-
From the
Axial Machining section, select Sequential
Groove
then a position in the Manufacturing Program.
A typical part to machine with two grooves looks like this:
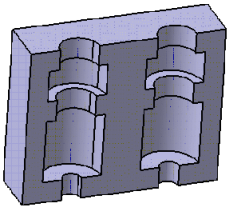
- A Sequential Groove entity is added to the
Manufacturing Program.
- The Sequential Groove dialog box opens directly at
the Geometry tab
. This
tab includes a sensitive icon to help you specify the geometry.
- Areas colored red, texts such as No point and
No geometrical feature has been selected
indicated that geometry is required.
-
Still in the Geometry tab which comprises a
Global and a Local tab:
-
In the Global tab, select the red groove depth
representation then select the two holes.
See Selecting Geometry for more information.
The sensitive icon is updated with information such as the number of
machining points, the depth and diameter of the first selected hole,
...
-
Set Number of Levels to 2.
-
In the Local tab, select the plane representations
in the sensitive icon, and the desired planes in the part.
Plane 1 is the plane of the first groove in the part, plane 2 is the
plane of the second groove.
-
Optional: Select the axis representation in the sensitive
icon to invert the tool axis direction.
-
Optional: Select the check boxes below the sensitive icon
to modify the corresponding data.
-
Select the Motions tab in the
Strategy tab
and define the
required motions.
-
Click the icon corresponding to the required motion.
-
Select values from the lists, or key in the values.
-
Click OK to add the motion.
For example:
Rank |
Name |
Plane number |
Compensation |
Feed Rate |
Appl. Mode |
1 |
Go To Plane.1  |
1 |
2 |
50mm_mn |
- |
2 |
Circular.1  |
- |
- |
Machining |
- |
3 |
Go To Plane.2  |
2 |
1 |
50mm_mn |
- |
4 |
Circular.2  |
- |
- |
Machining |
- |
5 |
Go To Clearance.1  |
- |
1 |
50mm_mn |
Last Level |
The motions are added and listed in the dialog box.
-
Select the Tool tab
and choose a tool, example, a T-slotter tool with a
nominal diameter lower than that of the top hole.
Drill, multi diameter drill, spot drill, center drill, countersink, tap, two
sides chamfering, boring and chamfering, boring bar, reamer, T-slotter, end
mill, face mill, thread mill, conical mill and counterbore mill tools are
supported. See Assigning a Tool Element to a Machining Operation.
-
Click More >> and select the
Compensation tab to specify a second corrector.
-
Select the Feeds and Speeds tab
to specify the
feedrates and spindle speeds for the operation.
-
Select the Macros tab
to specify the
desired transition paths.
See Defining and Editing Macros
-
Click Display or
Simulate to check the validity of the operation.
See Simulating the Tool Path.
- The tool path is
computed.
- A progress indicator is displayed.
- You can cancel the tool path computation at any moment before 100%
completion.
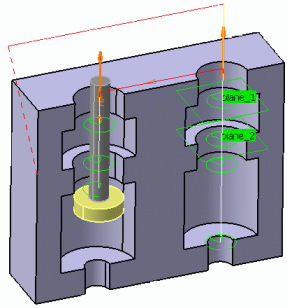
-
Click OK to create the operation.
|