-
Activate a physical product or a 3D shape representation to be
used as a context.
- If the context is a
physical product, a separate insulation 3D part with insulation feature, is
created for each selected support.
- If the context is a 3D
shape representation, insulation feature is directly created under the
representation.
-
From the
Structure Insulation section of the
action bar,
click
Structure Profile Insulation
.
-
In the
Structure Profile Insulation panel, select a PLM
type from the list.
Note:
The PLM type list is available only for physical
product context.
-
Enter the name of the insulation feature.
You can keep the default name derived automatically.
-
In the Support box, select profiles to insulate.
- Optional:
Click Combine/Separate
to
combine the insulations of the profiles whose traces are connected in G0
continuity.
In the Element List, the first profile is used as a reference for
creating the insulation. The icon
is displayed in front of it. The insulation is created taking into account the
properties of this reference profile only. You can select a different profile
and click Set as Reference
to
set it as a reference. The profile is moved to the top in the list and set
as a reference for insulation creation.
Notes:
- A single insulation feature is created for the combined
insulations.
- By default, the Combine/Separate
button is turned off and a separate insulation is created for
each selected profile.
- If some profiles are not connected to the reference profile, an
error message appears and such profiles are removed from the
selection.
- For stiffeners on free edges created on multiple panels, the profile
insulation considers the thickness of the reference panel only.
- The Support panel of stiffener check box in
preferences must be selected if it was selected while creating the
stiffeners.
- After splitting a combined insulation, the newly created insulations
have the same properties as that of the combined insulation.
-
Under Contour Definition, select one of the following
contour types:
Contour Type | Description |
---|
Bounding box |
Insulation is created using the bounding box of the profile.
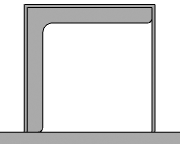
You can change the slope angle for insulation over stiffeners.
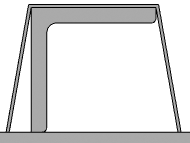
|
Section |
Insulation is created using the section of the profile.
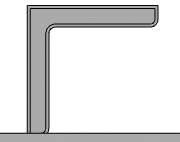
|
Formed shape |
Insulation is created with a formed shape. The shape is computed
using the T1, T2, W, h1, and h2 parameters.
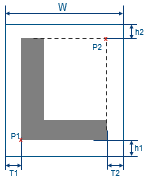
You can do any of the following:
- From the Mode list, select any of the
following combinations and specify the values of the
parameters to compute the shape: T1 +
T2, T1 + W, or
T2 + W.
- Click ƒx Thickness to link the
parameters to the profile thickness and compute the shape
automatically using a formula. In case of a combination that
includes W, you need to specify the value of W.
For stiffeners, you can specify the value of the h2
parameter as zero. Result:
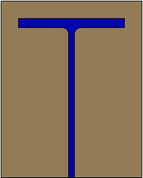
|
- Optional:
Under
Limits, specify limits for the profile
insulation.
You can select plane, surface, or panel insulation as a limit.
You can also add offset from the selected
limits or extremities, by entering the offset values or using the handles in
the
3D area.
-
Under
Material & Thickness, specify the material
and thickness for the insulation.
Note:
If a material table is set in
Data Setup, the materials appear in the
Material list. Otherwise, you can click
More... to import or search the required
material.
-
Click
OK.
The insulation is created.
For stiffeners, the insulation is created properly taking into
account the stiffener positioning type (Normal to plate
or
Along plane).
If the stiffener's limits are modified, the profile insulation is
updated accordingly.
- Optional:
To edit the insulation, select the insulation feature and click
Structure Profile Insulation
on the
context toolbar.
Notes:
- A proper context
must be active.
- In physical product
context,
- You cannot edit
an insulation feature which is created under 3D part other than insulation 3D
part.
- You cannot edit
an insulation feature, if there are multiple insulation features created under
the same insulation 3D part.
- The PLM type list is
unavailable in edit mode.
|