-
From the Surface section of the action bar,
click Polishing profile
and
select a robot in the work area.
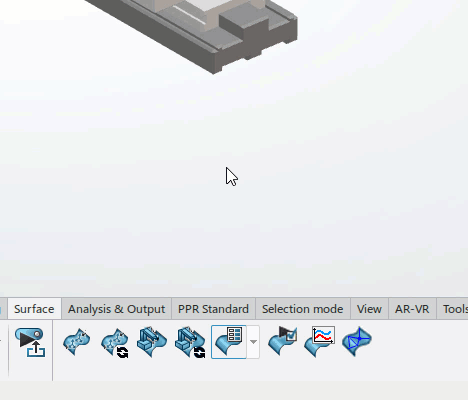
The Polishing profile dialog box appears.
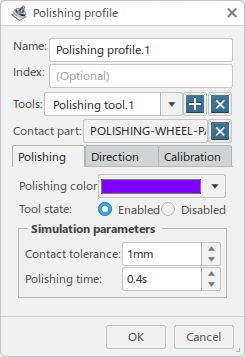
-
You can enter a Name and specify an Index
for the new profile.
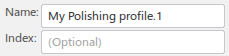
-
Select a polishing tool from the Tools list of available tools.
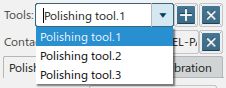
Click to add a polishing tool to the list, and to remove a tool from the list.
-
In the Polishing tab, click the Polishing
color list to select a color for the object.
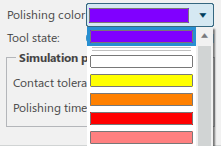
-
Select Enabled in the Tool state section
for abrasion to occur on the polished surface. Select Disabled for
no abrasion.

Note:
Several tools can be associated to a robot. They can be activated or deactivated per
profile.
-
In the Simulation parameters section:
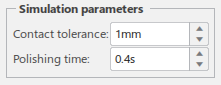
-
Contact tolerance specifies the reference contact tolerance
between the polishing wheel/belt and the product.
-
Polishing time specifies the time at each surface point to
produce the ideal 100% abrasion exposure during simulation.
-
Click the Direction tab.
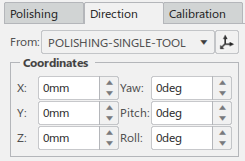
-
The current selection in the From list specifies the tool
profile from which the polishing part normal is relative to.
Click to further refine
the position.
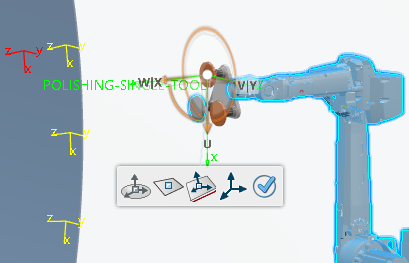
-
The Coordinates section specifies the offsets for
X, Y, Z,
Yaw, Pitch, and
Roll from the current TCP location.
-
Click the Calibration tab.
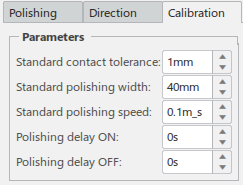
-
Standard contact tolerance specifies the reference contact
tolerance between the polishing wheel/belt and the product.
-
Standard polishing width specifies the width of the
reference polishing wheel/belt.
-
Standard polishing speed specifies the reference robot TCP
speed that will result in 100% abrasion exposure.
-
Polishing delay ON specifies the time delay in spray
deposition turning on after shot flow is turned on.
-
Polishing delay OFF specifies the time delay in spray
depostion turning off after shot flow is turned off.
-
Click OK to create the new Polishing profile.
The new profile appears in the Profiles side tab:
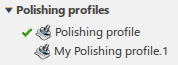
The profile can be edited by double-clicking the thumbnail in the Profiles side tab.
-
From the Surface section of the action bar, click Surface
Trajctory
and create one
or more surface trajectories as described in Generating Paths.
-
From the Surface section of the action bar, click Generate Robot
Task
and create a task as described in Generating Surface Tasks.
Note:
In the Trigger Parameters section of the Create
Operations dialog box, select the polishing profile created above from the
App. Profile list.
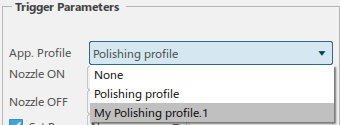
-
Set the Paint Results tab of Simulation
Options for Polishing.
-
Select the task in the Behavior side tab, and click Play in the Compass to simulate the task.
|