Machining Parameters
Note:
The tabs User Parameters and Output
require specific conditions to be displayed.
- Tool path style
- Specifies the tool path style.
The options in the Tool
path style menu are as follows:
- Helical: the tool moves in successive
concentric passes from the boundary of the area to machine
toward the interior. The tool moves from one pass to the next by
stepping over.
- Back and forth: the
machining direction is reversed from one path to the next.
- Machining tolerance
- Specifies the maximum allowed distance
between the theoretical and computed tool path. Consider the value to be the
acceptable chord error.
- Cutting mode
- Specifies the position of the tool regarding the surface to be machined.
The options in the Cutting
mode menu are as follows:
- Climb:
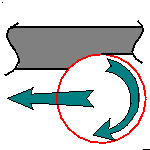
- Conventional:
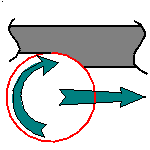
- Machining mode
- Defines the type of area to be machined.
The
options in the Machining mode menu are as
follows:
- By plane: the whole part is machined
plane by plane
- By area: the whole part is machined area
by area
then
- Pockets only: only pockets on the part are
machined
- Outer part: only the outside of the part
is machined
- Outer part and pockets: the whole part is
machined outer area by outer area and then pocket by pocket.
- Helical movement
- Specifies the way the tool moves in a pocket or an external zone. This is
available for Helical tool path style.
The options in the
Helical movement menu are as follows:
- Inward: the tool starts from a point
inside the zone and follows inward paths parallel to the
boundary.
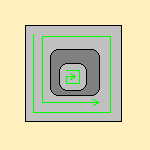
- Outward: the tool starts from a point
inside the zone and follows outward paths parallel to the
boundary.
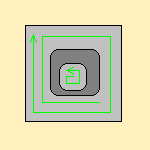
- Both: For pockets, the tool starts from a
point inside the pocket and follows outward paths parallel to
the boundary. For external zones, the tool starts from a point
on the stock boundary and follows
inward paths parallel to the boundary.
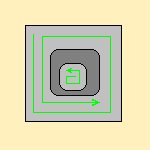
- Always stay on bottom
-
When this parameter is activated, most
Return on Same Level macros are replaced by
optimized linking motions that force the tool to remain in contact with the
pocket bottom when moving from one domain to another. This avoids unnecessary
linking transitions.
Clearance lets you define a clearance for linking
motion between consecutive passes.
Feedrate lets you define the feedrate for linking
motion between consecutive passes.
- Part contouring
- When selected, lets the tool machine
the outside contour of the part before roughing.
- Contouring pass ratio
- Specifies the position of the final pass for removing scallops. This is done
by entering a percentage of the tool diameter (0 to 50). This
is available for Back and Forth tool path style.
- Truncated transition paths
- Enables the tool to follow the external profile more exactly by allowing the
transition portion of the trajectory to be truncated. this is available for Back and
Forth tool path style.
- Truncated transition paths is selected:
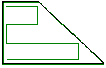
- Truncated transition paths is not selected:
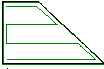
- Fully engaged tool management
- Manages full material cut when
roughing hard material, where the step over is not always respected and
where the tool is damaged. This is avoided by switching to a trochoid motion
that reduces the step over, or by adding machining planes to reduce the load
on the tool.
Full engagement is detected when:
- More that 75% of the tool diameter is engaged in the material.
- or More than 120 degrees of the tool is in contact with the
material
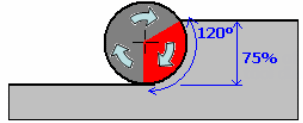
The options in the Fully engaged tool management
menu are as follows:
- None: No management of the tool
engagement.
- Trochoid: Adds a trochoid motion in areas
where the step over is not respected. The trochoid motion is
managed by
- the Minimum trochoid radius(1-
Full material milling detected, 2 - Full milling
replaced by Trochoid motions):
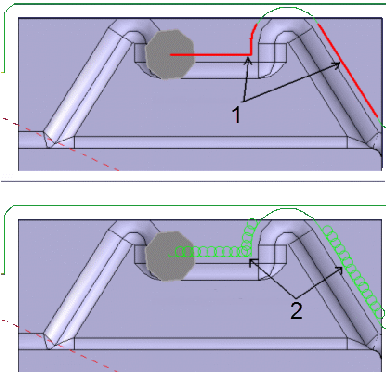
By default, the Minimum trochoid
radius value is 1mm.
- the Max engagement.
