over the
Computed Tool Axis over the Guide Curve.
- Lead Angle
- This is a user-defined incline of the tool axis (1) in a plane
defined by the direction of motion (2) and the normal to the
part surface. The lead angle is with respect to the part surface
normal. (The arrow signifies the forward direction.)
X is the lead angle defined.
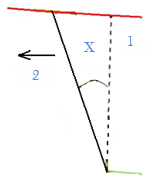
- Step Angle
- Defines the step angle.
- Step Size
- Defines the step size.
Machining Parameters
- Lead-in type
- Specifies the type of lead-in onto the profile at lead-in feedrate.
You can specify:
- Linear: Lead-in up to the point where
profile machining start is defined by the Lead-in
distance and Lead-in
angle parameters.
- Circular: Lead-in is circular and tangent
to the point where profile machining start. It is defined by the
Lead-in radius and Lead-in
angle parameters.
Note:
The lead-in angle is defined with respect to the normal
to the cutting direction. Range of lead-in angle is from -90 to 135
degrees for all tool types except for a grooving tool, where it ranges
from 0 to 90 degrees.
The figure below shows how to set linear lead-in and circular
lift-off.
- Lift-off type
- Specifies the type of lift-off from the profile at lift-off feedrate.
You
can specify:
- Linear: Lift-off from the point where
profile machining ends is defined by the Lift-off
distance and Lift-off
angle parameters.
- Circular: Lift-off is circular and
tangent from the point where profile machining ends. It is
defined by the Lift-off radius and
Lift-off angle parameters.
Note:
The lift-off angle is defined with respect to the normal
to the cutting direction. Range of lift-off angle is from -90 to 135
degrees for all tool types except for a grooving tool, where it ranges
from 0 to 90 degrees.
The figure below shows how to set circular lead-in and linear
lift-off.
- Leading and Trailing Safety Angles
- The insert geometry is taken into account to avoid collision by reducing the
maximum slope on which the tool can machine. The Leading Safety
Angle and Trailing Safety Angle allow
you to further reduce this slope.
Leading and trailing angles can also be
defined on the insert-holder to define the maximum slope on which
machining is done. In this case and if the Insert-Holder
Constraints setting is applied, the angles that reduce
the slope most are taken into account.
- Machining Tolerance
- Specifies the maximum allowed distance between the theoretical and computed
tool path.
- Insert-Holder Constraints
- Specifies insert-holder constraints as:
The following attributes (located on the Insert-holder's
Technology tab) may influence machining: See
Creating and Editing Milling, Drilling, and Probing Tools
- Gouging angle
- Trailing angle
- Leading angle
- Maximum recessing depth
- Maximum cutting depth
- Maximum boring depth
These attributes take tooling accessibility into account and
may reduce the machined area. However, you can use the
Insert-Holder Constraints option to either
ignore or apply these tooling attributes. You can replay the Machining Operation to verify the influence of these attributes on the generated tool
path. The Insert-Holder Constraints
setting does not influence the Leading Safety
Angle and Trailing Safety
Angle.
Corner Processing Parameters
- Entry, Exit, and Other corners
- Entry Corner means the first corner on the Part
profile in the specified machining direction and Exit
Corner means the last corner on the Part profile in the
specified machining direction. Corner processing is proposed for
Entry, Exit, and
Other corners. . The
Entry/Exit corners are determined according to
the specified machining direction and not by the tool motion.
You can specify:
- None: No corners are to be machined along
the profile.
- Chamfer: Only 90 degree corners of the
profile are chamfered.
- Rounded: All corners of the profile are
rounded.
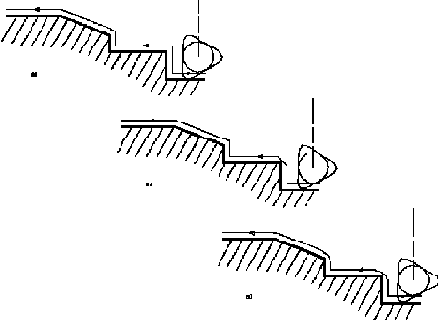
The following options availability depends on the following conditions:
- Chamfer Length: If Other
corner processing mode is
Chamfer.
- Corner Radius: If Other
corner processing mode is
Rounded.
- Entry Corner Chamfer Length: On the first
flank of groove when Entry corner
processing mode is Chamfer.
- Entry Corner Radius: On the first flank
of groove when Entry corner processing
mode is Corner.
- Entry Corner Angle: On the first flank of
groove when Entry corner processing mode
is Corner.
- Exit Corner Chamfer Length: On the last
flank of groove when Exit
cornerprocessing mode is
Chamfer.
- Exit Corner Radius: On the last flank of
groove when Exit corner processing mode
is Corner.
- Exit Corner Angle: On the last flank of
groove when Exit corner processing mode
is Corner.
Local Invert Parameters
The inversion of elements is possible for Profile Finish
Turning operations. This is illustrated in the figure below:
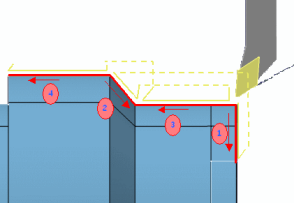
- Invert Lead-in angle
- By default, Specifies Invert lead-in angle to
provide angle control for Invert Lead-in dist
parameter.
