Launching the Synchronization Manager
, the Synchronization Manager panel
appears in the left side bar. It has a tree view that shows all of the loaded design
products in the session with the name/icon in the expanded state.
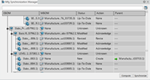
See also Scope Link Creation on Assembly Item.
To collapse a specific row that has children rows, double-click a cell in the EBOM column. You
do not want to execute Compute, all columns show
Unknown except for the EBOM column. To advance to the next
steps, Compute is required. Synchronize is
disabled by default the first time.
The columns:
- MBOM: This shows the name and icon of the corresponding implementing
Manufactured Item if it exists. If not, None and displays the
expected icon. The other columns fill up depending on this column.
-
Status: There are 5 possibilities:
- New: Corresponding Manufactured Item does
not exist.
- Deleted: Design part does not exist in the session but the
corresponding Manufactured Item exists.
- Modified: Simple modification on design part or attribute change,
which DELMnOSynchronizePLMAttributes.CATRule determines.
- Revised: Design part has a version. To detect the version status, the
option Check Versioning for Synchronization Manager
in the Preferences, upper right corner in the dialog box
widget has to be selected.
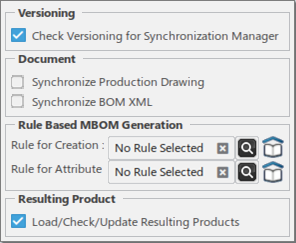
See Synchronization Manager for Resulting Product scenario's. This option
is to detect the revised design product during computation. If this
option is OFF, a new status appears for the
revised design product. The Deleted status
appears for the Manufactured Item of the previous revision product
because the implement link does not exist. Synchronize
Production Drawing: This option is cleared by default.
Production Drawing which is attached to a manufacturing assembly update
by the Synchronization Manager when this option
is ON.
Synchronize BOM XML: This option is cleared by
default. When this option is ON, the BOM XML that
is attached to the manufacturing assembly refreshes by the
Synchronization Manager. This is referring to
the Consider Direct Children Only option of
Production Drawing.
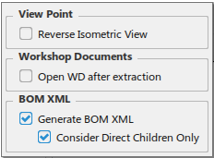
Rule based MBOM Generation
Rule for Creation: Defining this rule, the
Parent Manufactured Item and its Manufactured Item Type automatically
defines it by this rule for the new status row after computation.
Rule for Attribute: This rule applies
attributes to the newly created Manufactured Item after synchronization.
- Catalog Browser
, the text appears Select or search an
object or Press ESC to exit. In the
Search window, select
Catalog from the list window. Type your catalog
name or type catalog.
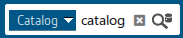
All of the catalogs appear in the search tab window.
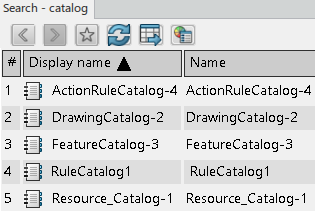
Double-click a catalog, example
DrawingCatalog-2, this opens the catalog.
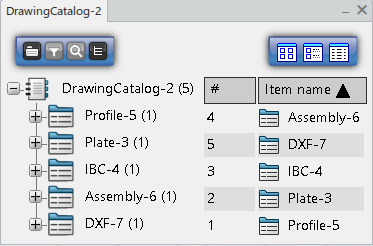
A Catalog is a tree structure consisting of the following elements:
- Chapters: A chapter references other chapters
or items. Use to classify items by category.
- Items: An item is a reference to an external
document or PLM Object. Items describe them with keyword
values.
- Keywords: A keyword is an attribute
describing a chapter or item. The Librarian can associate keywords
to a chapter or item, and assign keyword values to each item. Search
by keyword values to filter its content.
Libraries classify standard objects according to user-defined
attributes. A Library consists of Classes, which categorize the objects
in the Library hierarchy. Items are the actual objects that they
manage. Library to navigate, search, and
select an item with better view and performance. The Library has a class and
a description by an item.
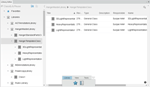
The keyword in the catalog replaces by an attribute in the library
and the filter updates accordingly. After a resource selection, the
positioning information and auxiliary viewer updates with the resource and
selected manufacturing assembly.
- Action: Determines status column and performs two behaviors;
Execute/Ignore.
Status |
Action - Execute |
Action - Ignore |
New |
Create Manufactured Item creates under the parent Manufactured
Item that defines the Parent column. Implement
link creates between newly made Manufactured Item and
design product.
|
None |
Deleted |
Delete Manufactured Item that does not
have implement link anymore, deletes.
|
None |
Modified |
Acknowledge Resulting Product updates
based on design product.
|
None |
Revised |
Revise New revision of current Manufactured Item creates.
Replaces current Manufactured item by newly
revised Manufactured item and implement link reroutes.
|
None |
Up To Date |
|
None |
- Parent: This is for New status and shows
Manufacturing Assembly name/icon if you choose the father Manufacturing Assembly. In
the case of the root node, father is the root Manufacturing Assembly by default. To
choose father, right-click a cell in the Parent column then
the Manufactured Item Tree Dialog appears. Then you can select the parent
Manufacturing Assembly on this panel.
- Compute: Synchronization Manager starts to
compute the status for the selected product node in the panel. If there is no
selection, then all loaded design products in the session compute.
- Synchronize: Synchronization Manager starts to
synchronize the MBOM status based on EBOM status and determined action.
- Filter box: As soon as you put a keyword on the filter box at the top
of the Synchronization Manager panel, the EBOM column filters
for the piece parts.
-
Customization Dialog is located next to the filter box and it
is meant to customize columns in the Synchronization Manager
panel. If clicking, the Customization Dialog, which consists
of check boxes with the titles of PLM attributes, appears. Within this, you can use
the Filter Pop-Up to filter the other columns by (Select
All), Modified, Up-To-Date,
Unknown, Revised,
New, and Deleted. When clicking
these header columns, all the values of the current column lists on the pop-up, and
then you can filter the column by selecting a value. For the date type column, the
Synchronization Manager panel provides the user with a
different filter pop-up, Custom Filter. There are two modes
for filtering the date type column:
-
Manual - Filter pop-up shows a date/time tree to
select the date and time manually, the hierarchy is
Year-Month-Day-Hour-Minute-Second.
- Custom - Put a specific date and time value as
filtering keywords. And you can customize the filtering condition by using
two dialogs and And/Or operators. The format of the
keyword must be the same as month/day/year or
month/day/year hour:minute:second. If there is no
time value, then it fills with the default time (00:00:00). Clicking the
Calendar, select a date from the calendar to
define the filter keyword. As soon as you select a date from the calendar,
the keyword box fills with a selected date and default time (00:00:00).
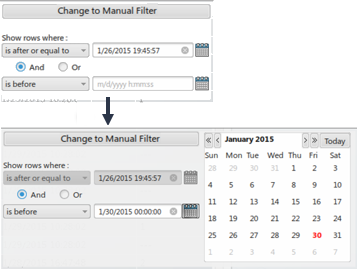
|