Unsymmetric Iterative Linear Equation Solver
The unsymmetric iterative linear equation solver can now solve problems with
strongly unsymmetric modeling features; for example, models with a high contact friction
coefficient and some material models that cause an unsymmetric system
matrix.
The iterative linear equation solver can solve strongly unsymmetric problems
using a newly developed Krylov iterative solver (FGMRES) and unsymmetric
preconditioners. The new unsymmetric iterative linear equation solver can solve strongly
unsymmetric problems that the iterative solver using symmetric preconditioners cannot
solve. It can also solve weakly unsymmetric problems faster than the iterative solver
using symmetric preconditioners.
Benefits: This capability improves the iterative solver performance for models with
strongly unsymmetric modeling features.
Variable Bead Width and Bead Orientation in Additive Manufacturing
Processes
For thermomechanical analyses of FDM- and LDED-type additive manufacturing
processes, you can define material deposition and moving heat sources with varying bead
sizes and orientations. You can also define material removal.
Previously, the bead width and orientation for material deposition and a
moving heat source in an additive manufacturing simulation were fixed. Now you can
simulate complex additive manufacturing and welding operations using parameter tables to
specify arbitrary three-dimensional motions of the toolpath with varying bead
orientations and bead widths.In addition, you can now use element progressive
activation to specify material removal. The material removal functionality also
supports varying bead width and bead orientation. This allows you to define complex
three-dimensional cutting operations.
Benefits: The ability to vary both the bead width and bead orientation in FDM- and
LDED-type processes expands the range of additive manufacturing simulations you can
perform.
For more information, see
Thermomechanical Analysis of FDM- and LDED-Type Additive Manufacturing Processes
Machining and Material Removal Process
Stress Intensity Factor–Based Fatigue Crack Growth Laws
Stress intensity factor–based fatigue crack growth laws are now available for
enriched elements.
Previously, fatigue crack growth laws were based only on the strain energy
release rates. You can now specify a mode-mix formula for computing the effective stress
intensity factor based on the following:
- The Irwin mixed-mode fracture criterion.
- A tabular form to support multiple piecewise linear log-log (crack growth rate
versus effective stress intensity factor range of a load cycle) segments.
- A user-defined crack growth criterion using user subroutines in a fatigue crack
growth analysis.
The stress intensity factor–based laws are not available for crack propagation
or debonding along initially partially bonded surfaces where the strain energy release
rate–based laws are more relevant and should continue to be used.
Benefits: Stress intensity factor–based fatigue crack growth laws expand the modeling
capabilities available in Abaqus/Standard.
For more information, see
Linear Elastic Fatigue Crack Growth Analysis
Modeling Discontinuities as an Enriched Feature Using the Extended Finite Element Method
Contour Integrals with Second-Order Tetrahedral Elements Based on the
Conventional Finite Element Method
You can now use second-order tetrahedral elements for fracture mechanics
studies based on the conventional finite element method.
You must specify a small radius within which rings of elements are identified
in a model for fracture mechanics studies. A refined mesh is required to define the
rings of elements around the crack front, especially in a region near the external free
surfaces.You can now request field output for the contour integral for fracture
mechanics studies based on the conventional finite element method.
Benefits: Contour integrals with second-order tetrahedral elements based on the
conventional finite element method expand the simulation capabilities for fracture
mechanic studies.
For more information, see
Contour Integral Evaluation
Adjoint Sensitivities for a Static Analysis in Abaqus/Standard
Enhancements for adjoint sensitivities include new design responses, shape
sensitivities for additional element types, a new user subroutine for user-defined
element design response, and a set of additional stress-based element design
responses.
You can now request design responses and adjoint sensitivities for Neuber and
Glinka plasticity correction measures, which approximately account for the effects of
plasticity in structural design optimization studies based on linear analyses with a
purely elastic material response. This capability is useful in design applications where
plasticity effects are important, but a full nonlinear analysis that includes plasticity
is too expensive computationally. You can utilize this approximate approach during the
initial phases of a design cycle to select one or more candidate designs for more
detailed analysis.You can request adjoint shape sensitivities for a wider class of
elements that include hybrid, modified, modified-hybrid, axisymmetric continuum,
axisymmetric continuum with twist, and membrane elements. This extends the class of
design applications for which the adjoint sensitivities, computed by Abaqus, can be used as part of a design optimization workflow involving either Tosca or an
external optimizer. For example, axisymmetric hybrid elements are often used for
applications such as door seals made out of almost incompressible elastomers.
In
addition, you can now define your own element design response, based on either the
stress or the plastic strain tensor, through a new user subroutine. This capability
significantly expands the scope of element-response based designs and allows you to
define, for example, various failure measures as responses and to set constraints on
such measures.
Finally, you can now request response and adjoint sensitivities
for both the maximum and the minimum principal stress and the signed von Mises stress.
The maximum principal stress is an important measure for design applications involving
nominally brittle materials, while the signed von Mises stress is utilized in civil
engineering applications involving concrete as well as some fatigue applications using
metals.
The Neuber and Glinka design responses can be helpful during the design
phases of automobile parts. The figure below highlights a panel of a full
body-in-white model (courtesy of the Public Finite Element Model Archive of the
National Crash Analysis Center at George Washington University). A Tosca-Abaqus design optimization workflow minimizes the effects of the material plasticity for
the panel under different loading conditions by carrying out a purely linear elastic
multiple load case analysis while minimizing the Neuber effective plastic
strain.
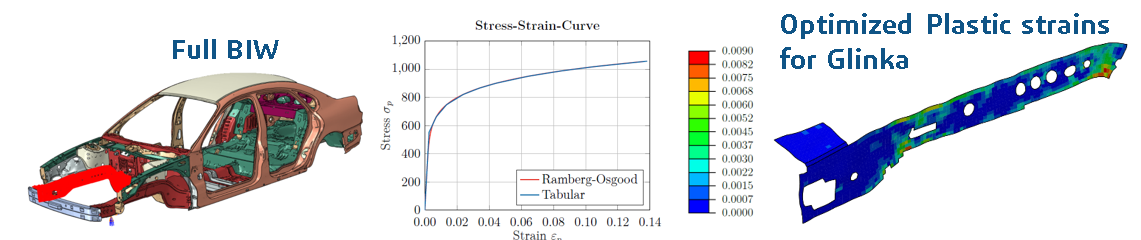
Benefits: Enhancements for adjoint sensitivities expand the modeling capabilities for
Abaqus/Standard.
For more information, see
Adjoint Design Sensitivity Analysis
Adjoint Shape/Bead Sensitivities for a Transient Dynamic Analysis in Abaqus/Standard
You can now request design responses for implicit transient dynamic analyses
and the corresponding adjoint sensitivities with respect to shape and bead design
variables.
You can output the design response and corresponding adjoint sensitivities
from Abaqus for use in your own design modification approaches. The figure below shows both the
initial (left) and the optimized (right) design of a plate, based on a combined Tosca-Abaqus design optimization workflow. The optimized design results in 65% lesser deflection
under a given transient load compared to the initial design. Thereby, it yields an
increase in the dynamic stiffness of the structure by almost a factor of three.

Benefits: This capability expands the coverage of the adjoint transient dynamic
sensitivities and benefits workflows such as concept design for crashworthiness, design
for dynamics of machinery and compliant flexible dynamic mechanisms, and the behavior of
electronic equipment in drop tests.
For more information, see
Adjoint Design Sensitivity Analysis