By default, the Invert lead-in angle
value is 90 degrees.
- Invert Lead-in dist
- Specifies Invert lead-in distance to approach
distance from the inverted profile.
- Invert Lift-off angle
- Specifies Invert lift-off angle to provide angle
control for Invert Lift-off dist parameter.
By
default, the Invert lift-off angle value is 45
degrees.
- Invert Lift-off dist
- Specifies the exit distance from the inverted profile.
- Invert Strategy
- Specifies the invert strategy.
To machine part with inverted elements,
the following Invert strategies are available:
- Thickness: A given thickness is set on the
inverted element and the remaining material is removed
when the inverted element is machined again.
- Overlap: A given length of an element is
machined twice, which is when the profile is machined and then
when inverted elements are machined. In this case, you can
choose to machine inverted elements first or machine them
later.
- None: No invert strategy is applied.
- Machine inverted elements first
- Select this check box to machine the inverted elements in the first path,
and then the other elements.
- Invert Lift-off type
- Specifies the type of entry and exit motion.
You can specify:
- Linear motion defined by a distance and
an angle.
- Circular motion defined by a radius and
an angle.
Note:
The lead-in and lift-off is linear or circular as specified in the
Machining tab.
- Automatic inverted way of machining
- Select this check box to automatically make local inversions and have EKL
accessibility. By selecting this option, the toolpath generated will take
into account the local inversion applicable to elements of the profile.
Note:
You can also set local inversions manually when you select the
Inverted way of machining check box in
the Local Information Editor dialog box. If you
manually set local inversions in this manner, and you select this
option to automatically set local inversions, then existing manual
inversions are deleted. In this case, the tool path is also computed
based on the automatic method.
- The following rules are applied for calculation of machining direction when
Automatic inverted way of machining is
selected:
- Rule 1:
When the large vector is from the center of the insert to the
center of the active tip. Diamond, Square, and Triangular
Inserts:
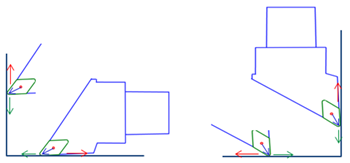
- Rule 2:
When the centers of the insert and the active tip are equal to
zero, then the vector is from the tool carrier to the center of the
active tip. The machining direction is the scalar product of the vector
and must be on the positive section of the profile. Round
Insert
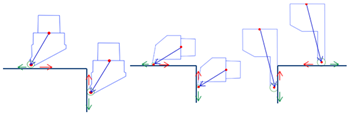
Groove Insert
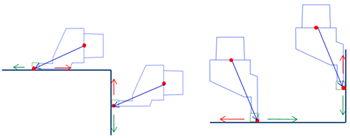
- Rule 3:
When the scalar product multiplied by the machining direction is
equal to zero on the entire portion of the profile. The vector is from
the tool carrier origin to the center active tip. The machining
direction is the scalar product of the vector and must be on the
positive section of the profile. Groove Insert
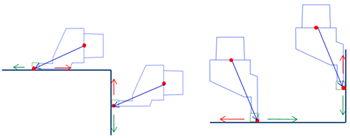
Diamond Insert
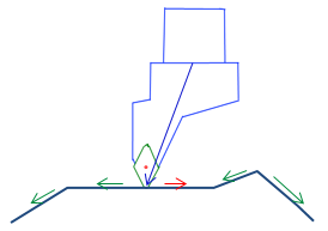
Square Insert
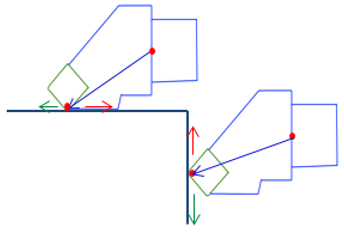
- Rule 4:
This applies in addition to Rule 2 or Rule 3. When the vector is
equal to the value of the tool carrier origin to the center active tip.
It us also when the vector multiplied by the machining direction is
equal to zero. The machining direction is what limits the number of
local inversions. Diamond Insert
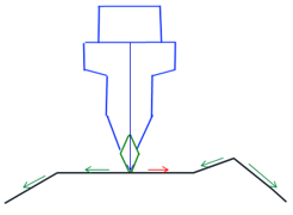
Round Insert
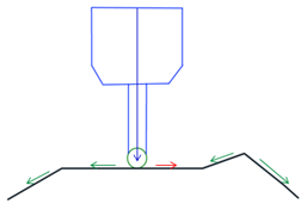
The Inversion Point on a radius is when the vector multiplied
by the machining direction is equal to zero.
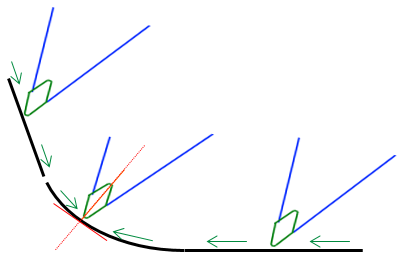
|