By
default, the Max engagement
value is 0.5mm.
- MultiPass: Adds machining planes in areas
where the step over is not respected. The distance between those
additional planes is managed by the parameter Maximum
full material cut depth. In previews and
replays, a warning is displayed if this cut depth is greater than the
Maximum cut depth.
Radial Parameters
- Step over
-
The options
in the Step over menu are as follows:
- Overlap ratio: the overlap between
two passes, given as a percentage of the tool diameter.
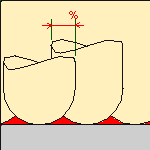
- Overlap length: the overlap between
two passes, given as a distance.
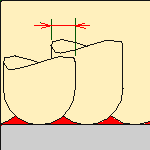
- Step over ratio: the step over
between two passes, given as a percentage of the tool
diameter.
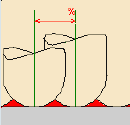
- Step over length: the step over
between two passes, given as the maximum distance between
passes.
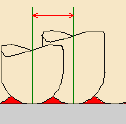
- Tool diameter ratio
- Specifies the tool diameter ratio. This is available when
Overlap ratio is selected as Step
over.
Axial Parameters
- Maximum cut depth
- Specifies depth of the cut done by the tool
at each pass.
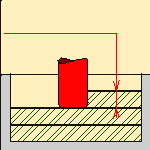
HSM Parameters
- High Speed Milling
- Specifies whether or not cornering for
HSM is done on the trajectory.
- Corner radius
- Specifies the radius used for rounding the
corners along the trajectory of an HSM operation.
The tool path is
rounded to give a smoother path that can be machined faster. The minimum
value of the corner radius is the radius of the tool. Note:
Value must
be smaller than the tool radius.
- Corner radius on part contouring
- Specifies the radius used for
rounding the corners along the part contouring pass of an HSM operation.
Note:
This radius must be smaller than the value set for the
Corner radius.
Output
This tab is displayed when the check box2D circular interpol
is clicked in the Numerical Control tab of the machine. See
NC Machining Apps Common Services: Assigning a Machine with the Machine Editor
- Circular Interpolation
- When selected, lets you generate an
arc interpolation output when the tool is in contact with a revolution
surface (but not with one represented by a CATNurbsSurface). This arc is
propagated to radial paths created by offset of this path, when they exist.
By default, this check box is not selected.
- Helical Interpolation
- To set the helical syntax as the output instead of GOTO points, enable the
following options:
- Helical Interpolation in the
Numerical Control tab of the NC
Machine Definition dialog box.
- Helix option from the
Mode menu in the Macro
Parameters tab of the Roughing
dialog box.
Geometry
You can specify the following geometry:
- Automatic horizontal areas detection
-
- When this check box is not
selected, the only way to ensure that a cutting plane corresponds
with a horizontal area is to define an Imposed
plane crossing the area. This means that you have to
consider the offset on part. This plane applies to the whole part,
which is not required. If there are several horizontal areas to
consider at different levels you have to define all of the
corresponding Imposed planes. Black planes in
the figure below, orange planes are standard planes 1 - Offset on
part, 2 - Stock, 3 - Part.
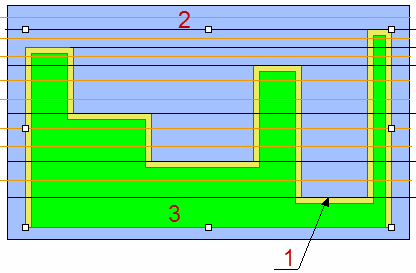
- When this check box is selected, you can do the following:
- Automatically detect horizontal areas on the part.
- Limit the cutting plane effect to these areas.
- Apply a dedicated offset on the part for these areas.
- Define the Maximum angle that is considered as horizontal.
The angle is measured perpendicular to the tool path (1 -
Offset on part, 2 - Stock, 3 - Part, 4 - Cutting Planes
limited to the Horizontal areas, 5 - Offset on Horizontal
Areas.
- Detect planar surfaces accessible for the tool.
- Computes the exact location of the paths on the horizontal
area.
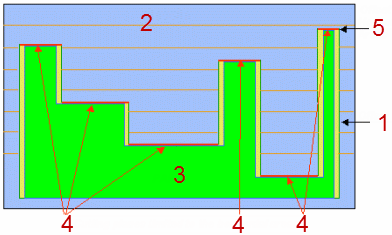
If the machining mode is:
- By area, the tool path looks like this:
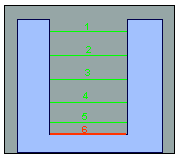
- By plane, the tool path looks like this:
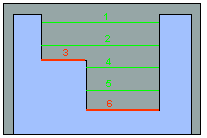
The cutting planes in green are the standard roughing tool paths. The red
ones are those computed for the horizontal areas detected.
