
Strategy Parameters
- Tool Axis
The Tool Axis command in the Turning
Operations dialog box is represented by an arrow when
creating a part operation.

See Defining the Tool Axis
- Max Depth of Cut
- Specifies the maximum distance between passes.
- Roughing Strategy:
- Specifies roughing strategy as:
- Orientation
- The selected orientation defines the type of geometric relimitation to
be done between the rough stock and part geometry in
order to determine the area to machine.
You can specify:
- External,
Internal for
Longitudinal recessing
strategy.
- External,
Internal, or
Frontal for
Face recessing strategy.
External Ramp Rough Turning
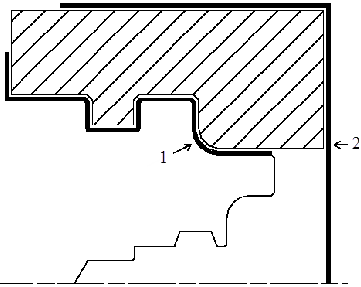
1 is Part
Profile
2 is
rough stock Profile
Internal Ramp Rough Turning
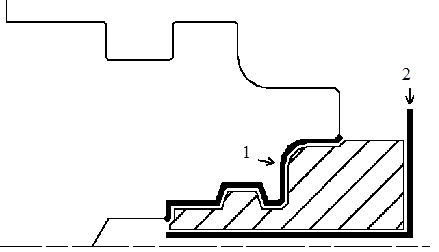
1 is Part
Profile
2 is
rough stock Profile
Frontal Ramp Rough Turning
In Frontal orientation, the minimum and
maximum diameters of the area to machine are determined by the rough
stock profile dimensions.
For example, in the following figure the area to machine is relimited
by the spindle axis because the rough stock profile is also
relimited by the spindle axis.

1 is Part
Profile
2 is
rough stock Profile
- Location
- Specifies location.
It determine the way the program closes the area
to machining. The following machining
location types are proposed:
- Front: the part is machined toward the
head rough stock
- Back: the part is machined from the head
rough stock
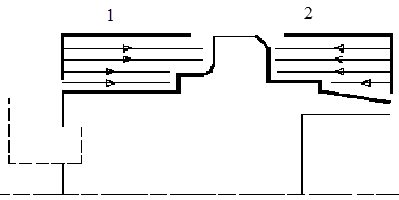
- Machining Direction
- Specifies the machining direction with respect to the spindle axis. You
can specify Machining Direction only for
Face roughing with
Frontal orientation. The choices are:
- Under Spindle Axis Machining
- Select this check box to request machining under the spindle axis, for
Face roughing strategy
- Tool Compensation
- Select a tool compensation number corresponding
to the desired tool output point.
The usable compensation numbers are defined on the tool assembly
linked to the Machining Operation.
By default, the output point corresponding to type
P9 is used, if you do not select a tool
compensation number.
Options
- Entry Flank Angle
- Specifies the entry flank angle.
The insert geometry is taken into
account to avoid collision by reducing the maximum slope on which
machining is done. Defining an Entry Flank
Angle on the Machining Operation allows you to further reduce the area to machine.
- Clearance
- Specifies values on the check element for the first and
second cuts.
A leading angle can also be defined on the insert-holder
to define the maximum slope on which machining is done. In this case
and if the Insert-Holder Constraints setting
is applied, the angle that reduces the slope most is taken into
account.
- Insert-Holder Constraints
- Specifies insert-holder constraints as:
The following attributes (located on the Insert-holder's
Technology tab) may influence machining:
See Creating and Editing Milling, Drilling, and Probing Tools:
- Trailing angle
- Leading angle
- Maximum recessing depth
- Maximum boring depth
These attributes take tooling accessibility into account and may
reduce the machined area.
However, you can use the Insert-Holder
Constraints option to either ignore or apply these
tooling attributes. You can replay the operation to verify the
influence of these attributes on the generated tool
path.
The Insert-Holder Constraints setting does not
influence the Entry Flank Angle.
- Minimum Machining Radius
- Specifies the minimum machining radius.
This option is available when Orientation is
External.
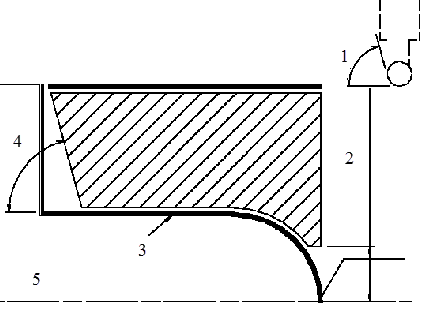
- Leading Angle (Defined on Tool)
- Minimum Machining Radius
- Part Profile
- Leading Angle
- Spindle Axis
- Maximum Machining Radius
- Specifies the maximum internal machining radius.
This option is available when
Machining Direction is From
Spindle.
Note:
Maximum boring depth is defined on the
tool.
- Axial Limit for Chuck Jaws
- Specifies the axial limits. Offset defined from the machining axis system.
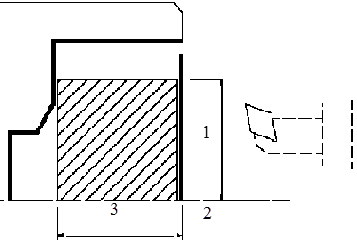
- Maximum Machining Radius
- Spindle Axis
- Max Boring Depth
- Machining Tolerance
- Specifies the maximum allowed distance between the theoretical and
computed tool path.
Rework Parameters
- Lift-off Distance and Lift-off Angle
- Specifies Lift-off Distance and
Lift-off Angle.
These parameters define
the lift-off vector at the end of each pass with respect to the
cutting direction.
- Lead-in Distance
- Specifies Lead-in Distance with respect to the
cutting direction. It takes the rough stock profile and rough stock
clearance into account. The tool is in RAPID mode before this
distance.
- Start pass mode
- Specifies the pass mode. This is defined by one of the following
settings:
- Rework Mode
- Select this check box to make the following options are available:
- Distance before Rework Plunge
- Angle before Rework Plunge