Problem Description
The two parts that will be assembled in this example are shown in the figure below. The clip is
51 mm long and 14 mm wide, and its three prongs are inserted into the buckle. The
buckle is 37 mm long and 14 mm wide. The bottom face of the buckle is fully
constrained, and the clip is free to move only in the z-direction. The clip and
buckle are made of ABS plastic, which is assumed to be a linear elastic and
isotropic material with a Young's modulus of 2 GPa, a Poisson's ratio of 0.394, and
a density of 1020 kg/m3. The model is meshed with the default quadratic
tetrahedral elements and a mesh size of 2 mm. The clip is inserted in the buckle by
moving it –14 mm in the z-direction.
Workflow
The workflow diagram below provides an overview of the example. The diagram shows the apps
that you use as you perform the steps in sequence. Clicking a number in the diagram
opens its corresponding step in the example.
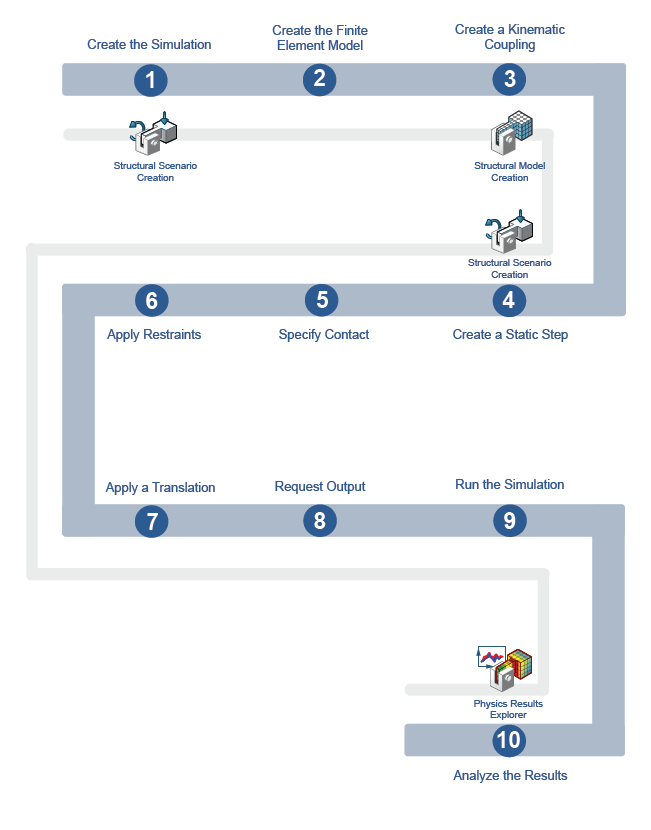
|
Task |
Description |
1 |
Create the Simulation
|
Create the simulation by first importing the model into the 3DEXPERIENCE platform and then opening the model in the appropriate app. |
2 |
Create the Finite Element
Model
|
Use a finite element model (FEM) representation of
your geometry to perform the simulation. |
3 |
Create a Kinematic Coupling
|
Use a coupling to apply a load to represent
pushing the clip into the buckle and to measure the insertion force.
|
4 |
Create a Static Step
|
Use a step to determine the nature and sequence of
events in a simulation scenario. |
5 |
Specify Contact
|
Specify contact interactions in your model to
define the behavior of the simulated response when the selected
surfaces come into contact. |
6 |
Apply Restraints
|
Apply restraints to define the directions your
model can and cannot move during the simulation. |
7 |
Apply a Translation
|
Use an applied translation to specify the distance
the clip is inserted into the buckle. |
8 |
Request Output
|
Create an output request for the coupling.
|
9 |
Solve the Simulation
|
Run the simulation to solve for the insertion force. |
10 |
Plot the Force vs. the Coupling
Displacement
|
Display simulation data in a history plot with
displacement as the independent variable. |
Complete the workflow steps in the order in which they are listed. Deviation from the
instructions associated with each step might cause model or scenario errors, which
might prevent convergence of the simulation.