Notes:
- The computation of horizontal areas is not possible if the part
is made of a cloud of points (STL).
- When only outer part areas are to be machined, no specific tool
path style is given for the pockets. As a consequence, if the
tool path style used for the outer part areas is not compatible
with pockets (example, By Offset on part with
One-Way), horizontal areas are machined with a
default tool path style (Concentric).
- Contouring paths, hard soft attributes along pocket boundaries, tool holder
collision checking, circular interpolation are managed in horizontal areas
like in standard sections.
- Offset
- Defines the distance that
the tool can overshoot the Position. It is expressed
as a percentage of the tool diameter. This parameter is useful in cases
where there is an island near the edge of the part and the
tool diameter is too wide to allow the area behind the island to be
machined. This parameter can only be used if the
Position is Inside or
Outside.
- Limit Definition
- Defines what area of the part is
machined with respect to limiting contours. It can either be inside or
outside. In the pictures below, there are three limiting contours on the
stock. The yellow areas are machined:
- Side to machine: Inside
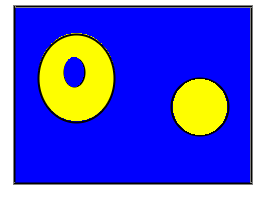
- Side to machine: Outside
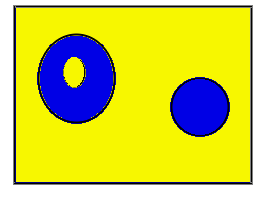
- Limit the Machining Area
- With R210 release, the tool motion is added along limit line on both sides, to remove
residual material around the limit line and secures the machining on lower
levels. Now, there is no collision between the residual material and tool
holder and height of removed material is also not greater than the distance
between levels.
The machining trajectory is more secure because of these
paths and removes residual material on both sides before machining the
bottom.
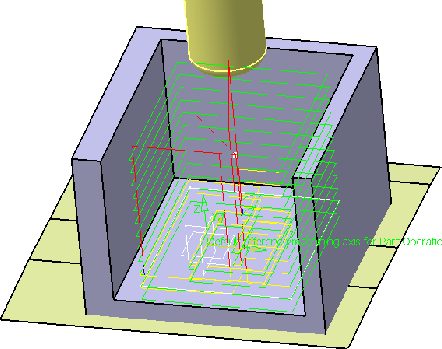
- Ignore holes on stock
- When selected, ignores holes, which are on
the stock. Once this check box is selected, define the diameter value below
which holes are to be ignored.
- Compute with tool holder
-
- When selected, the tool path
is computed so as to avoid collisions with the tool holder and you
can define an offset on the tool holder assembly.
- When this check box is cleared, the tool path is computed only with
the tool.
Feedrates and Speeds Parameters
- Transition
- You can locally set the feedrate for a transition path to a
machining operation B from a
machining operation A or from a tool change activity. This is done by
selecting the Transition check box in the Machining Operation dialog box
for operation B.
For more information, refer to the Setting a Transition Feedrate.
- Slowdown Rate
- Reduces the current feedrate by a
given percentage. The reduction is applied to the first channel cut and
to the transitions between passes:
- In Helical tool paths, the reduction is
applied to the first channel cut.
- In Back and Forth tool paths, the
reduction is applied to the first channel cut and to the
transitions between passes.
- Feedrate Reduction in Corners
- You can reduce feedrates in
corners encountered along the tool path depending on values given in the
Feeds and Speeds tab page:
- Reduction rate
- Maximum radius
- Minimum angle
- Distance before corner
- Distance after corner
Feed reduction is applied to corners along the tool path whose radius
is less than the Maximum radius value and
whose arc angle is greater than the Minimum
angle value.
For Pocketing, feedrate reduction applies to
machining and finishing passes:
- for all corners in Back and forth and
Concentric mode,
- for inside corners in Inward and
Outward Helical modes, in
Offset on part One-way and Zigzag,
in Inward and Outward
Spiral Morphing.
When machining pockets, feedrate reduction applies to inside and
outside corners for machining or finishing passes. It does not apply
for macros or default linking and return motions.
Corners are angled or rounded, and may include extra segments for HSM
operations.
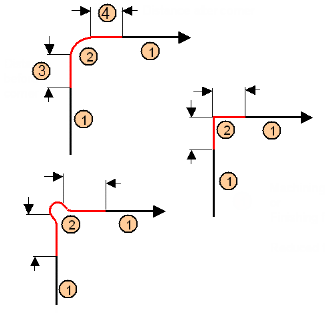
- Machining feedrate or Finishing feedrate
- Reduced feedrate
- Distance before corner
- Distance after corner
- Combining Slowdown Rate and Feedrate Reduction in Corners
-
If a corner is included in a slowdown path, the general rule is that
the lowest percentage value is taken into account. For example:
- if the Slowdown rate is set to 70%
and Feedrate reduction rate in corners is set to 50%, the
feedrate sequence is: 100%, 70% (entry in slowdown), 50%
(entry in corner), 70% (end of corner, still in slowdown),
100% (end of slowdown).
- If feedrate Reduction rate in corners
is then set to 75%, the feedrate sequence is: 100%, 70%
(entry in slowdown), 70% (entry in corner: 75% ignored), 70%
(end of corner, still in slowdown), 100% (end of slowdown).
- Spindle output
- This check box manages output of the SPINDL instruction in the generated
NC data file:
- If the check box is selected, the instruction is generated.
- Otherwise, it is not generated.
Note:
The spindle speed is defined
in linear (length per minute) or angular (length per
revolution) units.
- Angular: length in
revolutions per minute and unit is set to mm_turn.
- Linear: length in feed per
minute and unit is set to mm_mn.
- Quality
- The feed and speed values are computed according to the
Quality setting on the operation.
- Compute
- Feeds and speeds of the operation is updated according to tooling feeds
and speeds by clicking the Compute command
located in the Feeds and Speeds tab of the
operation.
Feeds and speeds of the operation is updated automatically according to tooling data
and the rough or finish quality of the operation. This is described in About Feeds and Speeds.
NC Macros
The following types of macro are defined on a Prismatic
Roughing operation:
- Pre-Motion Macros: These macros are built using the
elementary motions proposed in the Current Macro
Toolbox. A premotion macro is applied between the rapid
motion from safety plane and the automatic macro.
- Post-Motion Macros: These macros are built using the
elementary motions proposed in the Current Macro
Toolbox. The post-motion macro between the automatic macro
and the rapid motion from safety plane.
- Automatic Roughing Macros: Select one of the
following approach modes to specify how the tool
can engage the material.
- Plunge: the tool plunges vertically.
- Ramping: the tool moves progressively down at
the ramping angle.
Ramping approach mode applies to pockets
but also to outer areas in given conditions:
- If a limit line is used, the tool can approach outer areas
of the part and pockets in ramping mode.
- If a lateral approach is not possible (due to the check
element), the approach is made in ramping mode.
- Helix: the tool moves progressively down at
the ramping angle with its center along a (vertical) circular helix
of Helix diameter.
- Radial Only: When drilling holes exist,
define start points and this mode to avoid any plunge or ramping
macros. If a radial engagement is not possible (collision with part
or with the residual material), the roughing tool path is stopped.
- Clearance
- Two modes are available:
- Along tool axis: When selected, tool retract
movements will be along the tool axis all the way to the selected
plane. A clearance plane must be selected.
- Optimized: When selected, optimizes tool
retract movements. This means that when the tool moves over a
surface where there are no obstructions, it will not rise as high as
the safety plane. This is because there is no danger of tool-part
collisions. As a result, it saves time.
Notes:
- Optimized clearance takes the
rough stock left by the previous operation into
account.
- If you have defined a safety plane, deactivate
Clearance. If you do not, the
safety plane will be ignored.
- Approach distance
- Engagement distance for the selected
approach mode.
- Radial safety distance
-
Distance that the tool moves
horizontally before it begins its approach.
- Circular approach
- When selected, creates circular
engagements from external zones, with the given Circular approach
radius:
- A cornering arc is inserted in the approach movements.
- All the movements are tangent except when a collision could occur
between the arc and the part.
- Engage from outside
- In case of open pockets, when selected
creates engagements from external zones.
- Limitations on Circular approach and
Engage from outside
-
- By default, the point used for external engagement is the point on
the stock closest to the pattern start point.
- In case of collision, it tries to compute a pattern avoiding
collision.
- If some collisions remain in planes you have defined, you can define
a start point to help find out a pattern, which avoids the
collision.
- If some collisions remain in some planes even with the defined start
point, a ramping approach is created.
|